SPF Roofing and Coatings Robot Improves Spray Application Efficiency
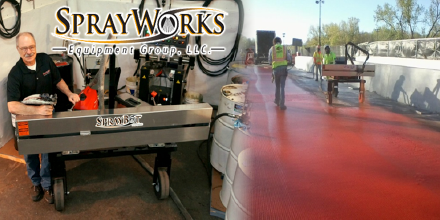
CANTON, OH–March 14, 2014–It resembles a Mars Rover, except that a spray gun is mounted on this motorized mobile spray machine. The Spraybot, from SprayWorks Equipment Group, is a hallmark of innovation for spray application equipment.
Jim Davidson, President of SprayWorks Equipment Group, LLC in Canton, Ohio, invented the automated spray application machine that was patented as the Spraybot. This roving machine is designed to evenly apply spray foam, polyurea, or other coating materials to roofs, bridges, decks, and other large horizontal surfaces. Interestingly enough, automated spray machines are finding a place in floor-coating industries that require the application of elastomers, polyureas, epoxy, and other types of coating materials.
Watching the Spraybot in operation is reminiscent of something right out of a science fiction movie. Images of Orson Wells’ "War of the Worlds" come to mind, as a long alien-like black hose, transporting the material to the gun, feeds the machine. Rhythmic clicks and hisses can be heard as the spray gun quickly oscillates back and forth, delivering a wide angle of material to its targeted surface with precision.
The Spraybot incorporates two DC motors, an on-board generator, an enclosed windscreen assembly, a spray gun mount, and a toolbox. It features user-friendly controls, an adjustable spray-head mounting device, and speed control options. The spray head can be adjusted to accommodate a wide-angled spray pattern, up to 7’ 5”, which is a wider area of coverage than most human beings can achieve. Moreover, it can process approximately 5 to 50 pounds of material per minute and can operate for 8 hours on a single gallon of gas.
The Spraybot almost seems to possess intelligence–never missing a beat as it glides onward. In the path of the Spraybot lays a smooth, even carpet of spray foam, transforming the surface as it moves. It is certainly a marvel of technology with high performance, high efficiency, and consistent accuracy.
Davidson’s vision was to create an automated spray coating machine that could perform consistently every single time it is used. In fact, the Spraybot has performed so well for contractors that some Departments of Transportation, colleges and commercial entities have written it into their specifications.
“Since so much of a company’s profits can quickly vanish through human error, I was determined to create an application process that would provide excellent results for any contractor regardless of his or her level of education or training,” explained Davidson.
Using the spraybot increases production: unlike its human counterpart, it doesn’t get tired, doesn’t mind working in hot weather or precarious places, and doesn’t need a paycheck or health insurance. However, the Spraybot will not replace the type of workers normally hired for the coatings industries. On the contrary, the Spraybot is designed to be so user-friendly that even a novice can achieve excellent results. What this means for the contractor is a reduction in errors and improved efficiency, which can translate into substantial savings.
“Contractors are seeing a 10% higher material yield, as well as a reduction in the cost of man-hours,” explained Davidson. “Consistent, even application of material is easier to achieve through an automated system, since people are affected by more variables. For example, the high frequency of starting and stopping spray equipment throughout each day adds up over the course of the job.
“When you have a number of people, each spraying via their own technique, you tend to get a lot of variation in your end product. Each spray-worker interprets the profile of a surface differently, so he or she will spray rises and valleys differently in order to compensate for the variations. The Spraybot applies material to the surface evenly, whether it’s a rise or a valley. The savings realized gives contractors a competitive edge in that it provides them with sharper bidding opportunities. This way, the savings can be passed on to the customer and/or increase profits by way of repeat business.”
Another consideration is in obtaining material thickness specifications. The Spraybot delivers one clean application at a time as opposed to a crew of workers doing multiple overlapping layers. The average spray crew consists of four to six individuals. One to two individuals can operate and monitor the Spraybot. That means that more workers are free to engage in other work, thereby completing the job faster.
In addition to the Spraybot, Jim has several patents for the spray coatings industry. His next projects will entail custom-built Spraybots that are specifically designed for specialized coating markets. This includes in-plant automated machines that are capable of applying coatings where mobility of the spray application is needed. He plans to create a new Spraybot that can accommodate a spray area in excess of 15 feet wide. Some will be laser-guided, so that the machine will be able to “sense” its surroundings; thereby, maneuvering around or avoiding barriers. Adaptations for the spraybot will include its ability to apply coatings to large tanks as well as wall and ceiling coatings. When asked about what motivates him, Jim sums it up by saying, “I do not fear the challenges themselves. Rather, I am more fearful of what will happen in the industry if I don’t find solutions.”
Spraybot Overview
Accuracy: Delivers even, consistent application of materials, virtually eliminating the common errors associated with human applicators.
Powerful Design: The spraybot is made of durable metals with grooved solid tires for better traction. The heavy-duty chain-driven spray assembly is built for durability.
Production: High yield of material and reduction of man-hours provides contractors with a more competitive edge.
Speed: The Spraybot’s speed can be varied to change the amount of material that is delivered to the surface.
Flexibility: The spraybot’s sprayer head is adjustable for different spray heights and can be adapted to fit most hand-held spray guns. The pull-pin design makes it easy to disassemble it into four components for transport and quick job-site set ups.
Affordability: Contractors report that they are able to save a substantial amount of money on their first projects, which enable them to recoup their investment for this equipment purchase within the first few jobs.
Safety: Using the Spraybot eliminates the risk of putting many workers in harm’s way. Fewer people are needed to operate the Spraybot; therefore, crew monitoring is easier.
About SprayWorks Equipment Group, LLC: SprayWorks Equipment Group, LLC is a third-generation, family-owned company, located in Canton, Ohio. It specializes in custom spray rigs, spray equipment, supplies, parts, materials, tech support and training for the spray foam, polyurea, and coatings industries. Its service area has no geographic boundaries, as it has provided customers with products and training throughout the United States, Canada, Mexico, Guam, China, Russia, and Panama. Jim attributes his business success to developing long-term relationships with his customers. “Customer success is our success. Becoming proficient in this industry takes time; therefore, developing long-term relationships with customers is crucial,” says Jim. For those interested in learning more about SprayWorks Equipment Group, please use the contact details and links provided below.
Disqus website name not provided.