Building Codes Continue to Change
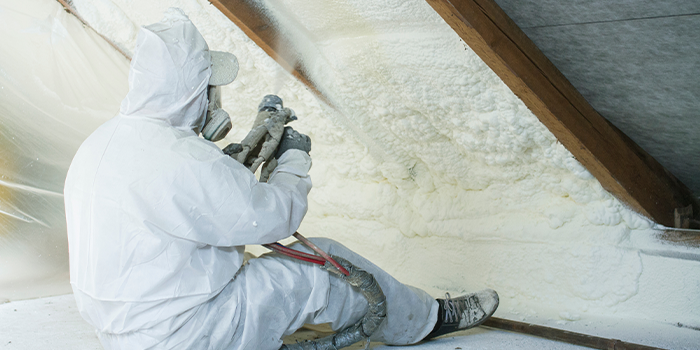
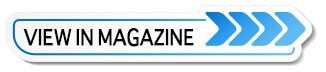
Spray Foam Magazine – Have you heard the rumor that when you create an unvented attic in some southern states, like Georgia, that R-20 spray foam on the underside of the roof deck is code compliant? Well, this is true, but there are conditions… so, let’s talk about how the code compliance for spray foam in an unvented attic in the state of Georgia works.
Why Georgia? Well Georgia is the only state that I am aware of that has adopted energy code language with R-values directly related to air-impermeable insulation in unvented attics.
So here we go, the Energy Code, also known as the IECC, offers three methods for building envelope and energy code compliance for residential buildings:
- The Prescriptive Requirements
- The Performance Method
- and the Energy Rating Index
The prescriptive requirements are the code minimums that are documented in the building code. These are the specific requirements, broken down by climate zone. When you install a specific R-value or U-value, like putting R-13 in a wall in Climate Zone 3, you are simply meeting the prescriptive code requirement. Essentially, you can meet energy code compliance by following a checklist of minimum values specified by the code – this is the prescriptive method.
The performance method allows the builder to use simulated energy performance to make energy trade-offs if they show that the actual design they are building, called the proposed design, has an annual energy cost that is less than or equal to the annual energy cost of the prescriptive code minimum. The most common way to document performance-based compliance is with the use of energy modeling software.
Finally, the Energy Rating Index, or ERI, is a calculation where a rating for the building is calculated on an index scale of 0 to 100, which compares the proposed design to an ERI reference building. The Energy Rating Index of the proposed design must outperform the ERI reference building by an identified percentage based on climate zone.
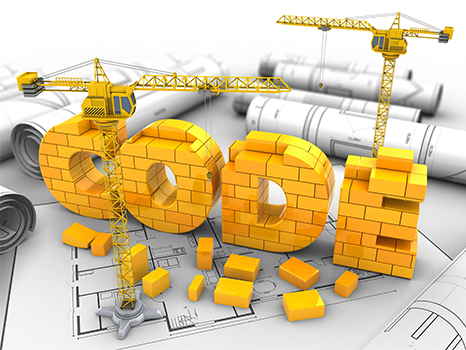
Now that we understand the code compliance options, let’s look at the specifics of the example I mentioned before – an unvented attic in Atlanta, GA, Douglas County, Climate Zone 3.
The key code sections that apply are IECC R402 and IRC 806.5.
The prescriptive requirements are:
- Minimum R-38 Ceiling Value (from IECC R402.1.2)
- Spray foam (air-impermeable insulation) in direct contact with the underside of the roof deck
- Minimum R-5 air-impermeable insulation for condensation control (from IRC 806.5)
Following these guidelines would require approximately ten inches of open-cell spray foam or approximately five and a half inches of closed-cell spray foam (depending on specific product R-values) in direct contact with the underside of the roof deck to meet the prescriptive code requirements.
If you want to create an unvented attic with less spray foam than the prescriptive requirements above, then you must follow the performance method or the energy rating index. Both methods require energy modeling and allow energy trade-offs, where you can reduce the amount of spray foam insulation used on the underside of the roof deck, if the design makes up for the reduced insulation somewhere else in the energy performance of the building.
However, IECC Table R402.1.6 points out that when trade-offs are used, the minimum R-value of air-impermeable insulation on the underside of an unvented attic roofline is R-20. [See table above.]
This means that when you are using energy trade-offs via the performance method or the energy rating index the absolute minimum amount of spray foam insulation that you can use in an unvented attic is R-20.
So, according to the above amendment, adopted in January 2020, R-20 spray foam insulation can be code compliant in an unvented attic in GA, if the energy modeling shows that the building design outperforms the code’s reference building.
Additionally, code section IECC R402.1.2.1 [see sidebar], adopted in the Georgia code January 2022, provides a prescriptive path for approving R-20 spray foam as code compliant in an unvented attic, under the following conditions:
- Blower door test result must be less than 3 ACH50
- Mechanical ventilation is required and must be positive pressure, balanced or hybrid
- Exposed portion of the roof rafters shall be covered by minimum R-3 unless directly covered by a finished ceiling (rafters are not required to be covered if continuous insulation is installed above the roof deck)
- Indoor mechanical equipment shall be inside the building thermal envelope
These Georgia amendments show consistent development and approvals related to the unvented attic application when using air-impermeable insulation, such as spray foam. Furthermore, other states, like Alabama have started adopting similar language as well. If this trend continues, we could see more states adopt amendments directly related to approved R-values of air-impermeable insulation in unvented attic applications.
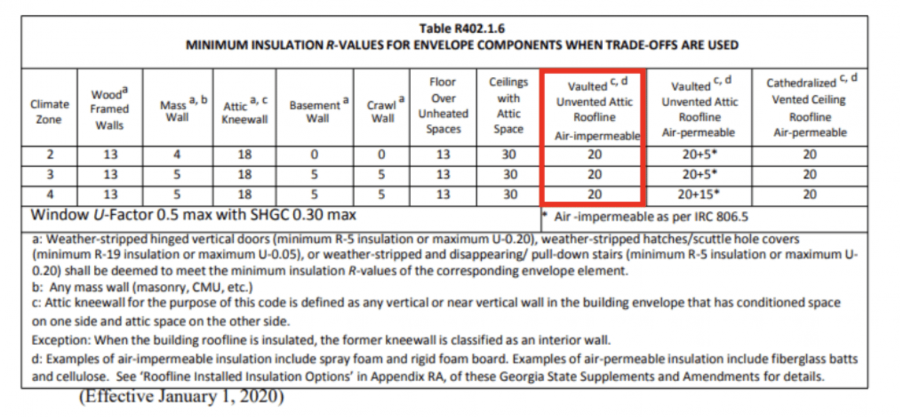
Keep an eye out for these changes in your local jurisdiction, it can have a significant impact on your SPF business.
Direct any questions you have about statements made in this article to Robert Naini:
817-983-3544 | robert@sprayfoamadvisor.com
For use by SprayFoamMagazine.com & Spray Foam Magazine
Disqus website name not provided.