Weed Go Well Together
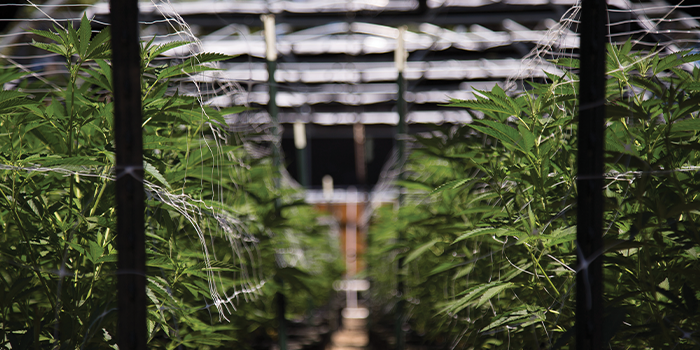
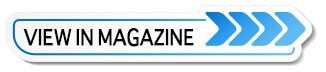
SPRAY FOAM MAGAZINE – Cultivation and manufacturing facilities are increasing in numbers as many states allow licenses to companies wanting to specialize in cannabis crops.
To succeed in this business, and to have a plentiful harvest, the design of the grow house and the correct materials installed in them is vital. The SFMT (Spray Foam Magazine Team) first covered this subject in our 2019 Show Issue and wanted to circle back to this growing industry. Eager to find out more, we headed to Missouri to chat with a company who recently sprayed an impressive cultivation facility.
Founded in 2009, Installtec, Inc. quickly set themselves apart from the pack by building trusted relationships with general contractors, architects, and owners. They not only put the quality of their work first, but also their pursuit of finding employees that embody their ideals of hard work and lasting relationships. This has propelled Installtec to be regarded as one of the top contractors in the various scopes they provide.
Installtec installs spray foam, in addition to spray-applied fireproofing, finished acoustical insulation, fire-rated intumescent paint, various specialty coatings, and plaster application. They are strictly a commercial outfit, with few exceptions. Given Installtec’s reputation as a high-quality subcontractor, the size of the project, and their background knowledge of the specific needs of indoor cultivation centers, they were the obvious choice of the general contractor for Vertical Enterprise, LLC.
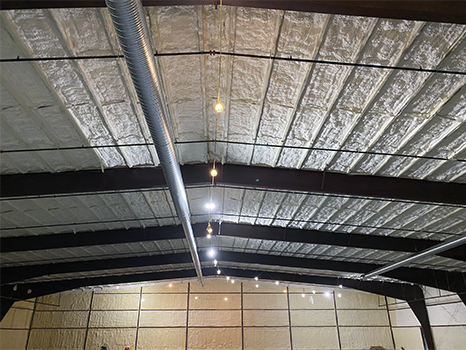
The finished envelope (walls and roof deck) of the Vertical Enterprises center in St. Joseph, MO gives a total R-value: R28.
Installtec’s Spencer Plumb highlights, “The federal government offers tax credits to builders using spray foam insulation on their projects, residential and commercial alike. We have seen energy savings of up to 50 percent on some projects, this number varies depending on other variables like building design, and how much spray foam was used on the project. I thought this was noteworthy considering having a low carbon footprint is becoming more and more important for companies in all sectors.”
Finkle Williams was the architectural firm that included spray foam at the envelope of the building. It was originally spec’d for four inches of closed-cell spray foam. However, the general contractor wanted to bring the price down, so Spencer Plumb of Installtec wrote a new spec that included a combination of closed- and open-cell foam, to achieve the desired air/moisture/vapor barrier, as well as the desired R-value at a lower cost to the owner. A well-insulated and well-sealed envelope for the grow rooms resembles that of a walk-in cooler with the wall and ceilings constructed of insulated metal panels inside a building structure.
Cannabis thrives in controlled environments, and a cultivation facility that can achieve this will have an advantage in producing a great crop and will also help meet firm state regulatory requirements. Aspects connected to quality control and production are:
A controlled environment (temperature, humidity, light, water, nutrients, carbon dioxide, and airflow) leads to maximum yields and product quality
The ability to grow crops year-round in any climate
Control of odor associated with the plant
Isolation from insects, mold spores, pollen, birds, and other pests and contaminants.
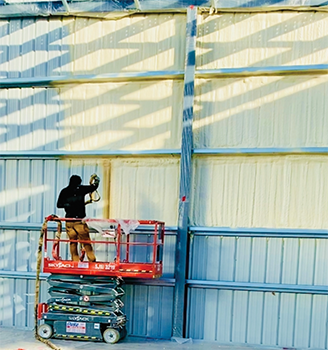
Before a project commences, safety is discussed and is paramount to the Installtec crew. Workers are required to wear standard PPE for commercial job sites which includes: a hardhat, level 3 cut resistant gloves, steel toe boots, and company issued high-vis shirts. In addition to the standard PPE, their SPF sprayers, or anyone on their site, are required to wear a full-face respirator with organic vapor cartridges (changed every 8 hours they are exposed to air), a full body spray suit, and disposable chemical resistant gloves. They are also given the option to use a fresh air exchange suit/hood if they desire, but according to Installtec, most prefer the respirator.
Installtec assigned two crews, with three workers to a crew, to spray the structure, which has a footprint of 62,000 sq ft, with the building dimensions being 130ft x 430ft with 20-ft high walls. They had two of their spray rigs on site; one was an enclosed trailer housing a Graco E-30 Reactor 2, the other was a box truck housing a Graco H-50. Both rigs used a Graco Fusion AP gun to do the spraying.
The crews sprayed a total of 78,000 sq ft including the entire envelope of the building, walls, and the roof deck with two inches of NCFI’s 2.0 lb InsulBloc to achieve an air/moisture/vapor barrier. The substrate sprayed was corrugated metal panels. They then sprayed four inches of NCFI’s open-cell foam over the top of the closed-cell spray foam to add R-value, as well as acoustical suppression.
The crew worked at night during the winter, which made circumstances extremely difficult. The metal they were spraying it to was basically the temperature of the outside air; so anywhere from 10 degrees to 40 degrees Fahrenheit. This makes spraying harder and time consuming because they would first have to spray a flash coat to warm up the metal enough to spray the full thickness.
Plumb commented, “Ask any spray foam installer and they will tell you that spraying cold metal is a pain because the polarized temperatures of the reacting spray foam and the cold metal cause the spray foam to delaminate, and sometimes just pop right off the substrate. Additionally, there was no roof system on the top side of the roof deck, so even if the crew wanted to run heaters they could not as it would produce condensation, which makes spraying impossible. The substrate must be 100 percent moisture free.”
The Installetec team noted the advancements in technology and formulas that manufacturers have adopted have greatly reduced the odor that may be created by the product. They also use negative air machines to ensure that they are removing any contaminated air from inside the building to the outside. The Installtec crews are often one of the first sub-contractors on a site, once the main structure is in place. This means that they have completed their tasks many months before the building is even ready to turn over to the owner.
With the cure time for spray foam ranging anywhere from eight to 24 hours, depending on temperature, product, substrate, etc., any reaction happening between the two components of spray foam has come to a stop, and the foam is no longer emitting any unwanted by-product. As a company, Installtec will only spray HFO products. For many years, HFC blowing agents were once the standard in the spray foam community, however, many manufacturers have now switched to HFO blowing agents for environmental reasons, such as zero Ozone Depletion Potential (ODP), low Global Warming Potential (GWP), low conductivity, and non-flammable material.
Through the modernization of the spray foam manufacturing process, the right product choice, the proactive measures taken by the Installtec crews during the installation, and the length of time between the installation of the spray foam and the planting of the first harvest, there is a greatly decreased risk of transferring any odors or off-gassing to the cannabis plant.
The job took the Installtec crews roughly four weeks to spray, and this was all done during a second shift between 3pm-11:30pm when the area was clear of other trade workers. The hard work and dedication of the team and crew, resulted in the Vertical Enterprise project being a well-executed success, and proves that SPF is yet again a great temperature and humidity control material. Installtec delivered on a well-planned and well-executed project, proving once again that coupling a reliable and qualified SPF installer with a superior material resulted in a great joint effort.
Disqus website name not provided.