Do the 2021 IECC Building Codes Benefit Spray Foam?
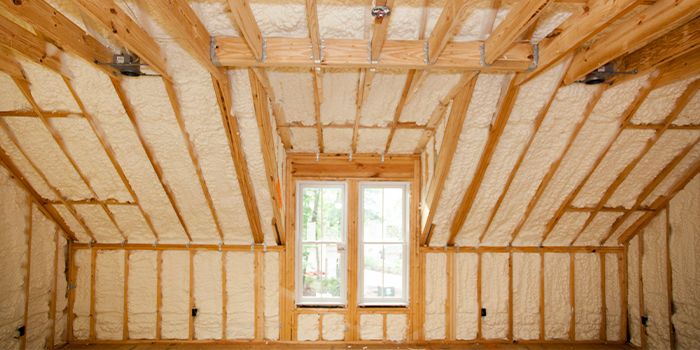
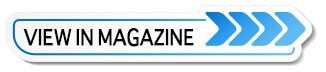
Spray Foam Magazine – The 2021 International Energy Conservation Code (IECC) is arguably the largest change in building codes to date. I’m dating myself, but when I started my career in construction, the energy codes required R11 in walls and R19 in attics. With the updated 2021 IECC, minimum energy requirements have increased to R49 for ceiling insulation in climate zones 2 and 3, and R60 for ceiling insulation in climate zones 4 and higher. Climate zones 1-3 maintained the same wall insulation requirements that have been in effect since the adoption of the 2012 IECC, but climate zones 4 and higher now require R-30 insulation in walls! See the latest IECC Climate Zone Map below for guidance.
I will do my best to make something as clear as mud simple. What does a climate zone mean?
The IECC divides the United States into sections based on average moisture and temperature. These zones change over time, and in part, drive changes to the building code. The majority of new housing starts are in climate zones 1-5 per US Census Data. See the Top 25 Builder Markets Map on the next page for guidance.
That’s a lot of information around Climate Zones. So, how did we get here? What has really changed? If you look at the R-Value tables that were historically the first table in section R402 of the IECC, they have moved to the second table (R402.1.3) and are now considered alternative compliance.
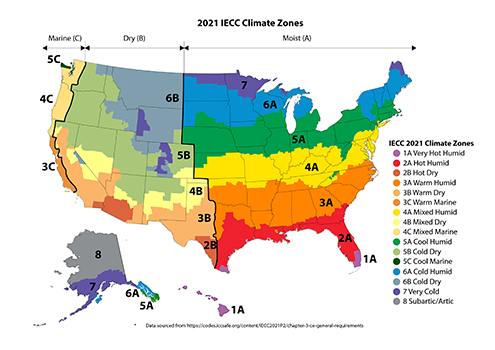
Compliance now starts with table R402.1.2 “Maximum Assembly U-Factors and Fenestration Requirements.” Additionally, section R402.2.1 allows a roll back to 2018 ceiling R-Values, if you have raised heal trusses, allowing the same R-Value at eaves over top-plates. The narrative is starting to write itself now. The new code isn’t that much different from prior codes, but it does give penalties for using the R-Value tables, or not using raised heal trusses.
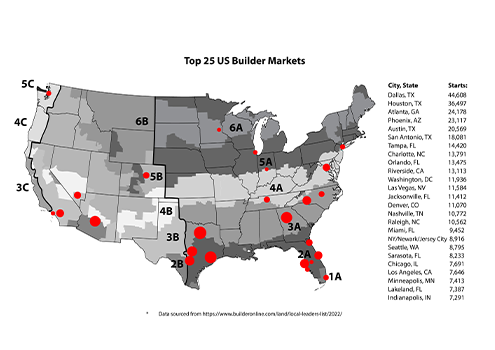
Now let’s revisit the U-Factor table (R402.1.4). The U-Factor, which is simply put the reciprocal value of the R-Value, requires calculation of the entire composite assembly by the ASHRAE handbook of fundamentals including thermal bypass from framing. This includes air films, gypsum, etc. The reciprocal value of the ceiling U-Factor requirement for 0.026 (climate zones 2 and 3) is 38 not 49. The reciprocal value of the ceiling U-Factor requirement for 0.024 (climate zones 4 and up) is 42 not 60. The reciprocal value of the wall U-Factor requirement for 0.045 (climate zones 4 and up) is 22 not 30.
What does this mean? There is a heavy penalty for not calculating your code compliance to the tune of nearly 30%. (Tables: https://codes.iccsafe.org/content/IECC2018P5/chapter-4-re-residential-energy-efficiency)
So, how is this good for spray foam?
Minimizing framing just became extremely important. A typical wall has approximately 25% of the surface area with an R-Value of the wood or 1 per inch with 16 OC framing. Switching to 24 OC advanced framing will reduce the percentage of wall that is uninsulated wood to around 15%. A 2x6 advanced frame wall with R-21 cavity insulation will come close to meeting the R-30 requirement. Add 4 to 5 continuous insulated sheathing on the outside and the wall will exceed the requirement. Use the correct framing fraction for 24 OC trusses and low density or open cell Spray Polyurethane Foam (ocSPF) can meet the R-49 requirement of 0.026 with R-13 cavity and R-24 continuous or R-37. Simply put, the old building code was based on the R-Value of the cavity. The new building code is based on the total composite assembly including thermal bypass. This pushes the favored assembly toward unvented attics where spray foam outperforms traditional types of insulation.
Let’s review compliance methods. There are 3 methods of compliance:
- Prescriptive
- Performance
- Energy Rating Index (ERI)
In this article we have only focused on prescriptive so far. There is a 3rd method of prescriptive from section R402.1.5 that allows tradeoff between walls, floors, ceilings and windows. If you move to 2x6 advanced framed walls, there is typically some room to reduce the R-Value requirements of ceilings. Prescriptive compliance starts with U-Factor tables, the R-Value alternatives, and finally UA alternative. UA is commonly completed for free using DOE RESCheck software. RESCheck can be accessed at https://www.energycodes.gov/.
The performance method has been in the code for a little while, but only allows HVAC and Domestic Water Heating to be the same in the baseline as the proposed. For this reason, it is essentially only comparing the code baseline thermal envelope to the as proposed thermal envelope. It is essentially a more complicated way to do the UA calculation, but will yield similar results. This method is uncommon.ERI compliance gets interesting. The first step in ERI compliance is meeting the ERI requirement by climate zone. This is in the low 50s but varies slightly by climate. An ERI of 50 would use approximately 50% of the energy of a home built to the 2006 IECC. An ERI of 0 would use 0 energy and 100 would be the 2006 IECC baselines. More on the clear as mud theme. Most homes that have Spray Foam unvented attics with current high performance HVAC equipment will meet the ERI index. If you calculate the ERI without renewables, you can relax the thermal resistance requirements by 15%.
Most homes that are designed to qualify for the new 45L tax credits will qualify for ERI and allow for this credit. ERI allows you to take advantage of HVAC, Lighting, Appliances and Domestic Hot Water (DHW) efficiencies and trade off against the envelope. Conditioned space ductwork gives you around 7 points on the ERI scale in addition to HVAC and DHW. In my view the 45L tax credit and the ERI index both promote the rapid adoption of unvented attics. In my opinion, Spray Foam is the simplest and easiest strategy to accomplish an unvented attic.
Contact SES Polyurethane Systems: If you have any questions about any of SES’s products or services: 713-239-0252 // www.sesfoam.com
*This article is not intended to be a comprehensive guide for compliance of the 2021 IECC.
*Spray Foam Magazine does not take editorial positions on particular issues; individual contributions to the magazine express the opinions of discrete authors unless explicitly labeled or otherwise stated. The inclusion of a particular piece in the magazine does not mean that individual staff members or editors concur with the editorial positions represented therein.
For use by SprayFoamMagazine.com & Spray Foam Magazine
Disqus website name not provided.