The Snail House
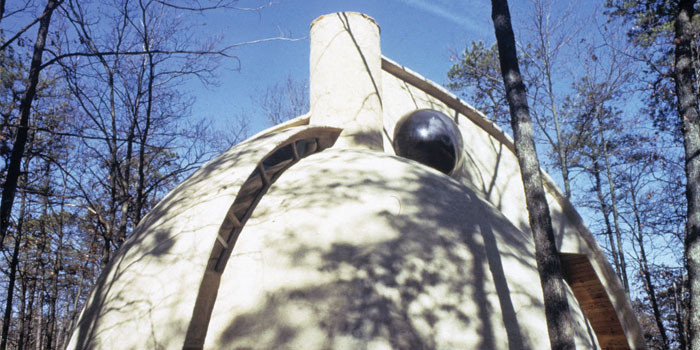
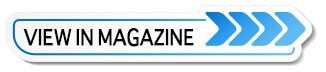
SPRAY FOAM MAGAZINE – Show Issue 2021 – The design of the geodesic dome home was patented in 1954 by Buckminster Fuller, the polymath American architect, philosopher, inventor, and writer. His vision of dome homes was embraced a decade later when young enthusiastic builders and architects made them one of the most iconic architectural builds of that era.
In the 1970s, there was a noticeable population increase in rural and suburban areas of the U.S. According to the Population Reference Bureau, ‘This nonmetropolitan turnaround resulted in a population gain that actually exceeded the gain in metropolitan areas for the first time in at least 150 years.’ The dome home design was an early response to a changing mindset at the time.
This dome home, named ‘Snail House’ was designed and built by Steve Badanes and John Ringel of Jersey Devil Design/Build in 1972 in Forked River, NJ, at the edge of the Pine Barrens. The house was built for a Princeton University steamfitter and his family. The dome was framed with barn rafters, sheathed in tongue and groove cedar decking, with a nominal of 2x6, on the outside and then covered with closed-cell spray foam. The architects chose spray applied insulation for the outer finish because of its air barrier and vapor retarding properties. The project was meant to eliminate as many steps as possible for the economy, so exposed framing and sheathing acted as the interior finish. All material decisions were based on efficiency and material cost savings.
The central column was built by stacking manhole risers and after the framing was complete, the urethane foam was applied by rigging a rope and pulley around the column. The installer hooked in and skittered around the roof applying the closed-cell foam.
The foam was protected at that time with one of the first installations of a product called Dryvit, a type of synthetic stucco that is applied as a final coat. In this case, it was applied over SPF rather than over another stucco system, such as Exterior Insulation Finishing System (EIFS). The Dryvit layer keeps water from penetrating the other layers of the wall.
Steve explains, “We chose SPF for the insulation R-value and since it was the easiest way to waterproof the unusual structure. Using the Dryvit, also protected the foam from UV exposure. We were off label in our installation over the urethane foam, but the product stuck and did what we needed it to do, protect the foam from sunlight, and give a finish color on the outside.”
John continues by adding, “The foam was dense enough to feel rigid and it presented an uneven but skinned-over finish. We had a nominal two inches of foam installed, probably due to budget and, as I remember, based on the recommendation that the two-inch minimum would ensure the dew point was in the foam, eliminating any condensation issues. In those days, R-12 was considered a pretty good level of insulation in the walls. This was just before the first oil embargo in 1973. At that time single pane windows were the default and upgrading to thermopane units was not a foregone conclusion.”
The budget for this original dome was $20k, which included the completed shell and the spray foam with the interior features which were completed by the owner. In recent years, the dome homes still standing are being purchased with many being remodeled to fit current lifestyles including this impressive ‘Snail House’ which is currently for sale for $295k.
Disqus website name not provided.