Historic Church Updated With Spray Foam Retains Aesthetic Charm
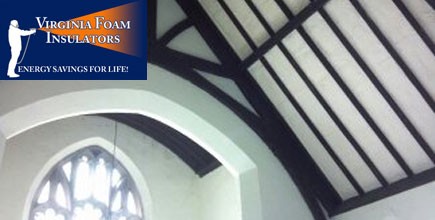
LYNCHBURG, VA – February 18, 2013 – Lynchburg is located in the foothills of the Blue Ridge Mountains, along the banks of the James River. The city was named for its founder, John Lynch, who started a ferry service across the river. The "City of Seven Hills," as it's known, developed along the hills surrounding Lynch's Ferry. The new easy means of transportation allowed Lynchburg to become the new center of commerce for tobacco trading. Rich in history, Lynchburg prides itself on preserving its historic buildings and is currently undergoing a revitalization of its downtown area.
The First Unitarian Church of Lynchburg, located in the middle of Monument Terrace, was built in 1924 as a memorial to citizens who fought and died in American wars. The church wanted to retain its historic aesthetic, but lacked insulation to keep its parishioners comfortable and could not stay open year-round. After several months of contemplation, the church contacted Virginia Foam Insulation (VFI) for help.
"They could only hold services for a few months out of the year," said James Kuhn, owner of VFI. "It cost too much to heat it in the winter and it was too hot in the summer."
The church had a furnace, but it was costly to run because the building continued to lose heat. In order to cool the building, they planned to install an air conditioning system, but VFI noted that without proper insulation, the building would not be able to retain heat or cool air.
"You can heat it and cool it, but you're still going to lose it all without insulation," Kuhn said.
So it was decided that while the new air conditioning system was being installed, VFI would be responsible for installing spray foam insulation.
To get a better idea of how to go about working on a historic building, VFI consulted with a local architect experienced in the area. A decision would be made that it would be best for VFI to cover the original timber framing with plywood, making it look similar to the original ceiling, without damaging the existing wood. This would require protecting old beams and chandeliers, plaster walls, stained glass windows, and slate floors – all original to the church – from overspray. So, although the church was not very large, the project would prove very labor-intensive due to preparing everything that had to be protected from overspray.
VFI put down heavy plastic sheeting over the walls, securing it to the floor with tape, and fastened it to the top of the walls. Large curtains of plastic hung down, protecting the area from foam. Crewmembers pinned up and covered old chandeliers with plastic. Normally, such fixtures would be removed, but due to the church's old wiring system, VFI decided against it. Nearly 30 beams on either side of the ceiling had to be individually wrapped in plastic to protect them from overspray.
When preparation was complete, VFI installed a whole new ceiling system over the existing one. To do this, they attached ½-inch wood furring strips to the ceiling beams to make backing surfaces to support the plywood. After the furring strips were installed, crewmembers nailed pieces of luan – thin, lightweight plywood – to the strips. Rather than applying spray foam directly onto the original timber framing, the luan would be used as the substrate to which the foam would be sprayed. Before they began application, crewmembers affixed one-by-three pieces of wood to the sides of the timber framing. These pieces of wood acted as a barrier that the foam would bond to instead of adhering to the timber frames. When VFI applied 2.5 inches of Premium Spray Product's Foamsulate 210 closed-cell spray foam to the luan, the foam had about a half-inch leeway for expansion against the one-by-threes, leaving the frames unharmed. The foam would subsequently be trimmed back.
After spray foam was applied, VFI chose to stain rough-sawn plywood to install for the ceiling. This would create an illusion of older wood. They asked the church to select a stain color to match the original timber framing. After cutting and staining the rough-sawn plywood to fit the ceiling, crewmembers installed it over the foam then trimmed the foam back.
"Although you didn't see the lines in the board like you used to, it gave the appearance of it being really old wood," said Kuhn. "But now, everything was insulated and nothing was touching any of the original framing, so if they wanted to get it back to the original, they could tear it back out and it wouldn't affect the original framing."
The church was located in the middle of 150 steps between the top and bottom of Monument Terrace and the parking lot was very small, so VFI could only get their spray foam rig within about 75 ft. of the church.
"Everything is compact," said Kuhn. "The whole city is terraced."
Due to the limited space, the project had to be done between 6 p.m. and 2 a.m. most evenings, with the aid of work lights.
"We could only get into the ramp that goes into the parking lot and we had to make sure everyone was out and it was all blocked off," said Kuhn. "There was just enough room to open your door and squeeze out of the truck."
Crewmembers used a Graco Reactor E-30 to apply the spray foam and wore fresh air masks while spraying. Scaffolding was employed to access the church's 25-ft. vaulted ceiling and fans were used to circulate the air. The total spray area was nearly 1,800 square feet.
It took two to four crewmembers, including Kuhn, close to a week to complete the project in late summer of 2012. Kuhn believes the church is now open year-round and better able to accommodate its loyal, long-time members by providing comfortable temperatures, while maintaining its original, historic appearance.
About Virginia Foam Insulation: Virginia Foam Insulators is a veteran-owned small business started by James Kuhn in 2007 after he returned from Operation Iraqi Freedom. Virginia Foam Insulators is Central Virginia's regional expert in the installation of closed-cell and open-cell polyurethane spray foam insulation. Headquartered outside Lynchburg, Virginia in nearby Monroe, Virginia Foam has performed jobs as far away as Georgia and in the surrounding states of Maryland, West Virginia, and North Carolina. Employees have undergone training field and classroom training and have met rigorous standards for performance and work ethic. Virginia Foam utilizes blower door testing as an in-house diagnostic and quality assurance tool. For more information about Virginia Home Insulation, please use the contact details and links provided below.
Disqus website name not provided.