American Midwest
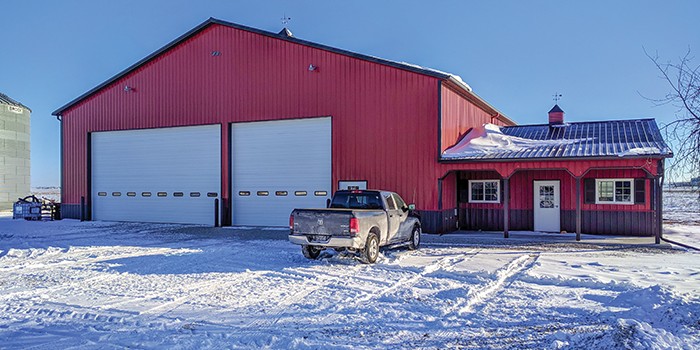
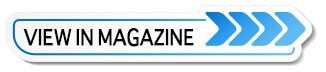
COLFAX, ILLINOIS – June, 2018 – In the Midwest lies the “Prairie State” of Illinois marked by farmland, forests, and rolling hills. Nestled within Illinois’ Bloomington-Normal (B-N) Metropolitan area is the quaint village of Colfax, where there may be as many livestock as people. Dubbed the commercial hub of surrounding prosperous grain-growing farms, many residents in the rural areas of the B-N community own pole barns to house farming equipment, tools, and office space.
One family in the village was in the process of building a pole barn (a farm building with no foundation and with sides typically made of corrugated steel panels supported by poles in the ground set at eight-foot intervals) to use as a shop and office for their family farm business.
With annual temperatures ranging from sub-zero to low 90s throughout the seasons, the owners were tasked with finding the ideal insulation material to keep the environment inside the pole barn as comfortable as possible without exorbitant utility bills.
The project builder suggested that spray polyurethane foam would provide the best insulation for the barn, and the family took his advice. Having worked with them in the past, the builder called in Slagel Insulation Inc. (SI) to take on the job.
“The owner wanted something that would not degrade over time, keep the building energy- efficient, and seal out any rodents that may try to get in,” explained Kevin Slagel, owner of SI. “Since the building would be used as an upscale shop, we knew spray foam would provide the best results for the daily farming activities that would be occurring within the structure.”
The SI crew applied three inches of Henry PERMAX 1.8 lb. closed-cell foam to the walls.
With two days to complete the first phase of the job, the two-man crew geared up in Bullard Air-Fed helmets protected by SI’s custom-made lens covers, gloves, and spray suits, and went straight to work. The building encased over 6,300 square feet split between the shop, office, break room, and kitchenette. Since the ceiling had not been installed yet, the team began with spraying the interior walls of the structure. Prior to application, the windows, doors, and floors were masked off to prevent overspray damage.
Using a Gusmer HV20-35 proportioner, a Probler P2 gun, and 265 feet of hose, the SI team applied to the metal sheathing of the walls three inches of Henry PERMAX 1.8 lb. closed-cell foam. Since the walls in the shop were 18 feet tall, the crew utilized a scissor lift with fall protection to reach it all. Once the foam had cured, the builders lined the interior with corrugated metal.
Months later with the interior completed, the SI team was brought back to insulate the top side of the finished ceiling (attic floor). A six-mil vapor barrier had been attached to the bottom of the trusses prior to the installation of the noise-deadening, perforated steel ceiling panels. The crew finished the project by applying three inches of PERMAX closed-cell foam to the attic floor. Fire blocking had already been put in place at the top of the exterior walls to seal off any cavities, and because of the resulting complete air-seal of the shop space, no foam was applied to the underside of the roof.
The office space was connected to the store with the walls reaching 24 feet high. Once completed, it was adorned with wooden ceilings and furniture for a rustic style design.
“Spraying the attic floor enabled the building envelope to be sealed, and allows the owner to service mechanicals in the attic more freely than with conventional blow-in,” says Slagel. “SPF in the attic also fixed another problem with loose-fill and perforated ceilings: the building owner had close acquaintances with similarly designed shops, and they found that due to the pressure changes when large overhead doors are opened on windy days, air blowing through the perforations would cause the vapor barrier to ‘pop up’ and catapult the blow-in insulation into piles that had to be put back in place every season. Spray foam obviously does not have this issue.”
Completing the attic phase in two days, the only hurdle noted by Slagel was the hot summer days that saw attic temperatures soar as high as 101°F degrees while they worked in the confined space. Yet even in these extreme conditions, the workmanship of the SI team continued to shine through.
“The client was very impressed with the results due to the added structural integrity and energy efficiency that will be provided for years to come,” states Slagel.
And as a testament to SI’s quality workmanship, the owner later had the team perform more work in the family’s home after they completed the job in the barn—but that’s a story for another day.
For more information on Slagel Insulation, go to www.slagelinsulation.com.
Disqus website name not provided.