Adapt & Overcome
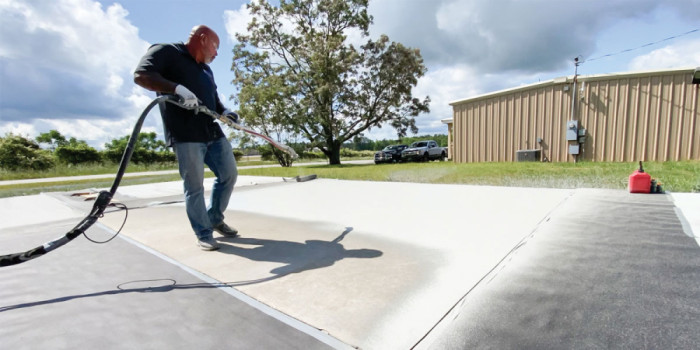
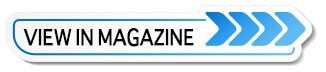
Spray Foam Magazine – Fall 2020 – Most small businesses such as polyurethane concrete lifting contractors, have had to adapt their business to the coronavirus pandemic. Many have found offering additional services has helped them during the uncertain times. Any service add-on can help create new cash-flow and provide additional options to better service your customers.
Those utilizing polyurethane foam for concrete lifting can find that fixing a geotechnical problem does not always fix the aesthetics on a project. Adding onto your existing business to help address concrete or asphalt beyond polyurethane foam, does not have to require a large investment or extensive training. Resurfacing material such as CEM-Shield SR, has become an easy service add-on for many utilizing polyurethane foam for geotechnical applications.
CEM-Shield SR’s unique chemistry of highly engineered resurfacing material forms an extremely durable polymer micro composite wearing surface for concrete and asphalt substrates. These critical characteristics, including fast setting times with extended working time, bond and flexural tensile strength results in a strong reliable surface. Incorporating this add on to your existing business will not only protect concrete or asphalt from environmental distress, but has extreme resistance to fuel, oil and de-icing salts. This material can be applied on multiple applications; driveways, patios, pool decks, sidewalks, parking garages, parking lots, bridge decks, warehouse floors, void filling and precast forms.
PCMO stands for Polymeric Composite Micro Overlay and is made up of thermosetting resins, binders, aggregates and add mixtures. When mixed with the appropriate amount of water, the PCMO will start the chemical reaction that allows the product to be applied and then cure over. This material can be spray applied or manually applied. The spray applied method operates Graco sprayers capable of utilizing this material and custom wands that can be purchased with the equipment for different spray patterns. The manual application includes the squeegee method, boom finish method and the spray knock down method.
CASE STUDIES
On multiple projects, case studies were conducted using CEM-Shield SR that required different solutions for a variety of projects. A case study was completed at a 8,000 sq.ft. gas station parking lot that had major deterioration, including failed concrete areas, spalling, scaling, random cracking and many trip hazards. CEM-Shield SR was applied to the gas station parking lot and the job was completed in two and a half days with partial gas service maintained throughout the project. The stakeholder realized a significant cost savings compared to removing and replacing the concrete. All completed work was turned back to traffic with 12-15 hours of cure time.
A second case study conducted using CEM-Shield SR was for the New Mexico DOT. The DOT was experiencing chronic problems with bridge decks through the state. The concrete decks had major spalling issues due to the generous use of de-icing salts, allowing water to penetrate the concrete and was subjected to multiple freeze-thaw cycles. The DOT had been using epoxies as their solution and were not happy with the results; constating raveling of aggregate (friction). The DOT was seeing a new solution to this problem to compare with the epoxy system. The solution for the DOT issue was to apply two layers of CEM-Shield SR with black color for a faster de-icing cycle. A heavy broom finish was applied for maximum friction. The job was completed in six hours and the bridge was opened within hours of completion. The results of the CEM-Shield SR application were found that in over seven years time, CEM-Shield SR had no signs of wear and was still a deep black color. NMDOT has a very favorable opinion of the CEM-Shield “Slurry” solution because there is no aggregate/ friction loss as there is with the epoxy systems. There also was significant cost savings on the installation price of CEM-Shield SR versus the epoxy application. The black color proved to help melt snow and ice quicker and is the preferred color for the future maintenance of the bridge deck systems.
A third case study using CEM-Shield SR, was applied to a 330,000 sq.ft. parking garage. A newly poured parking garage at Planet Hollywood was rejected for various issues. The challenge with this project was to make the area look consistent with the rest of the poured concrete throughout the parking garage. The expectations were that this parking garage would get extremely high traffic and had multiple sharp turning areas. The solution had to be very durable to hold up to heavy loading and shear. It also had to be a fast-setting application, because it was indoors, and the parking garage needed to be open right away for business. The solution on this project was to apply CEM-Shield SR in multiple layers to shield the concrete surface and minimize future deterioration. A heavy broom finish was applied to match the rest of the project. Prior to application of the CEM-Shield SR, all areas were properly prepared; shot blasted, grinded, acid etched, power washed and chipped out leveled as needed. The results of this case study showed that three years after the project was completed using CEM-Shield SR, the surface is still in place. The original broom finish is strong with only a few locations showing signs of wear.
Application methods using a PCMO resurfacing material require mixing that can be used by a single bucket, a cart bucket or utilizing a continuous mixer. Different additives include color pigments, accelerators, retarders and extenders and may be used with the resurfacing material depending on the project.
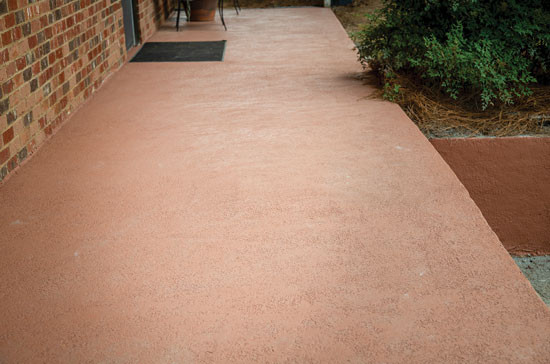
Knock down application method with terracotta stain for front porch resurfacing utilizing CEM-Shield SR
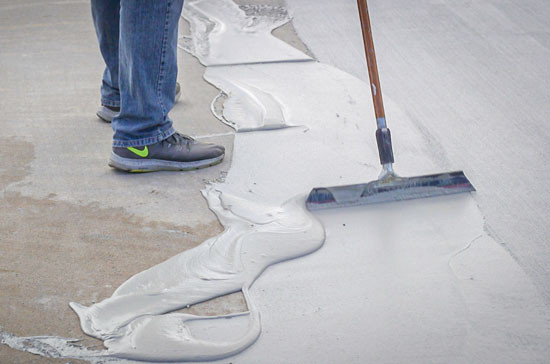
Cem-Shield SR application utilizing the squeegee method
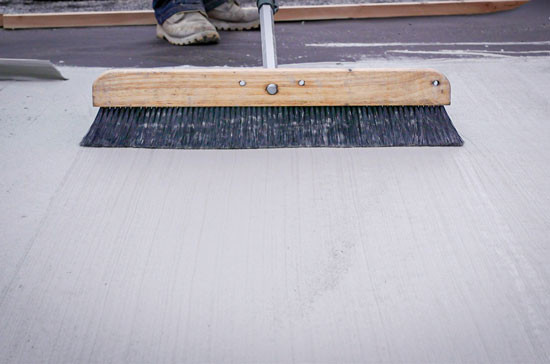
Manually applied Cem-Shield SR with broom finish.
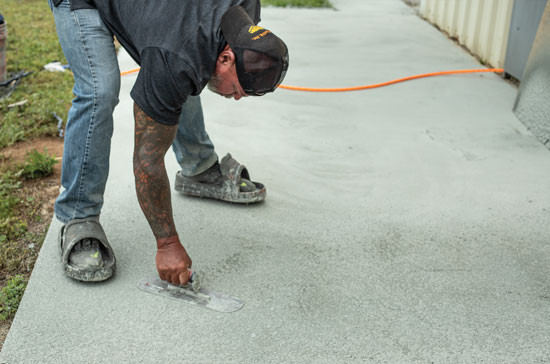
CEM-Shield SR knock down method application for walkways.
For polyurethane concrete lifting contractors, soil erosion is the leading cause of sunken and cracked concrete slabs. After utilizing polyurethane foam beneath a slab, it brings the sunken concrete to be level but does not repair cracks and other environmental wear on the concrete surface. Once stabilizing the concrete with the polyurethane foam, contractors are often left without a solution to fix the visible damage from the damage that was done beneath the surface of the slab. Utilizing a PCMO now offers a solution to contractors who find these surface issues while lifting slabs.
With the current situation of COVID-19 affecting many small businesses, adding additional services such as a concrete resurfacing application can bring added value and options to their companies list of current services. The addition of a new service like concrete resurfacing will allow concrete lifting businesses to reach new clients who want to adjust the look of their existing concrete, while being able to offer a solution for a deeper routed problem that can require the existing service of polyurethane concrete lifting. Concrete lifting projects now can provide clients the final touch on fixing their existing concrete issues while adding more value to their business. With a low-cost investment a PCMO material can become a great addition to help polyurethane concrete lifting contractors adapt their business during the uncertain times of COVID-19.
Contact Spray Foam Systems
Direct any questions about adapting concrete lifting businesses during COVID-19 to SFS:
Phone: 877-737-4362 // Website: www.sprayfoamsystems.com
*Spray Foam Magazine does not take editorial positions on particular issues; individual contributions to the magazine express the opinions of discrete authors unless explicitly labeled or otherwise stated. The inclusion of a particular piece in the magazine does not mean that individual staff members or editors concur with the editorial positions represented therein.
Disqus website name not provided.