The Crane Game
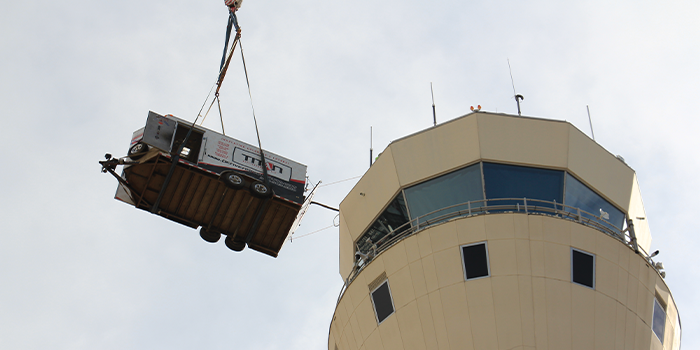
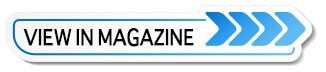
SPRAY FOAM MAGAZINE – Contractors are used to weighing up the pros and cons of bidding on projects. However, a job occasionally comes along where a contractor’s intuition pushes them to bid on it. It’s not because of the size and scope of the job, but it’s the challenge and importance of helping a client in need. Such a venture happened to Titan Applicators, LLC in Denver, Colorado. Titan launched in 2015 as a spray foam insulation company, since then, they have transformed into a foam and coatings company trusted by contractors, homeowners, and building owners alike. The Spray Foam Magazine team sat down with the Titan crew to find out about one particularly tricky job.
From the greater Denver area to Colorado Springs and Fort Collins, Titan’s highly trained team serves commercial, industrial, and residential customers across the Front Range of Colorado. Tony Bock is co-owner of Titan and explained the company’s culture, “We really focus on the simple things like keeping our word, over-communicating, and over-delivering. We combine these values with passion, dedication and skill while continuously developing strategic partnerships with construction professionals and homeowners. This unique job all started when I received a call from a general contractor in desperate need of a quality solution to an immediate problem.”
Centennial Airport is a public use airport southeast of downtown Denver. It opened in 1968 as Arapahoe County Airport and was renamed in 1984 as Centennial Airport. Today, it is one of the 25 busiest airports in the nation, averaging 1,000 takeoffs and landings per day. Bock received a call from a general contractor (GC) who was in a stressful position. His usual roofing contractor had not been able to take on this urgent project that needed completing in 72 hours. Bock is a character who runs towards a challenge, so he was eager to hear more. In a preliminary meeting with the GC, Bock learned that the control tower’s PVC roof was leaking and it was showing its fair share of wear and tear since being rebuilt in 1985. There needed to be a quick and cost-effective solution. The challenge — there had to be no halting of operations of the control tower in any way.
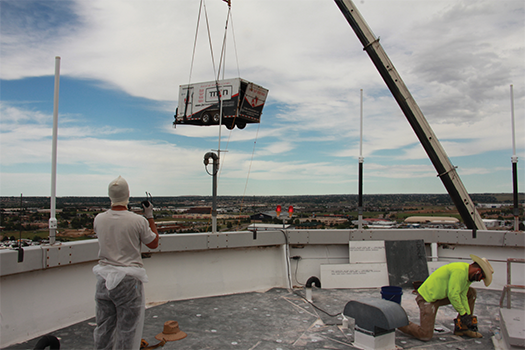
The Titan team preps the roof and gets ready to spray at the top of the tower at the Centennial Airport
Tony Bock went to his business partners, Jake Kluge and Bobby Cozine, and told them about the project. “We have been in business together for a decade and we base all of our decisions off a three-way vote, but this time I was the only one wanting to proceed with this job. They rightfully had concerns; for example, the hoses were not long enough and we didn’t have enough time to figure out the logistics.” Titan prides itself on going above and beyond and doing what many would view as the impossible, but in this instance, they were concerned that this job may be too much of a rush.
Bock convinced Kluge and Cozone to visit and walk the site with the GC so they could all make an educated decision. The Titan crew told the GC that their hose was not long enough to reach the control tower’s roof so they explored using a crane to actually lift their spray foam rig. The crew then ran through a list of what could potentially shut the job down and within twenty-four hours, the GC had the crew at peace with how he would mitigate all of their concerns. The contract was written out making sure that everyone was comfortable and any risks had been addressed before they proceeded.
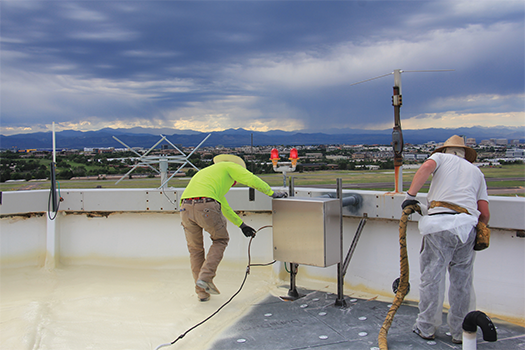
Two inches of NCFI 2.8lb foam was applied over the tower’s PVC roof, followed by a Pro-Tech Acrylic Topcoat
The crane was soon lined up by Duffy Crane & Hauling, Inc. and ready for the three person Titan crew at the Centennial Airport. Titan had no communication with the crane operator until the actual day, but the crane’s rig was big enough to lift whatever the crew needed. The crane had lifted similar trailers before, so the operator had the proper equipment to connect Titan’s 16-ft spray rig to the crane. Therefore, the crew was confident Duffy knew what they were doing. The big question mark for the crane operator and the crew was, ‘could they operate out of the rig while it was being suspended?’
Working out of a suspended rig ended up being the most stressful part of the job. The control tower is 200 ft tall and the rig had to be lifted roughly 220 ft to hoist over the tower’s sidewalls and FAA equipment for the crew to reach into the rig. Although it wasn’t blustery, there was enough wind and rain to make the rig difficult to control.
As the rig swayed back and forth the realization that the crew would be working out of it suddenly hit them, and their hands started to sweat. Once the crane operator had the rig hooked up and was comfortable with the attachment points, he lowered it back down to the ground. The crew put their faith in the crane operator and then fired up their PMC PH-2 proportioners and got everything running and operating. The crane operator then lifted the rig with the equipment up to the top of the control tower.
On the first run, the crane operator lowered the rig just enough for the Titan crew to open the doors and reach in and pull everything out of the rig. Bock takes a deep breath in and says, “That was the only blunder we made that day, to leave all the rig doors closed. As a result, our compressor overheated, and we lost pressure only after a couple of minutes of pulling the trigger. Therefore, the rig had to be lowered to the ground again. Unfortunately, the control tower doesn’t have an elevator, so we had to walk dozens of flights of stairs every time we needed to go and work in the rig. Up and down, we went several times. It was tiring.”
After the initial hiccup of bringing the rig back down to the ground and resetting the equipment, the entire procedure ran smoothly. The GC even got some extra hands to help hold the rig steady while the crew were spraying, as they were not allowed inside the rig once it was lifted off the ground. They were only allowed to reach into the trailer from the roof, not step into it. The crane operator lowered the rig until it was suspended only a couple of feet above the center of the roof, the crew removed all that was needed for the application, then the crane operator would hoist the rig a safe distance away from the building during application and finally, the rig was brought back to the roof in order to put all the equipment back into the trailer before it was lowered to the ground.
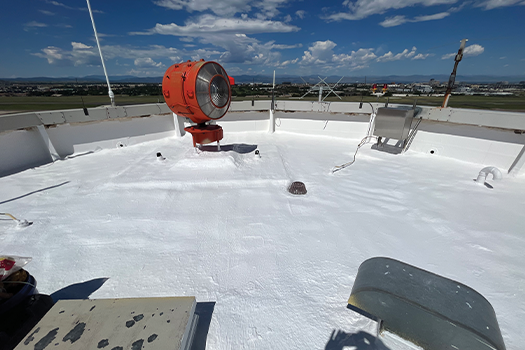
The Titan crew applied two inches of NCFI Polyurethanes 2.8lb foam followed by a Pro-Tech Acrylic Topcoat over the tower’s PVC roof. Titan would not typically place the roofing system on top of the old roof without having time for their own due diligence, like checking for moisture under the roof, substrates etc, however the airport had just received funding to build a new control tower and therefore wanted the old tower to have a quick and reliable solution until the new tower could be built.
Titan went back and forth considering whether to use their coating rig in addition to their spray rig. However, due to the project only being 1,000 sq. ft. they decided to have the roof coating pails on standby inside the rig and once they had completed spraying the foam, they pulled the hose back in, and then pulled out the pails they needed to roll the product out. That way, they did not have the stress of the machines and the rig, literally hanging over their heads.
The only other obstacle the crew faced, was due to the roof being an FAA (Federal Aviation Administration) control tower and being one of the busiest airports in the country, the tower couldn’t shut down its operations. “It was a unique situation for us all, with the traffic control agents looking outside at the view of the runway, then all of a sudden they see this big rig,” recalls Bock.
The logistical complexity of the roof, from the crane’s suspension of Titan’s rig, to working around the traffic controllers and making sure not to knock any radars and antennas out of place, made this a very technical and demanding project. The crew also had to complete the job in one day or the GC would face penalties from the client. Despite these challenges, the Titan crew were able to complete the job by days-end with a very happy and relieved GC.
For use by SprayFoamMagazine.com & Spray Foam Magazine
Disqus website name not provided.