It’s Rocket Science
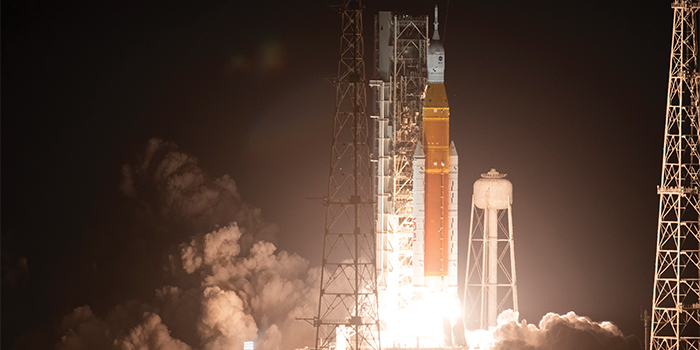
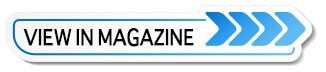
Spray Foam Magazine – During 2020, the Spray Foam Magazine team spoke with NASA about the pending Artemis l launch. Discussing the SLS Rocket core stage, and the backbone of the rocket, we investigated how SPF would be playing its part in this historic event. The core stage is 212 feet tall and 27.6 feet in diameter holding 2.3 million pounds of propellant, the cryogenic material that fueled four engines to produce two million pounds of thrust to launch the spacecraft into deep space at a speed of MACH 23 (faster than 17,000 mph in just 8.5 minutes).
Comprised of five sections, the core stage had tanks that held 733,000 gallons of cryogenic materials, liquid hydrogen, and liquid oxygen. Each section was insulated with SPF, helping keep the rocket’s propellant, the liquid hydrogen and liquid oxygen, cold enough to remain in a liquid state. These cold temperatures provided the engines with properly conditioned propellants, vital to launching the rocket.
Artemis l successfully launched on November 16th, 2022, the agency's first big step toward returning astronauts to the lunar surface. We recently caught up with Michael Alldredge, the SLS Stages Thermal Protection Systems Design Lead, to find out how the foam performed during the ‘Wet dress rehearsal.’
There were several prelaunch challenges NASA had to get through, which is to be expected with a project as complex as Artemis l. A rocket of this magnitude and complexity had never launched before. NASA also takes the materials on the projects very seriously, researching and testing them to the extreme. Naturally, the Spray Foam Magazine Team (SFMT) wanted to hear how the specifically formulated closed-cell spray foam performed during testing. The Green Run hot fire testing series was completed in March 2021 and consisted of the core stage's four RS-25 engines operating for eight minutes, generating 1.6 million pounds of thrust, the amount of thrust needed on the launch pad at liftoff.
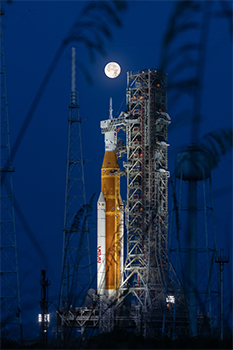
From a launch vehicle, a lot of the technology was carried on from the earlier Space Shuttle program, but like any starting point that is carried forward, it needed to be put back together in a new way. Therefore, Alldredge and his team of engineers had to understand what the vehicle was going to do with the additional advancements and how it would respond once the cryogenics were loaded onto the vehicle, “We were very happy with the SPF performance coming out of the ‘Green run testing.’ We built the vehicle in Louisiana and took it over to the Stennis Space Center in Mississippi where we did a full ‘Wet dress rehearsal.’ This is where we loaded the vehicle up with cryogenic fuel, cryogenic liquid oxygen and liquid hydrogen and we did a long duration hold to see exactly what would happen with the vehicle if we had to sit on the pad for a very long time. This really tested the spray foam insulation and all the components, letting us know exactly what the vehicle would do when it was exposed to extremely cold temperatures,” explained Alldredge.
Following the “Cryogenic test,” the team measured and analyzed the vehicle, inspecting for any cracks in the foam. Up until that point, the team had only performed bench level testing with this testing being full-scale. The next stage of testing was the ‘Hot Fire,’ where the team loaded up the vehicle again, put all the engines on and ran for the full duration of 500 seconds, then went back to look at the data.
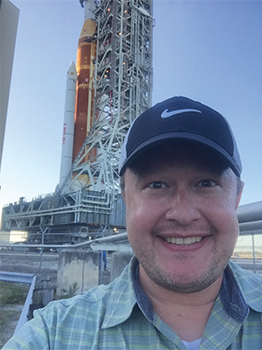
“I have been with this project since 2013. When Artemis 1 launched, I was in the control room watching the screen and the hydrogen burn off at the bottom and then it launched. At the eight-minute mark it separated, and the core stage was complete. Every step, people were clapping, cheering and high fiving. There is no other way to demonstrate that emotion. Here is this machine we spent so much time living with and working with, The meetings, the challenges, the testing and the ultimate success. For those brief eight minutes everything was perfect.” – Michael Alldredge
From an insulation standpoint, there is a huge temperature swing it had to cope with. The team focused on when the foam got extremely cold, keeping in mind in certain areas the foam was less than an inch thick. On the hydrogen tank the insulation is about one and a quarter inch thick. Outside of the vehicle the air temperature could range from 60-80 ° F while at -423° F for the liquid hydrogen temperature. When contracting and condensing moisture out of the air, physics can do some strange things. The team would ask numerous questions, for example, what happens when small cracks appear and start to pull in moisture out of the air? Will it vent back out or will there be an energetic event? These kinds of questions were imperative, as the last thing the team wanted on launch day would be for the foam on the vehicle to be popping off or cracking. Testing the foam to the extremes enabled Alldredge and his team some very informative data as to how the vehicle would perform.
Alldredge did expect the cracks, due to the liquid hydrogen temperature being close to absolute zero. At this temperature, materials become very brittle. However, the team were very impressed with how the SPF handled these extreme temperatures. In terms of patterns in the data received, Alldredge clarifies, “It’s really a function of how the cryogenic fuel is loaded onto the vehicle. Typically, we start with the liquid oxygen (or LOX) tank, instead of the hydrogen, due to how long it takes us to load that much material. If you look at the vehicle from a thermal imaging standpoint, you will see the feedlines running up the side where the liquid oxygen gets cold first. The cold temperature ran up the side of the vehicle into the LOX tank. Then we saw a flow of hydrogen on board and the large hydrogen tank on the bottom getting cold. Basically, it got cold from the bottom up.”
The team knew that the aluminum on the vehicle was going to contract too. Therefore, the brackets and joints need to move as well. So as the vehicle contracts and constraints, due to the cold, there is not a mechanical load that may cause a bracket to fail. All these factors are moving just to deal with the thermal shrinkage of the vehicle. In terms of the foam, this had to shrink with the vehicle, and by spraying directly onto the hardware, it needed to compress and expand too. The SPF applied was a unique formulation with the ability to do those things.
In some of their spray foam applications, Alldredge and his team noticed cracks that started to appear in the foam, which were driven by underlying stresses in the mechanical structure itself. The foam must go where the metal is, but at some point, something can fail.
From the previous Space Shuttle program, NASA had experience with small cracks in the foam, and depending on where they are located deciphered if they were okay or not. One of the things the team had to deal with and great conversation points, were the cracks they saw on the flange, where the liquid hydrogen tank and the intertank meet. The inner tank is very stiff compared to the liquid hydrogen tank, which is contracting and expanding.
All the motion of the liquid hydrogen tank coupled with the rigid inner tank was the main discussion about cracks in the foam and if there was any risk. The team also kept in mind that by the time the rocket launched, they had already loaded cryogen fluids onboard numerous times. The testing of the foam had been intense, with the team thoroughly recycling the rocket several times. The rocket also sat outside Stennis Space Center for just over a year, dealing with the diverse seasonal temperatures. With the same pattern of weathering events occurring when the vehicle was transported to Florida. The team reviewed and assessed the foam for any risks. Asking themselves, is our risk lower to leave it alone than the potential for opening it all up and finding that it will take a long time to repair something when it was good enough to begin with.
The team had a schedule which was not only driven by NASA but the moon and the Orion capsule. They had to make sure that the vehicle was available to fly when the target, which in this case was the moon, was where they needed it to be. They therefore had to weigh up all the risks, basically, doing something versus not doing something. When Artemis l did launch, the team did see some foam debris but nothing from a standpoint where the team were surprised.
One of the unique uses of 3D printing technology integrated with foam on this program was applying it to molds, used to form the foam. In addition to using automated and manual spray foam, the team used pour-in-place foam applications. This was a technology that was in its infancy during the Space Shuttle program in the 70s and 80s. The team were able to take 3D components like valves and develop 3D prints. This enabled the team to not only develop the process by which to put the foam on, but answer questions like, how much foam do they mix up, where do they inject it, and where is it going to vent. Being able to 3D print the part and the mold gave the team time to practice with the foam, thus saving time closer to the launch date.
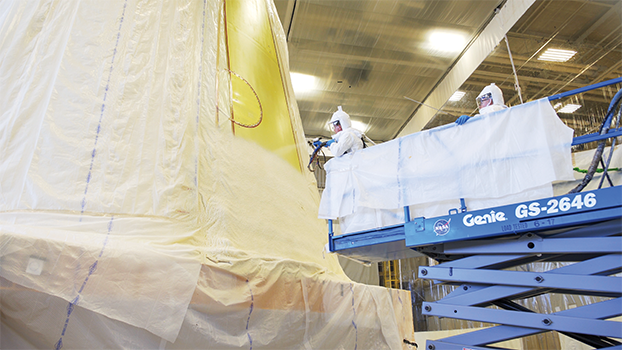
The foam is a lightweight variation of closed-cell polyurethane foam and contains an HFC-245fa blowing agent. NASA works closely with trusted vendors on the formulation of their unique type(s) of SPF. Over the years, NASA has developed a good rapport with a few key foam manufacturers whom engineers collaborate with to derive the perfect foam for their mission.
The question is, what does NASA do with the SPF data they received during testing and the launch of Artemis l? “Core stage number two and our second flight unit was in production, while we were getting ready to launch Artemis l. We are now in the process of completing our post data flight analysis. If we see things that are a big red flag we will go ahead and address those on the vehicle and discuss the risks and consequences of any findings,” clarified Alldredge.
The space business today could be viewed by many as being highly commercial. The “second race to space” was splattered all over the press in 2022 with China and Russia competing with the U.S. and tech entrepreneurs to extend space travel to new commercial heights. With so much competition, why is NASA still relevant? The simple answer is objective. The National Aeronautics and Space Administration (NASA) has already achieved inimitable scientific and technological accomplishments in space applications, human spaceflight, and space science. It is not an agency fueled by a potentially misguided view on space exploration disguised as entrepreneurs’ ego driven desire to conquer the final frontier. Built on the National Advisory Committee for Aeronautics (NACA), in addition to other government organizations, it is still viewed as the hub of U.S. civil aerospace research and development. This was proven once again when Artemis l, the largest rocket stage ever built, successfully fueled, and launched the world’s most powerful rocket known to humankind.
The SPF applied was tested to the extreme. From temperature fluctuations, contractions, expansions, and the elements. NASA’s plan is to have a crew on the Artemis II, by late 2023, and SPF will be helping to make history by being part of the first crewed mission around the Moon in half a century. Alldredge concludes by saying, “We are here to do exploration. This is where NASA belongs and how we push the technology, including spray polyurethane foam forward.”
For use by SprayFoamMagazine.com & Spray Foam Magazine
Disqus website name not provided.