Getting Through Winter with your Rig
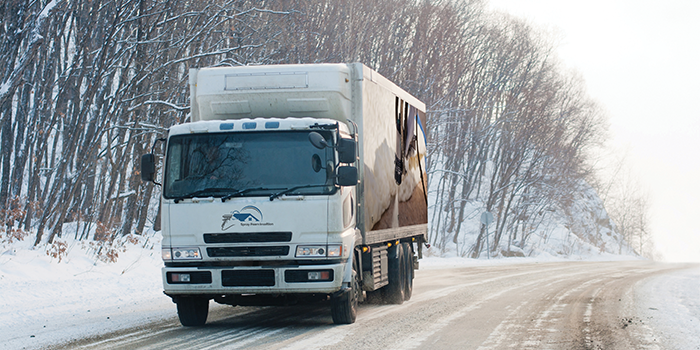
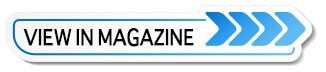
Spray Foam Magazine – Winter 2022 – Cold weather is right around the corner and that can spell problems for an unprepared spray foam contractor. When the winter weather strikes, it can cause problems for spray foamers like pump cavitation, poor adhesion, shrinking foam, and lower yields. To combat these issues, here are a few tips to get you ready.
1. Ensure Proper Formulas: First, make sure you’re getting the right formula for the temperature of the substrate that you want to spray against. That's number one.
2. Monitor Temperature: Get yourself a laser thermometer if you don’t already have one. You can use this to check the temperature of the substrate. You can also use it to check the temperature of the drums in your rig. We want to keep these drums between 70-80 degrees, both inside your rig and in your material storage area. That’s going to help you be more successful, less downtime, less problems.

3. Heat your Rig: Inside your rig, you want to have heat. Let’s say this is our spray foam rig. First, we have to heat the area that’s in that space, 70 to 80 degrees. So that’s going to help warm the drums from the sides and from the top, but if your drum is sitting right on the floor, even if there’s foam insulation underneath, foam doesn’t create any heat. It only slows down the transfer of heat. So right now we're still losing heat from the bottom of the drum.
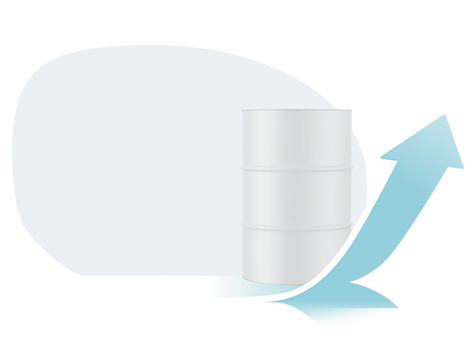
4. Lift Your Drums off the Floor: To prevent heat from leaking out of the bottom of your drums, let’s get the drum off the floor a little bit. Take some two by fours and lay them down flat underneath those drums, that’ll let that warm air go underneath and heat those drums from the bottom. That can make at least a 10 degree difference in the temperature of those drums. We also have electric drum blankets to wrap around the drums to keep them warm. That’s really going to help you out this cold weather season.
5. Heat Your Substrate: To avoid the lower yields, shrinking foam and poor adhesion, you’ll want to keep the substrate as warm as possible. Regular torpedo heaters can be used but present several problems. They can only be used before spraying begins. These must be turned off prior to spraying to prevent burning the fumes and creating toxic gasses. You will also need to monitor the moisture level of the substrate because torpedo heaters create a high level of moisture. Indirect heaters work a little differently. Indirect heaters sit outside the building and use ducts to blow dry clean air into the building. These do not add any moisture to the building and can be used during the entire spray process. Indirect heaters even count as ventilation during the spray process. These are a great way to improve yields and even production since employees will be more comfortable.
For use by SprayFoam.com & Spray Foam Magazine
Disqus website name not provided.