Heat Shields and Beyond
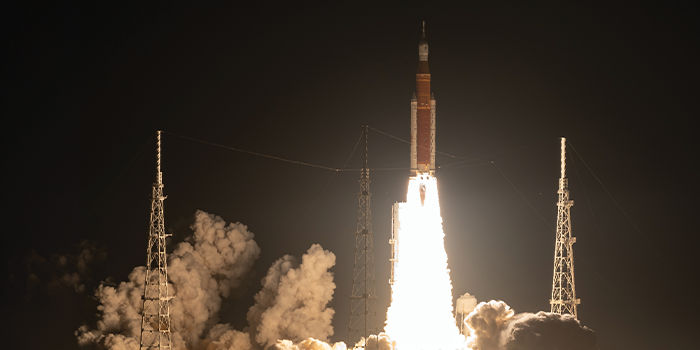
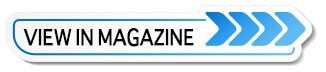
SPRAY FOAM MAGAZINE – Technicians at NASA’s Marshall Space Flight Center in Huntsville, Alabama, have applied spray foam as part of the thermal protection system to the Artemis III Launch Vehicle Stage Adapter (LVSA) for NASA’s Space Launch System rocket.. The SPF insulation is flexible enough to move with the rocket, but rigid enough to handle the extreme pressures and temperatures as SLS accelerates from zero to 17,400 mph and soars to more than 100 miles above Earth in just eight minutes. Spray Foam Magazine spoke with Greg Lawson, a Program Manager for the LVSA, and Lauren Fisher with NASA’s Thermal Protection Systems (TPS) team to find out more about their jobs and the application.
Spray Foam Magazine: Please describe your job role.
Greg Lawson: I am Teledyne Brown Engineering’s (TBE) Program Manager for the Launch Vehicle Stage Adapter (LVSA). I oversee the entire development, production, delivery, and support for the Artemis-I, -II, and -III LVSAs
Lauren Fisher: I’m a materials engineer working with non-metallic materials and the lead engineer for the thermal protection systems on the Launch Vehicle Stage Adapter (LVSA) for Artemis III.
SFM: What is the launch objective for Artemis lll?
GL: Artemis-III will provide the vehicle to carry the first woman and person of color to land on the lunar surface.
LF: In 1969 Neil Armstrong said, “That’s one small step for man, one giant leap for mankind,” and that giant leap started the journey to the first giant step for a woman, and the next giant leap for every kind. NASA’s Artemis missions, powered by the SLS rocket, are setting the stage for the first humans to explore the lunar South Pole. This is a difficult region to explore because of the extreme conditions. There’s so much to study in this region and NASA is working hard to make it happen.
SFM: Please describe the important role the LVSA plays in the Artemis lll launch?
GL: The LVSA plays the critical role of joining the core (first) stage of the rocket, to the second stage. The Adapter part of the LVSA name implies exactly what its function is. The second stage, which includes the Orion crew capsule, is a smaller diameter than the massive core stage. The LVSA makes the two stages fit together, so that the core stage can provide the lift needed for the smaller second stage.
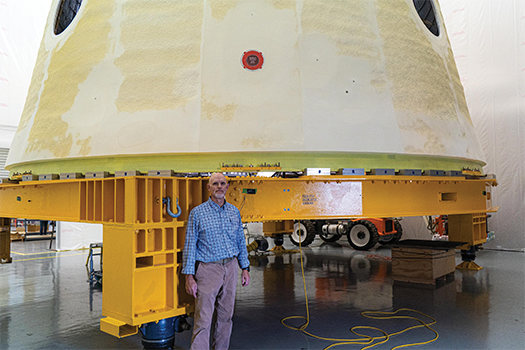
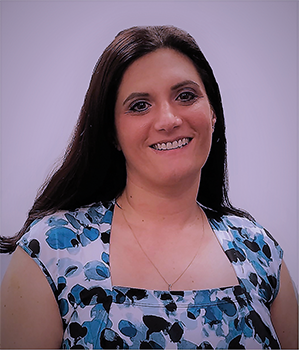
LF: The LVSA connects the core stage, which holds the fuel tanks, to the upper part of the rocket. It provides structural support for the separation system and protects various electronics and avionics devices from vibrations and other forces during launch and ascent. Basically, it keeps things together, in place, and prevents them from banging into things.
SFM: How did NASA and the engineering contractor, TBE (Teledyne Brown Engineering), work together on the LVSA?
GL: NASA and TBE worked together to determine the most cost-effective and technically superior insulation method that matched the capabilities. The Marshall Space Flight Center (MSFC) and TBE teams worked side-by-side, creating a dedicated cell, to spray the foam insulation and to develop the unique spray processes needed for LVSA.
LF: We had standing weekly meetings to coordinate the schedule and share production updates. We each had our defined roles and responsibilities and communicated well to make sure they had what they needed from us and vice versa. Our teams worked together on the production floor every day.
SFM: How was the LVSA integrated with the SLS core stage?
GL: The LVSA is integrated with the core stage in the VAB at KSC. The LVSA is shipped to KSC on the Pegasus barge and held in the High Bay in Kennedy’s Vehicle Assembly Building across from the core stage until the core stage is ready for the LVSA to be stacked. Then, the high-bay crane transfers the LVSA over the aisle and places it precisely on top of the core stage.
SFM: Can you explain the thermal protection system (TPS) applied to the LVSA and why it is so important?
GL: One of the features of the LVSA is that it protects the second stage engine (Interim Cryogenic Propulsion Stage or ICPS). The LVSA, due to its conic shape, has a forward-facing area that is subject to aerodynamic heating during the ascent through the atmosphere. Without insulation, heat from the aerodynamic friction would radiate through the LVSA and possible damage some of the sensitive second stage engine components or heat the engine’s fuel tanks beyond an acceptable level.
LF: The TPS applied to the LVSA is a closed-cell polyurethane spray foam insulation, kind of like what people might use to insulate parts of their house. We work with J6 Polymers for the spray foam applied to the LVSA. The foam protects the rocket from the heat of launch and provides structural support. The spray foam starts out as a light yellow when it is first applied to the LVSA and over time as it’s exposed to UV rays from the sun, it starts to tan and turns the burnt orange color we’re all familiar with.
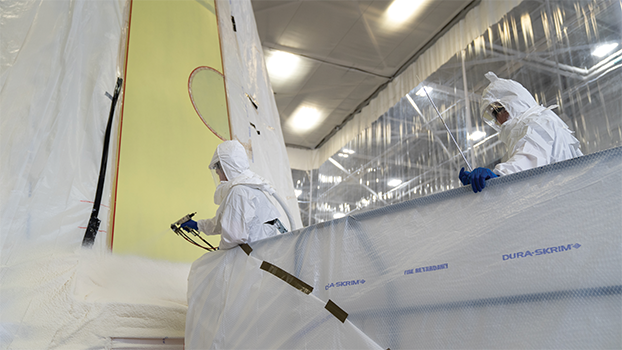
SFM: Is the spray foam applied to the LVSA the same as what is applied to the core stage of the rocket?
GL: For the most part, the spray foam on LVSA is not the same as that on the core stage. Some foams must be sprayed on a heated surface or must be sprayed by an automated system. MSFC didn’t have facilities to do either for an article the size of the LVSA. Trade studies indicated a different foam for LVSA, which led the MSFC and TBE teams to develop the special spraying processes and facilities for LVSA. The core stage does use some of the same foam as LVSA in some special regions and for some foam repairs, if needed.
LF: No, the LVSA is sprayed by hand and the large barrel part and domes of the core stage are sprayed by a robot. The domes are the same type of foam as is applied to the LVSA, while the tank part is sprayed with a different formulation of foam.
SFM: Can you describe the process of spraying the foam?
GL: The insulating foam was sprayed by hand, by a technician, in a mobile man-lift. The spray technician is joined by a lift operator on the lift platform, while a foam delivery system operator, on the ground, sets the spray parameters and monitors the spray during the entire process. The team also includes Materials Branch manager and Quality personnel to ensure everything goes as planned. It takes the technician about 45 minutes to spray each one of the 20 stripes on the LVSA. But since there is a time limit on the length of time that can elapse before the next spray pass is completed, the technician can’t simply start on the next stripe as soon as they finish one.
They must move over to another stripe region and begin that spray. Since adjacent stripes can’t be sprayed immediately, alternate stripe regions must be laid out, making the process a 10 + 10 stripe process, where each alternate area must be masked and prepared for each set of 10. Then, before the second set of stripes can be sprayed, the edges of the first set must be beveled, to avoid a deep spray corner, and a special tie-coat must be applied to the area where new foam will bond with the previously sprayed stripe. Each stripe on the LVSA is about 28 feet tall and increases from about two feet wide at the top to about five feet wide at the bottom. The bottom edge of the foam is also sprayed extra thick to be able to match thickness with the closeout spray that will be done at Kennedy Space Center (KSC), to cover the core stage and LVSA mating flange.
LF: The foam thickness varies from approximately 2.7in at the bottom and then tapers up to approximately 0.70in at the top. The technicians also check the thickness with a rod, like a dip stick for checking oil. The rod is inserted into either side of the lane, not directly into the section being sprayed, and the thickness is checked against the laminate tip of the rod. This is used as a marker so they can make sure they are hitting their thickness requirements as they spray.
After the foam has been applied to the first 10 alternating spray lanes, the edges are cleaned up by trimming and sanding. Each edge is sanded down to a bevel shape and then an adhesive is brushed on the edges of the lane. This helps promote adhesion of the foam when the adjacent lane is sprayed.
SFM: What was the special tool used to apply the foam, and how is it different to a gun a spray foam contractor would use?
GL: The spray gun used to apply the foam is specially made for this process. The closest thing that most people would recognize is the foam guns used in the shipping industry to create custom-formed packing materials. It provides for two foam components to be mixed at the exit nozzle of the gun. Those two components mix to immediately begin the curing process. Once sprayed, the foam undergoes an expansion, much like the foam you use at home to insulate around pipes or openings in a wall.
SFM: Now that the foam is applied, what happens next in the process i.e., will the foam go through testing?
GL: Immediately before a stripe is sprayed, and immediately after, a witness panel is sprayed. Those two witness panels are taken to a lab, where five samples are taken from each panel. Those samples are tested for materials properties. If all the samples pass the tests, the stripe is certified as “good.” If any of the samples fail, additional tests are run to determine the reason for failure. If the additional tests fail, some testing can be done on the LVSA itself, to get a true measure of the actual vehicle foam. No spray foam on any LVSA has failed all the tests.
LF: After the foam was applied, trimmed, and sanded, and went through final inspections, it was moved to another building to continue production.
SFM: How have you personally felt about being part of this project?
GL: Being involved with the Artemis program has been awe inspiring. My father built components for the Lunar Excursion Module for the Apollo program. It is almost surreal to think that I will be involved with the next generation of hardware that will return us to the Moon.
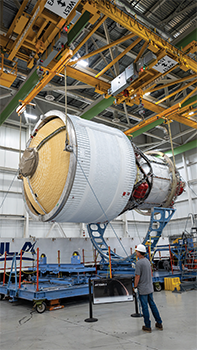
LF: Very proud. It was a challenge and quite the learning experience, but also very fun. I work with great people who do a phenomenal job every day and I’m lucky to not only have had this experience, but to have shared it with such an amazing team both NASA and Teledyne. I said once before that having been born and raised here in Huntsville, I’ve always felt like I was a part of the history of NASA, and now getting to work on the LVSA for the Artemis III mission, I’m a part of the future of NASA.
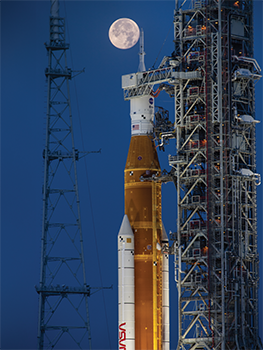
SFM: Will spray foam be used on any additional parts of Artemis lll?
GL: To my knowledge, the LVSA and the core stage are the major users of spray foam insulation. Some other parts of the rocket use cork insulation and some remain uninsulated.
LF: After it is connected to the core stage the section between the two will be filled in by hand spraying.
SFM: Is there anything else you would like to add about this project?
GL: The SLS/Artemis Program is a massive undertaking – building NASA’s newest, largest rocket. Just the size of all the elements presents daunting challenges, but NASA and the contractor teams, including Teledyne Brown, have risen to these challenges. There have been design challenges, production challenges, facility challenges, and logistics challenges, but the hard work and creativity of all the engineers, managers, technicians, and suppliers has provided the teams, NASA, and the country an endeavor of which we can be proud!
LF: A lot goes on in the background. For one, we make sure that everyone has the proper training to do their jobs and that includes all safety training. That’s just one of many things we do to make sure everything is in place and that we are set up for success. There are multiple teams working together like quality assurance, transport/lifting, environmental, scheduling, procurement, support staff for all these different departments, to make sure we are set up for success.
For use by SprayFoamMagazine.com & Spray Foam Magazine
Disqus website name not provided.