Technically Speaking
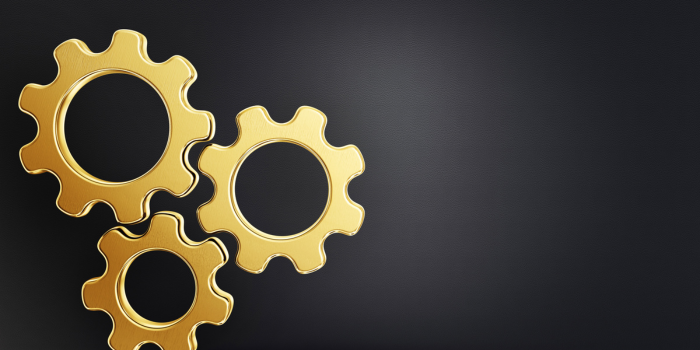
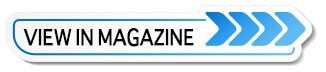
SPRAY FOAM MAGAZINE – Gaco SprayFoam | SES spray foam contractors know that a sale means nothing if the equipment doesn’t work, the installation goes poorly, or someone is hurt on the job. The actual installation of spray foam starts long before the installer pulls the trigger on the gun, and mastering this preparation is as much an art as spraying the foam. As part of our contractor support, we offer technical assistance to our partners to ensure they’re operating in a safe environment while maximizing yields and minimizing downtime.
Safety
Implementing and maintaining safety standards on the job are essential for a spray foam contractor. To guide us with safety in the industry, there are some very important safeguards that apply to every job site, including Respiratory Programs, OSHA standards, and the use of Personal Protective Equipment (PPE). It is the contractor’s responsibility to protect their employees and themselves. Every contractor should have a Respiratory Program in place for ALL employees to complete prior to working on the jobsite.
In addition, OSHA requires a fit test for the style of respirator used. This helps ensure the user is properly trained to care for and use the respirator. Contractors should be well-versed in OSHA requirements related to fresh air system maintenance and usage. Make sure employees are up to date with OSHA requirements on the job site. There are many options available online for a 10-hour OSHA class that can help assist in training your staff.
Personal Protective Equipment is required during all phases of spray foam jobs. Protecting our eyes, skin, and lungs is important when spraying foam insulation, cleaning guns, consolidating drums, or doing job site cleanup. Before beginning, during, and after spray foam application, installers must wear a chemically resistant suit, protective face mask, respirator, and protective gloves to cover their entire body.
These measures protect the health and well-being of individuals while also protecting the contractor’s business.
Heat
It was one of the hottest summers on record, so taking the proper precautions for you and your team was imperative. There are steps to take that allow for spraying foam through the heat without worrying about dehydration or your spray chemicals getting too hot. Tips to beat the heat:
- Hydrate and take breaks! According to the Centers for Disease Control (CDC), when working in the heat, individuals should drink one cup of water every 15-20 minutes. Ensure your installers stay hydrated and we recommend having electrolytes on site as well.
- Use a lightweight coverall suit.
- Use a cooled air supply system for your mask or hood.
- For the hottest climates, use a rechargeable cooling vest under your suit. »
- Use a system to keep your drums within the optimal temperature per manufacturer’s requirements for maximum performance.
Preventative Maintenance
Proper preventative maintenance measures are critical to prevent rig downtime and get jobs done on time. Contractors can mitigate most rig performance challenges by implementing a proactive weekly preventative maintenance process for their teams to follow.
- Check generator oil and filter changes.
- Drain air tank (daily in the summer).
- Check tire condition and pressure.
- Clean Y screens.
- Check hose condition and connections.
- Check for air leaks throughout the system.
- Make sure stick pumps are lubricated.
- Make sure there are no loose objects near the generator.
We recommend documenting these and other weekly procedures on a poster hung on the inside wall of each spray rig to make this a part of your company and team culture.
Consolidating Drums
Wasting product is not an option when you’re trying to run a profitable spray foam business. Contractors can consolidate both Part A and Part B materials. Consolidating drums is the smart thing to do to maximize yield per set. Using the instructions outlined below, it can be a simple and safe process.
Before Consolidating Drums:
- Prepare the area where you’ll be consolidating the drums. We recommend using a plastic sheet on the floor of the rig or warehouse to collect potential overspill.
- Ensure everyone taking part in the process has the proper Personal Protective Equipment. Protect yourself with splash resistant coveralls, breathing protection, eye protection, and rubber gloves.
- Read the drum labels to ensure you are consolidating the same chemicals.
- Wipe down the drum to ensure moisture and debris do not enter the drum when consolidating.
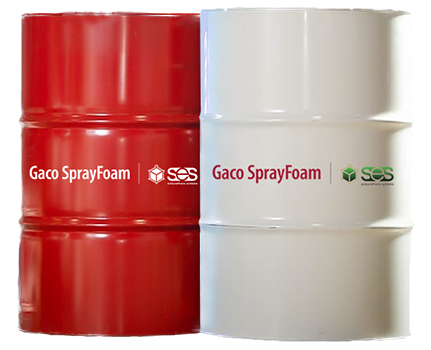
Consolidating the Drums:
- Pump out as much chemical as possible to reduce the weight of the drum.
- Consolidate chemicals quickly to avoid the need to strain out a crusted layer of material.
- Use consolidated chemicals as soon as possible to avoid use of expired product.
- Clean up the consolidation area and store drums in a dry space with lids tightly secured.
Following these and other maintenance and safety procedures will ensure your business is as profitable and accident free as possible. For more tech tips contact your Gaco SprayFoam | SES sales representative or support technician.
Contact Gaco SprayFoam | SES If you have any questions about any of Gaco SprayFoam | SES’s products or services: 713-239-0252 // gaco.com | sesfoam.com
*Spray Foam Magazine does not take editorial positions on particular issues; individual contributions to the magazine express the opinions of discrete authors unless explicitly labeled or otherwise stated. The inclusion of a particular piece in the magazine does not mean that individual staff members or editors concur with the editorial positions represented therein.
For use by SprayFoamMagazine.com & Spray Foam Magazine
Disqus website name not provided.