Efficiency
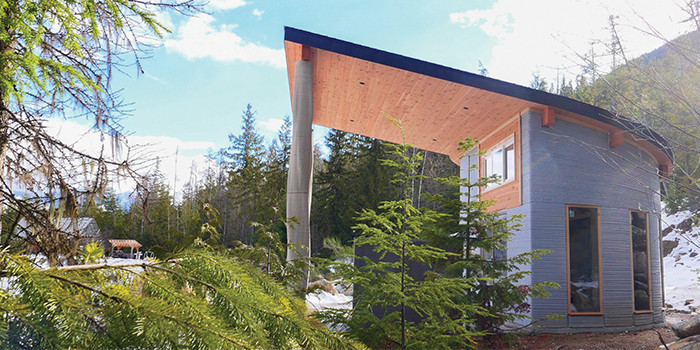
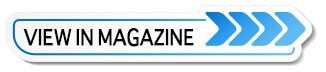
Spray Foam Magazine – Winter 2021 – TAM (Twente Additive Manufacturing) are pioneers when it comes to 3D concrete printed structures, known as 3D printed concrete (3DCP). With the use of this modern technology and assistance from materials like spray polyurethane foam, these concepts will not only help revolutionize the construction industry but are structurally sound and energy efficient too.
TAM was founded by six like-minded friends with backgrounds in industrial automation and skateboard manufacturing. When the business was first developed three of the members were living in the Twente region of East Netherlands, which is where the name was adopted. Their head office is still based there, however, there are now subdivisions in Canada, Germany, and the United Arab Emirates.
One prime example of their work is the 3D printed Fibonacci House situated in Procter in the regional district of Central Kootenay, BC, Canada. It also happens to be the first-ever permitted 3D concrete printed house in Canada. The word Fibonacci derives from the medieval Italian mathematician, Leonardo Fibonacci, who believed that calculation was an art form with balance, order, and harmony being created. This sequence is still thought to be relevant today with humans in general preferring order and symmetry for structures to be aesthetically pleasing. Many of the 3DCP buildings to date have been box shaped designs, but this house uses the Fibonacci curve concept and is a great example of how 3D concrete printing has progressed.
For this project, TAM requested spray polyurethane foam and pour-in-place polyurethane foam on and in several features of the structure. Insulating the footing and the surrounding sub ground area for frost protection allowed them to use a monolithic slab/floor that was shallower than the minimum code prescribed depth for the region. The project benefited by having a single concrete placing for both footing and slab.
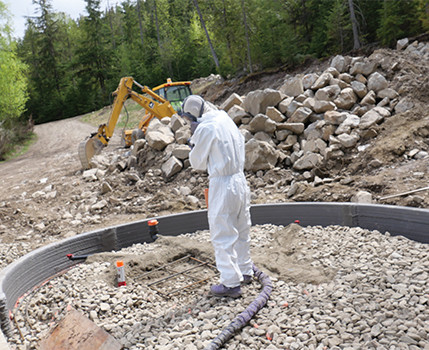
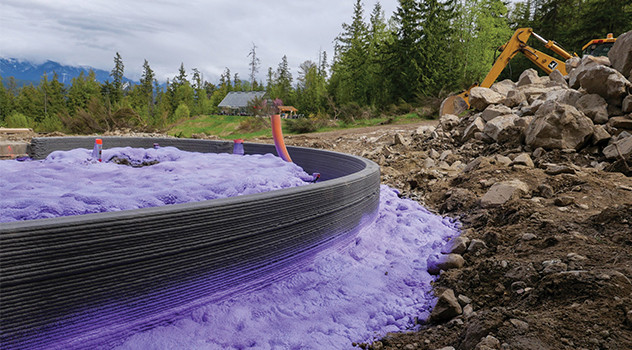
The 3D-printed foundations for the Fibonacci House were foamed with BASF WALLTITE for frost protection.
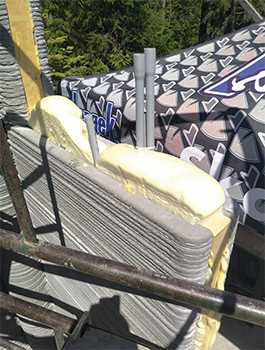
The walls were left hollow and Demilec Eco-Put-352 pour-in-place foam was installed inside.
This saved the crew, a trip from the local ready-mix plant, overall volume of concrete materials, additional form work for separate footings, personnel on site time, and an engineering inspection.
The Fibonacci project is a collaboration between TAM and Kootenay Lake Village, a real estate project in the catchment basin of Nelson British Columbia. Located in the Regional District of Central Kootenay, which is a form of rural municipality management who allowed the construction under the BC building code. The engineering was performed by EffiStruc Consulting Inc. who also helped to get the building accreditation. This is the first house for TAM to be accredited in Canada. The site where the Fibonacci House is situated is also scheduled to receive several additional 3D-printed buildings with the objective to make more complicated free-form structures and better cost and energy usage efficiencies.
The foundations for the Fibonacci House were even printed with the ground being spray foamed with BASF WALLITE to insulate the concrete slab. Printing took place on a facility within the grounds of the house meaning a quicker assembly time onsite and lower energy consumption. They applied the printed concrete over the foundation in addition to pouring in regular concrete to ensure the build has structural strength and integrity.
This method of poured and 3D printed concrete is carried throughout the house. Basically, using new technology and combining older methods to meet building code standards and ensuring code officials that the structure would be safe.
The roof is timber framed, a great juxtaposition to the 3D printed main shell of the building. The TAM team highlighted the fact that the entire roofing system was foamed using BASF WALLTITE 2lbs. The closed-cell purple foam is easily sprayed with even hard-to-reach areas being fully sealed. The TAM team pointed out that the additional cost of using spray foam was offset by omitting several steps and features that would otherwise be required. The use of alternate insulating materials, vapor barriers, soffiting, and labor to install in many of the irregularly shaped small spaces of this house. Using a Graco H-25 the two-man crew sprayed three inches to 300 sq ft of roofing space, applying one set of foam to the wood substrate. Once the foam was cured, they covered it with drywall.
The walls were left hollow for placement of a pour-in-place polyurethane product with TAM choosing, Demilec’s, who is now owned by Huntsman Building Solution, Eco-Pur-352. According to the team at TAM this product significantly stabilized and bolstered the integrity of their 3D printed hollow wall components and secured them together across both vertical and horizontal expansion joints.
By implementing 3D concrete printing and energy efficient products like spray foam insulation in successful projects like the Fibonacci House, the construction industry is starting to realize that old building materials are starting to be replaced by methods that are quicker, easier, and efficient to apply.
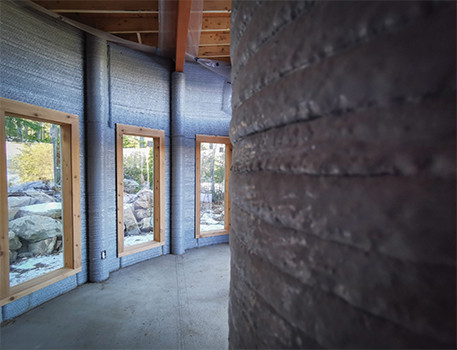
The 3D concrete printing uses the exact quantity of materials needed as opposed to the traditional methods where bulk orders are often placed. The pour in-place foam in the walls of this house and spray foam were also to help with structural strength in the attic due to the foam being rigid and dense once sprayed. In addition to acting as an air and moisture barrier.
The team at TAM was happy with the outcome and how spray foam performed on this project saying, “The unique shapes we can produce with 3D printed concrete is difficult to insulate conventionally. The spray foam lends itself well to these irregularly shaped objects.”
This tiny 3D concrete printed house is now available to rent on Airbnb as a fundraiser to help World Housing (.org) continue on their plight to help solve the housing crisis.
Disqus website name not provided.