Removing the Thermal Bridge
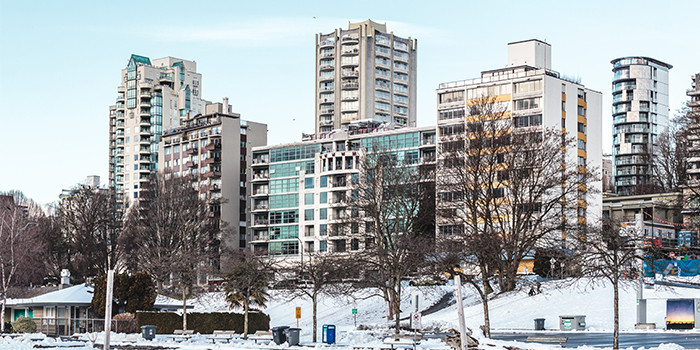
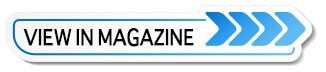
Spray Foam Magazine – Fall Issue 2021 – Winter—while many get excited for the changing of the seasons, contractors often shudder at the thought of spending many hours working outside in cold temperatures. Employees also wrestle with productivity during these winter months. Basically, winter construction takes longer and causes all manner of issues when climatic conditions come into play. Materials will be exposed to rain, snow and wind with some materials having their adhesion diminished in colder applications. These changes in the weather alter air movement, temperature, and humidity all of which can be a problem for spray foam contractors. Temperatures must be constantly monitored, and substrates should have less than 19% moisture content. If there is too much rain, wind, snow, or ice on the substrate this is a problem. In short, insulation products are habitually sensitive to temperature and water therefore the complete building needs to be watertight.
Are there any solutions that may help reduce time spent outside? Huntsman Building Solutions may just have the answer contractors having been looking for and it comes in the form of a wall assembly. The D-Max Wall application even sounds awesome. So how does this application work, and why should contractors and employees take off their snow boots, sit up and take notice?
The D-Max Wall application method makes large building construction in the winter a breeze, no pun intended. Seriously, consider this, it can be as cold as -10°C outside and contractors can apply the closed-cell SPF as soon as the first floor of a building has had the exterior sheathing installed. As the product is resistant to water, there is no need for the windows to be installed or the roof to be watertight. This saves on heating costs during construction as the insulated floor can be heated right away and there is no need to have heating without insulation, which often creates condensation or frost issues. Not to mention that there’s only one product to install with no questioning which products should be installed first. And before its questioned, yes, the assembly is certified by an engineer and tested to meet the building code requirements for high-rise complexes.
Passing Codes and Certifications
The D-Max wall assembly has successfully completed the CAN/ULC S101 test in accordance with the Canadian building codes and is UL listed. The product is also GREENGUARD Gold certified, which means that it is low VOC emission to ensure better indoor air quality. This certification is independently tested and verified to meet rigorous standards for chemical emissions. It also meets all fire blocking requirements for concealed wall spaces and is NFPA 285 Compliant. Other certifications include - ASTM E96 Water Vapor Permeance, ASTM E2178 Air Permeance, Firestop certification by Hilti, 3M and STI, LEED V4, UES evaluated and CCMC 14078-L.
Three In One
The D-Max Wall assembly method is achieved when Heatlok Soya HFO, Heatlok HFO Pro, or High Lift closed-cell insulation is applied to a wall which is composed of regular steel studs. This is where the interesting part happens, instead of installing the exterior sheeting directly on the steel studs, a Z girt is installed horizontally on the studs and then the sheathing is installed on top of the Z girts. And voila, this enables for a space between the studs and the sheeting which facilitates the foam to insulate between the two thus removing the thermal bridge. Picture it like the insulation is on the exterior of the building, but it’s applied from the interior with the D-Max Wall assembly providing an impressive building envelope which has both quality and durability as its main attributes. This truly is a win, win situation, with contractors spending less time outside in the cold and their employees saving time onsite, which makes economic sense.
The spray foam used in the interior application replaces four materials including the exterior insulation (rockwool or others), the full-surface membrane, and the fiberglass insulation in the cavity and the poly. Therefore, one of the main advantages of this assembly is that Heatlok Soya HFO spray foam acts as the insulation, air barrier and vapor barrier in a single application. As previously mentioned, the D-Max is not affected by water, so it can rain or snow on the assembly without there being a need to replace it. All this in addition to its mold resistance.
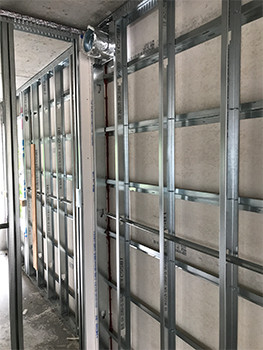
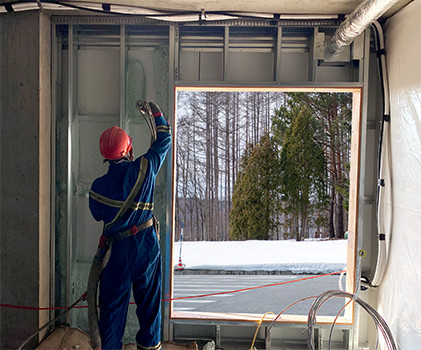
Heatlok Soya HFO closed-cell insulation is applied to the interior wall according to the specified thickness.
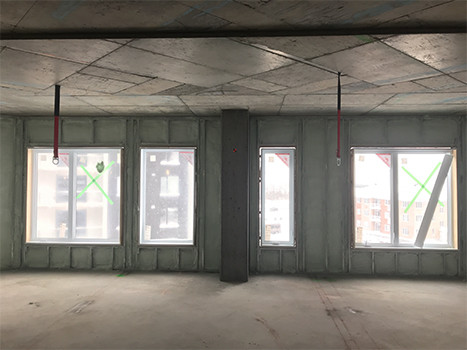
The single application D-Max allows for a high-performance assembly resulting in an effective thermal resistance and airtightness system with very thin walls. Due to the three main properties of the building envelope being provided by a single product these advantages result in the planning, coordination and execution of the work becoming easier and quicker. The fact that this reduces a considerable amount of time and construction costs and accelerates building delivery is a much-welcomed bonus for all.
Due to the spray foam application being installed completely from the interior, it cuts out the thermal bridge of the studs by filling the gap between the exterior sheathing panel (exterior gypsum).
The Interior furring is now optional and compared to conventional construction electrical systems can be installed before or after insulation with no holes in the vapor barrier. Due to the thinner walls providing additional square footage, there is also an extra sales point for the owner of the building, thus having the potential to make the building sale more profitable.
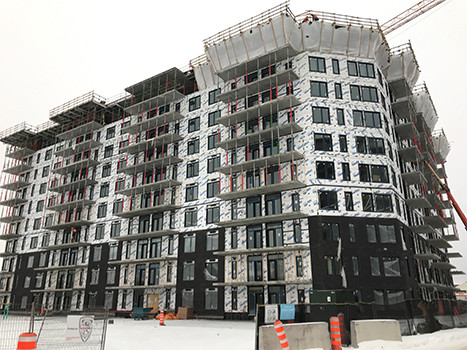
Example of productivity of the D-Max system. The cladding is installed from the ground floor to the third floor, the interior insulation is installed on levels 4 and 5 and the structure is poured on level 10.
Saving Time and Money
No scaffolding or vessel is necessary, and less machinery and materials are needed. This results in saving money on equipment rental costs and extra materials. The logistics of a job are also simplified with the project manager needing less workers to execute each step and the building insulation can be performed as the walls go up. Without question, the D-Max is also an important heating cost saver for clients.
General contractors are already raving about the D-Max Wall assembly with Simon Corriveau, Vice-President of Dinamo Construction commenting, “On one of our projects with this wall assembly, the time on site has been reduced by 4 weeks or more in addition to the savings realized on heating costs during wintertime. The owner has been able to occupy the building much quicker.”
The owner of MG Construction, Jean-Philippe Hamel said of the D-Max wall assembly, “It reduces a number of necessary materials, the simplicity of the details, the quickness of execution and the quality of the installation and it’s very easy to adapt to different projects.”
Spray foam installers are also impressed with Jean-Sébastien Dion from Isolation Arctique stating, “This assembly is very advantageous for us because the cost for the spray foam is much lower than for an exterior application. The reason is that we don’t need any scaffolding to include in our price and there are no weather conditions to predict which allow us to increase the onsite productivity and profitability. It’s also much safer for our employees and the product application is completed in the best conditions.”
This energy efficient one step wall assembly will not only bring spray foam installers in from the cold but make their lives easier too.
Disqus website name not provided.