Sealing With(Out) a Splash
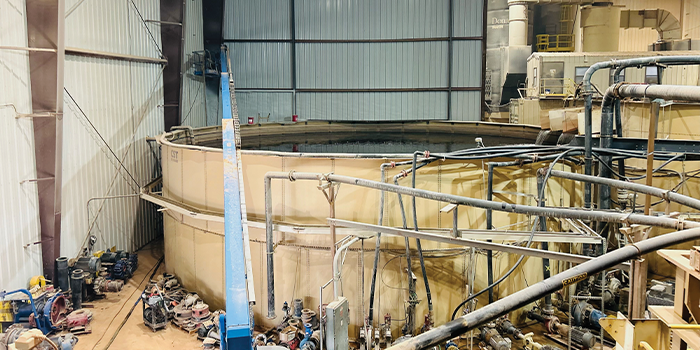
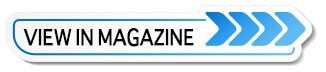
SPRAY FOAM MAGAZINE – Precision Spray Foam, LLC is a family-owned business which launched in 2019. Specializing in insulation, ventilation, and encapsulation they have a reputation for providing practical, effective solutions for spray foam, fiberglass batt insulation, blow-in blanket systems (BIBS), and protective coatings.
Precision Spray Foam is located in Gillette, Wyoming. This area is often referred to as the “Energy Capital of the Nation,” due to the area producing vast quantities of oil, coalbed methane gas, and roughly 40% of the nation’s coal. Extracting fossil fuels from the underground shale rock formations requires cracking and splitting them open by blasting them with a mixture of highly pressurized water and high-quality sands, known as frac sand, which in turn helps release massive quantities of natural gas and oil.
Precision provides protective coating services for all kinds of needs in the state of Wyoming. Gardner makes a point of not just selling insulation, but providing each specific project with the product it needs, and with their building science knowledge, they strive for a long-term efficient envelope. Gardener’s goal is to provide past, present, and future clients with pride and customer satisfaction, in addition to constantly looking for ways to improve efficiency within a structure.
Recently, the crew at Precision completed a job that required both their spraying skills along with a splash of imagination. Spray Foam Magazine caught up with the owner, Joseph Gardner to find out more.
Gardner and his crew have foamed several metal buildings owned by a frac sand manufacturing business who have plants in both Wyoming and Utah. Recently the Precision crew worked on one of their buildings in Wright, Wyoming. In this steel building, the production of different types of sand for fracking is manufactured. The client required SPF to be installed as the frac sand can be a very abrasive product and an air-sealed building helps with moisture control and prevents the sand from becoming wet and damaging the sand processing equipment like pumps, gears, and bearings.
Gardner’s crew has been working for Precision for at least two years. They all have their own area they control and oversee with Nick Glaser as the lead SPF sprayer, Hunter Tibbetts as the lead for batts, and Taven Bryan as the lead for blow-in. The crew all worked on this SPF project, taking their H40 Graco Reactor, fusion guns, and spray foam trailers to the sand plant to start the job.
As they were prepping, they soon realized that there was an issue. Spraying the 50-ft.-tall walls of the steel building seemed straightforward enough for the crew, however, there was a large water tank inside the building that is used for filtering the sand. It needed to be kept inside to help protect it from the -50 temperatures the area gets in the winter.
The height and positioning of the tank made it impossible for the crew to reach the curtain areas, even with the manlift.
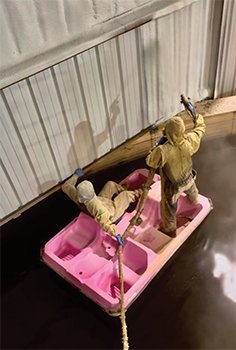
Faced with this obstacle, Gardner recalls, “In our area with the extreme work environments we can encounter, we have learned to adapt and think of different ways to get any job done. By thinking outside the box, it’s not a matter of can we, but how can we solve an issue.” Gardner along with his lead sprayer, Nick Glaser jokingly asked the client if they could drop a boat into the tank and they actually agreed to this notion. How would they find a boat small enough to carry two crew members on such short notice? Gardner suddenly remembered that his daughter had a paddleboat that just may be the solution they needed.
The crew was relieved when they placed the paddleboat into the tank and it was the perfect size to maneuver around the space. With the added feature of working on top of the water, the entire operation was very safety- oriented. The crew put on their usual PPE including their fresh air supply, in addition to following the Mine Safety and Health Administration (MSHA) requirements such as hard hats when able, steel toe boots, and safety glasses when not in masks. They also used harnesses and wore life jackets under their spray suits while on the boat.

After most of the walls were sprayed, it was now time for the crew to try out the pink paddleboat and finish off the curtain area. Two of the crew, Gardner and Glaser, positioned themselves in the boat and Taven was in the manlift hanging the hose above the water to make sure that none of their equipment touched it. Hunter was placed on a catwalk overseeing the job for issues and if anyone needed anything. As Glaser sprayed two inches of JM Corbond IV closed-cell foam, Gardner slowly paddled to keep him in position. The crew managed to spray all the walls of the building applying a total of six sets of foam. The client was happy with the job and planned to place metal over the SPF to complete the project.
Joseph Gardner said he’s proud of his crew and everything they have achieved, “I have a phenomenal crew of young guys who do a great job.
Not only do they complete their jobs to a high standard, but they use their initiative and imagination when we are faced with an exceptional situation. I can always count on them to work as a team, even if that means working from a pink paddleboat.”
Disqus website name not provided.