The Completed
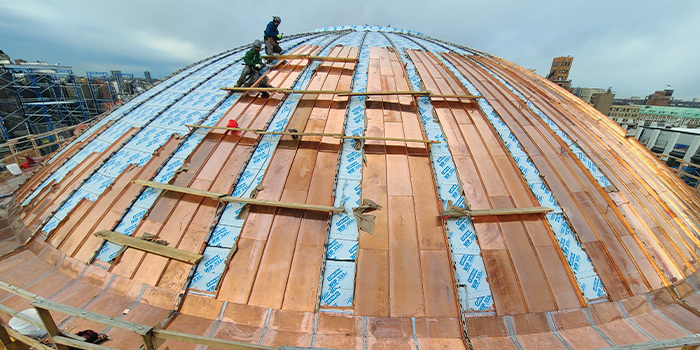
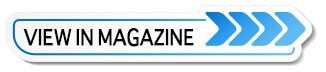
Spray Foam Insulation – Spray foam is implemented into a variety of interesting buildings and structures, but there is something very humbling and special when working on an internationally recognized historic building. The Spray Foam Magazine team (SFMT) were intrigued to investigate the architectural and construction updates recently applied to a magnificent structure in New York.
In 1850, the construction of The Cathedral of St. John the Divine, commenced in Manhattan’s Morningside Heights. From the beginning, there were debates on the cathedral’s style, with numerous architectural designs submitted to a plan-selection committee. Eventually, there was a competition to choose the winning design, with each of these designs being displayed to the public. The winning architects, Heins & LaFarge, modified their designs over the years due to several setbacks. Starting with Byzantinesque interior features and transitioning to English Perpendicular Gothic, the architects updated their plans to keep up with the building fashions of the time.
Following the death of Heins, architect Ralph Adams came in and redesigned many aspects of The Cathedral to French Gothic style, including the great nave. The construction had many setbacks and interruptions, for example two World Wars and even a fire in 2001 that ravaged the unfinished north transept.
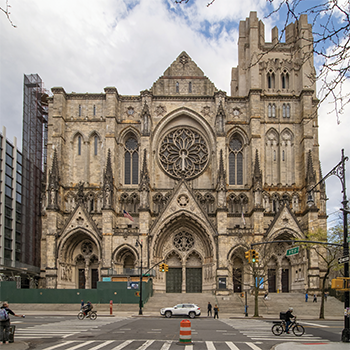
With so many disruptions, the cathedral is often referred to as, ‘St. John the unfinished,’ that is, until now. The structure, the length of two football fields, is well-loved by New Yorkers and admired by tourists from around the globe. It was therefore imperative that skilled and experienced architects and tradesmen worked on this superlative building.
Founded in 1849, Nicholson & Galloway specialize in Exterior Restoration in the Tri-State area, including masonry, roofing, and sheet metal. They have a wealth of experience in dealing with historical buildings and have worked on various projects on The Cathedral of St. John over the last 50 years. They were awarded the once in a generation project of putting a final roofing system on the great dome which would help protect the historical granite underneath.
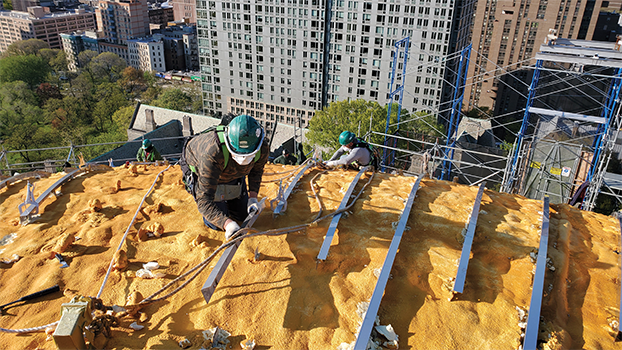
Following the spray foam insulation, new curved stainless- steel rafters were fastened to the struts, sheathing fastened to the rafters, and finally the copper cladding installed.
In 1909, building engineer and architect Rafael Guastavino along with his son, designed the 93-ft diameter great dome, one of the biggest in the world to be built from clay tile. They saw this as a temporary measure over the crossing, with the cathedral having future plans to construct a large tower over the crossing. Because this dome design was supposed to be temporary, it was not fitted with a durable covering, but in its place, asphalt was placed on top.
Noted by building experts for being the thinnest brick shell in the world, it is incredible the dome remained intact for just over a century. This could have been due in part to Guastavino’s applying a Mediterranean technique dating back to 1382, where thin clay tiles and plaster are applied resulting in a structure that is both lightweight and robust.
The thin interlocking terracotta tiles and fast-drying mortar did not have external supports at the time. There were also more layers near the base and scarcer toward the center of the dome. The base was then fastened with a steel tension ring.
The dome endured multiple repairs and roofing campaigns but over time, water infiltration and thermal movement caused cracking and deterioration of the clay tile. Basic repairs would not be enough, it was time for a rehabilitation. Two architectural firms, Ennead Architects LLP and James R. Gainfort AIA Consulting Architects PC were involved in helping the team at Nicholson & Galloway plan and assess. Recognizing they would have to get down to the base of the dome and start again, they started by first stripping out the old material and replacing it.
A plan was developed to install a final roofing system over the clay tile to deal with thermal expansion, movement, and leaks once and for all. This plan included: the removal of the compromised existing roof membrane and insulation, repairs to the cracked tiles, installation of trowel applied vapor barrier, the application of spray polyurethane foam, new stainless-steel framing, struts to accommodate spray foam, two inches continuous air space, new plywood sheathing, sheet waterproofing membrane, and new batten and standing seam copper cladding.
Wearing Tyvek suits, gloves, face masks, respirators and harnesses, the crew first installed full pipe scaffolding up around the crossing arches on the north and south elevations, with a continuous deck installed around the midpoint of the dome. Slices of the dome were accessed with ladders, pick platforms, and lifelines. Existing roofing was abated in phases and covered with custom tied down tarps.
On the lowest layer of the dome, thousands of tiles were examined to establish which ones were loose. Once identified, these tiles were re-mortared. The tiles that were either cracked, and or water-damaged, were replaced with new ones. The new custom-made tiles were made by Sandkuhl Clay Works in Spencerville, Ohio. A 4th generation family-owned and operated manufacturing business and originally a producer of clay drain tile for agricultural use, Sandkuhl now manufactures many other ceramic, structural clay, refractory and related specialty products.
The damaged tiles, in each slice, were then repaired and coated with AVB (air vapor barrier), with the tarps being removed after the AVB was installed. Then, six inches of framing struts were fastened and adhered to the tile prior to the spray foam being installed. The SPF was applied by two crew members from Nicholson & Galloway: one on gun, one on hose, and the third 200’ below on the compressor was from Henry. Henry Permax closed-cell foam was applied at 2-1/2” thick with 18 sets used. This foam was used as part of the Henry Waterproofing System, which also included Henry 787 Elastomulsion, designed for use as a waterproofing or damp-proofing membrane ideal for concrete or masonry structures. New curved stainless-steel rafters were fastened to the struts, sheathing fastened to the rafters, and finally the copper cladding installed.
The new outer enclosure, designed by Ennead Architects, was comprised of lean, arched pie-shaped roof pans made of sheet copper to compliment the other sections of the cathedral’s roof. Supple seams in the new enclosure enabled it to acclimatize to any dome movement.
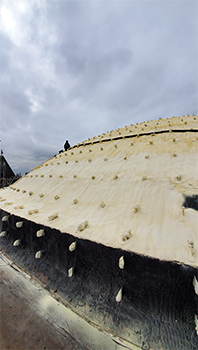
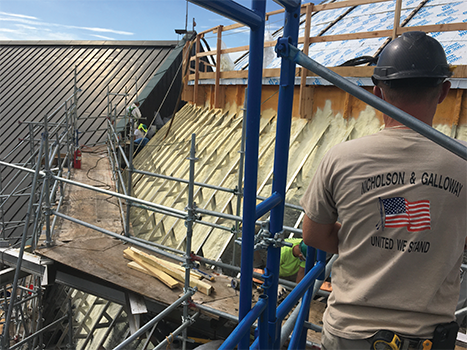
Henry Permax closed-cell foam was applied as part of the Henry Waterproofing System, which also included Henry 787 Elastomulsion, designed for use as a waterproofing or damp-proofing membrane ideal for concrete or masonry structures.
The purpose of specifying closed-cell and a waterproofing system was to help combat several issues. Over the years, the dome was exposed to high temperatures of the summer and extreme cold of the New York winters, expanding in the warm weather, and contracting in cooler weather. Over time, these fluctuations in temperatures resulted in cracking, and therefore leaks, with the damp and wet seeping into the structure. In the 70s, foam glass insulation was added, but when a waterproofing membrane installed in the 1990s ultimately tore, water then soaked into the insulation.
The great dome’s new copper covering is already fitting in with the cathedral’s aesthetics, developing a discoloration much like the patina of the nearby angel Gabriel. The three-year $17 million rehabilitation project has restored this historic dome. This spectacular copper roof, with the new roofing system, including the closed-cell foam will be protected from the elements for the next fifty to a hundred years. With good maintenance, it may even last longer.
Historic buildings are crucial in constructing a sense of place, space, and personality of a city or town. They are a capsule of time, and fashion of architecture that would otherwise be disregarded.
Sad to report that many of these noteworthy old structures are in desperate need of repair. The extreme weather, neglect, and lack of money has resulted in many old buildings diminishing into disrepair. Having quality designs and materials applied is crucial for time and people to never forget this architectural and historic importance these structures have in our lives. Not to mention, they are contributing to increasing tourism and uplifting communities. Taking them for granted would be a mistake.
Luckily for all of us, there are people who fight for these buildings to be restored. With the help of talented architects, builders, and their crew, they can make a difference in preserving history by combining traditional and modern building techniques, and once again superior materials like spray foam insulation can take part in preserving a piece of history.
For use by SprayFoamMagazine.com & Spray Foam Magazine
Disqus website name not provided.