Don’t Forget About Your Drums

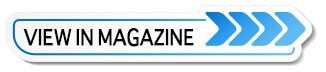
Spray Foam Magazine – As spring arrives and the temperature starts to rise, many contractors pay less attention to their drum processing temperatures. When you look at the tech data sheets from the chemical manufacturers, the processing temperatures are the only numbers that do not have the precursor of “recommended or suggested.” Good contractors recognize and go to great lengths to ensure that they keep their barrel temps at the optimal temperatures year-round, however, if not addressed, it can be a common occurrence to see barrel temperatures exceed 90 degrees as summer sets in. Many contractors fail to recognize the negative consequences of high inlet temperatures on their applications. Some of the effects include:
Lower yield and less blowing agent directly impact the performance of both open and closed cell foams.
No mix foams can start to separate. The majority of, if not all “no mix” foams on the market today are not true solutions, they are suspension formulations. The best way to get a suspension chemical to separate is to heat it up.
Higher temperatures cause catalysts to lose their potency. Catalysts drive the exotherm of the curing of the foam plastic. If they stay at a high temperature for too long, they will start to break down. This can lead to shrinking foam, yield loss, and undesirable spray patterns.
The viscosity of the chemical can increase due to the loss of the blowing agents and catalyst. That is why pour over chemicals are typically thicker.
Pumps will have more leakage both internal and external. While we are not suggesting that this is a large amount, it still can cause off-ratio foam, especially for contractors with pump lines needing maintenance.
Blowing agents boil off. This is a problem for both open and closed cell formulations.
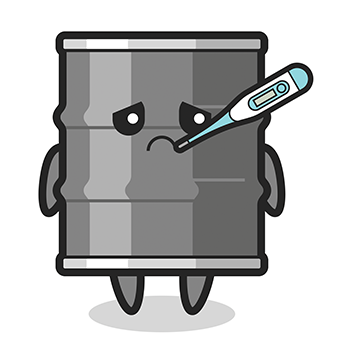
These are just some of the side effects that can occur when processing temperatures exceed the manufacturer's specifications and while you may not notice them while you are spraying, they can directly impact yield, reactivity, and density. Most contractors understand the consequences of trying to process cold chemicals and the importance of maintaining drum temperature in the winter months but paying attention year-round can help ensure your profits don’t go down when the temperatures go up.
About the Author
Justin Strombeck started his career in the spray foam industry, over 21 years ago, on the contractor side doing both roofing and wall foam applications. Since then, he has been the technical manager for a large chemical company where he oversaw training, built a nationwide technical team, and helped formulate and credential foams in over 20 countries.
Over the last five years, Justin has worked for Akurate Dynamics consulting with physicists, mechanical engineers, software engineers, chemists, and other industry professionals to help move the technology of the equipment used in the spray foam industry forward.
For use by SprayFoamMagazine.com & Spray Foam Magazine
Disqus website name not provided.