One for the Books
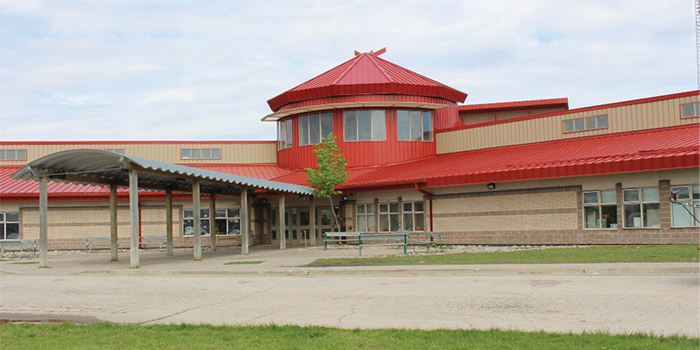
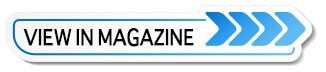
SPRAY FOAM MAGAZINE – Spray polyurethane foam’s versatility as a product means that some savvy business owners choose to segment their service markets to reach a wider customer base. Chris Lenchyshyn is one such owner. Together with his family, he owns and operates two spray foam companies in Niverville, Manitoba; Cold Country Spray Foam and Slab-Jack Kings, under the corporation name Prairie Wide Spray Foam (PWSF).
“We were looking for other things we could use our equipment for and saw that there was a lot of demand for concrete lifting in our area. We split the business into two different names to make it easier for customers to find what they need.” Lenchyshyn explains.
As family-owned businesses, their eight employees include Lenchyshyn’s siblings, parents, and several friends. Together, they provide a variety of spray foam services across their businesses and take pride in having a big impact on the community they serve.
In the summer of 2023, Slab-Jack Kings took on a concrete lifting job at the 250,000 sq.-ft. Sagkeeng Community School in Fort Alexander, Manitoba. Lenchyshyn met with the school’s principal to discuss the project’s parameters, and surveyed the school and had engineering reports performed to assess the school’s foundation. Lenchyshyn found that not only did the school’s foundation have some serious issues, it needed repairs done on the tightest possible schedule– one week.
The Sagkeeng Community school is located on a First Nations reserve near Lake Winnipeg. The school and the lake are roughly the same elevation, which caused ongoing issues with overland flooding from melting ice. When the ice in surrounding areas melted, water poured into the school’s crawl space. To make matters worse, the school didn’t have eavestroughs to divert rainwater away from the building.
The flooding problems were compounded by the concrete foundation slab not being tied into the rest of the building’s steel structure. Often, building foundations are secured with rebar dowels or other materials, but the school had what’s known as a floating slab. Floating slabs are a common and adequate foundation design, usually. But over time, the excessive water drainage led to compaction issues in the soil’s subbase, which caused the entire building’s exterior perimeter to begin to sink toward the middle, creating a bowl-shaped slope. Without intervention, the sloping slab promised to get worse with each passing year.
As if the sloping and flooding issues weren’t enough to deal with, the school’s compromised crawl space also attracted thousands of rodents. Because the settling foundation left the rest of the building vulnerable to heat loss, rats could detect the heat escaping from the building’s interior and couldn’t resist trying to burrow their way inside.
All these issues placed a massive burden on school administrators, but they also worried that fixing the problems would necessitate an extended school closure to fully excavate and repair the slab. But Lenchyshyn was confident he and his team could repair the school’s foundation quickly, and without interruption to the teachers or students.
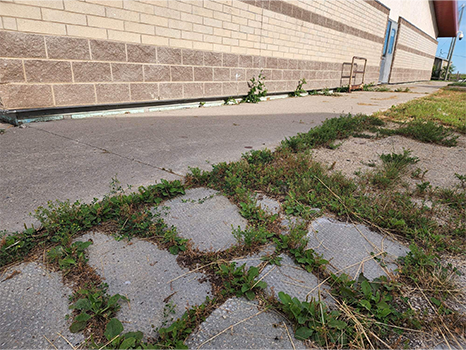
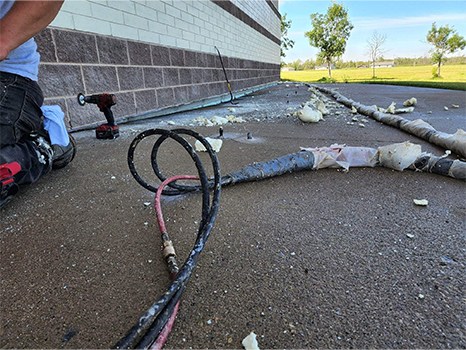
“The contract was to rectify the issue without replacing everything, with the goal of saving the school money without ruining the community’s school year,” said Lenchyshyn.
A team of five technicians from Slab-Jack Kings reported to the school for a single week in the summer of 2023. Even though the school was out of session, it was hosting a summer camp in the following week, so Lenchyshyn and his crew had to snap into action. The game plan was to lift and level the entire concrete slab around the school’s exterior, working over an area of approximately 11,000 linear feet. Before injecting the concrete lifting foam, they also installed steel angle irons to help join the slab and wall for additional structural support.

To begin the lifting process, they used five-inch drill bits to bore deep, five-foot holes into the concrete slab around the outside of the school. They drilled deep so that the injected foam could serve as a water seal between the wall and the foundation.
“Even if water did run down next to the wall, we wanted to completely stop it from permeating into the side of the foundation like it had been,” explained Lenchyshyn.
Aside from the drill, they used a variety of tools and machines to complete the job, including a Ziplevel to monitor the lift, and a concrete saw to cut into some of the slab’s joints and justify them correctly. They also used a Bobcat skid-steer loader as a counterweight during the lifting process. Because the foundation was not tied into the building and had heaved around the outside edge, they parked the skid-steer along the slab’s outside edge to prevent it from lifting while they worked on the concrete pad along the building’s exterior wall.
Using a TMC PH2 proportioner, they injected SPI’s Eco-Rise 3.5 lb. hydrophobic concrete lifting foam at 1200 psi into ports at each injection hole site. SPI specifically formulated this lifting foam in partnership with Slab-Jack Kings. Their preferred formula uses a special blend of hydrophobic foam that is 3.5 lb. rather than the commonly used 2 lb. to provide additional support in holding up the concrete over time. The foam is also designed with rise-time in mind, as it allows for greater control at the injection site as far as how far and how fast the foam spreads.
The technicians injected the foam two inches thick using a “bunny hop” technique. “Bunny hopping” involves injecting a precise amount of foam into every other hole until the concrete lifts far enough to touch the steel angle iron installed along the wall’s gap.
Lenchyshyn described the bunny hop injection technique: “Let’s say you have 500 feet of sidewalk. You’d start at one point and continue jumping from each hole until the concrete lifts to the right height at each injection point.”
After completing the lifting process, they went around and filled up the boreholes and remaining cracks in the concrete with Pecora caulk. Using surface grinders and Sawzalls, they smoothed down any remaining lifting foam to make sure everything was flush and level, then disposed of any excess material.
Because they were injecting the foam deep underground in an outdoor environment, respirators and face masks weren’t necessary. While operating the drill and other power tools, the team wore hearing and eye protection, plus steel-toed work boots. At least one member of the crew had to lie on the ground next to the wall while installing angle-irons to the gap, adding an extra obstacle to the already challenging daily grind.
The eye protection defended the crew from all manner of debris, even outside of power tool use: “It was fishfly season,” laughs Lenchyshyn. “A pretty gross time to work outside.”
By the end of the week, the Sagkeeng Community School’s exterior showed a subtle yet noticeable improvement. The slab was now flush with the walls with no gap or sloping concrete in sight. Pedestrians walking on top of the newly-lifted concrete might not be able to tell, but beneath the surface, the polyurethane foam generated a massive improvement to the slab. The foam injection material acts as a water barrier and thermal protectant, while also preventing soil erosion to maintain the slab’s stability as time goes on.
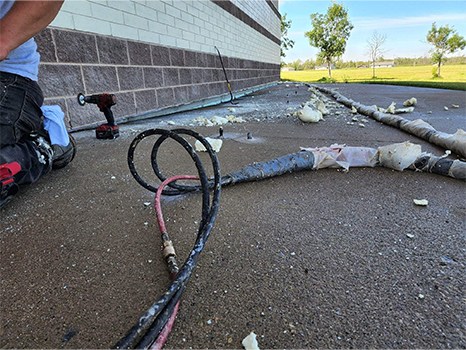
Slab-Jack King’s expert workmanship helped the Sagkeeng Community School save millions in repair fees while avoiding costly excavation. Most importantly, they made the school a more comfortable place for students to learn; free from flooding, cold drafts, and rodent intruders.
For use by SprayFoamMagazine.com & Spray Foam Magazine
Disqus website name not provided.