Spray Polyurethane Foam Cuts Connecticut Resident’s Energy Bills In Half
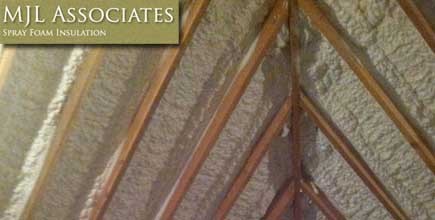
ORANGE, CT – September 3, 2014 – Unconditioned attics can often suffer under the harsh weather of changing seasons, with scorching heat or freezing cold penetrating the attic space and directly affecting the home’s temperature. HVAC systems tend to be situated in the attic, which means that the extreme temperatures can certainly add stress to their performance. Meanwhile, below in the living space, homeowners are modifying their A/C and heating systems accordingly to attain their desired indoor temperature, but to their detriment, their energy consumption is doubling along with their power bills. Case in point: Douglas Grabowski, Connecticut homeowner, witnessed an incredible spike in his energy bills through the first winter of winter two years ago. The fiberglass insulation between the rafters of his 4,500 sq. ft. attic had worn thin and significant heat transfer had caused ice damming on his roof that gave way to the threat of potential water leakage coming down into his attic. For these reasons, Grabowski decided to condition his attic and opted for a spray polyurethane foam insulation application.
Grabowski entrusted this task to Connecticut-based spray foam contractor MJL Associates, and they recommended a cost-effective and efficient solution in the installation of open-cell spray polyurethane foam between the two-by-ten attic rafters on top of the worn-out batt insulation.
“His utility bills were going through the roof – no pun intended,” said MJL’s Michael Lieto. “When we first arrived on site, the walk-up attic temperature was within a few degrees of the outside temperature, which was incredibly cold. He was also getting severe ice damming coming off the sides of his roof and that would eventually melt and leak. Judging from that, we could see how in the summer temperatures would get well over 100 degrees in that attic; it needed to be conditioned.”
Lieto said that spray foam was the viable solution to create an air and vapor barrier in the attic, and to also block heat transfer and eliminate the ice damming.
The MJL crewmembers were easily able to access the attic from a staircase on the second floor of the home. Once they were up there, they installed scaffolding to be able to work around the higher areas and the peak of the roof, which was 15 feet above the attic floor. They parked their rig, which was equipped with a Graco Reactor E-30 proportioner and Fusion AP gun, on the side of the house and pulled their hose through dormer windows on each side of the attic level. After the hose was through, the crew draped plastic sheeting on the windows, the floor, the mechanical units, and the finished light fixtures to protect them from overspray damage. They had a ventilation system that consisted of a portable reverse air filtration device that sucked air from the inside of the attic and ejected it to the outside of the house. The crew wore PPE consisting of fresh air hoods attached to respirators, Tyvek suits, gloves, and boots. Because the climate inside the attic was so cold, the crew had to heat up the substrate using portable heaters at 75 degrees ºF for 2 hours before they could proceed with the application of SPF.
Then, the crew installed nearly eight inches of Foamsulate 50, a half-pound, open-cell spray polyurethane foam formulated by Premium Spray Products, to the substrate in between the attic rafters, providing an R-30 value for the now-conditioned attic.
It took the three-man crew four days to complete the application. According to Lieto, the end result of the project showed drastic changes in the home’s insulation temperatures.
“Upon the third and final day of the project, the now spray foamed attic was within 8-10 degrees of the living space of the floor below,” said Lieto. “Not bad for a sub 30 degree winter day!”
After the project was completed, Grabowski turned his spacious attic into an additional bedroom, which he now uses for guests. The following winter, Grabowski noticed that his investment on spray foam insulation had been a wise one.
"In a winter that was 27 percent colder than last year, the addition of the foam insulation coupled with a new furnace had us about 300 gallons of fuel less than last year,” said Grabowski. “I’m told most folks use an extra tank, we were two tanks less, meaning that three tank swing alone pays for half of the installation.”
Lieto estimates that Grabowski’s investment on the SPF project will be paid back in full on energy savings alone by next year.
About MJL Associates: MJL Associates provides their clients with the latest in Spray Foam Technology. Servicing the Connecticut and New York areas since 2010,. MJL's professional work is represented in their clean craftsmanship, providing a quality product and ensuring that insulation needs are met. MJL believes in the highest levels of Customer Service, the most important value in the creation of any long term working relationship. For more information, please use the contact information and links provided below.
Disqus website name not provided.