The Benefits of Using Recycled EPDM
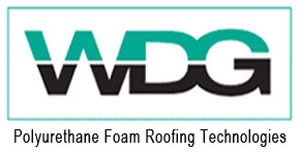
Every competitor wants to eat his or her competition for lunch. In a sense, that’s what West Development Group (WDG), a leader in sustainable roofing products and practices – is doing when they use recycled EPDM in our System 14 roof system.
Ethylene propylene diene terpolymer, commonly referred to as EPDM, is currently the number one roofing choice of architects, specifiers, and contractors for new and replacement roofing projects. The rub, however, is that when these roofs need to be replaced, roof tear-offs frequently go straight into rapidly filling landfills. And, like old tires, EPDM doesn’t decompose for 10,000 years.
According to the U.S. Environmental Protection Agency (EPA), construction and demolition debris accounts for over 136 million tons of waste each year, which is 40% of the country’s annual total. Of this, commercial and industrial roofing is estimated to account for 4% (5.5 million tons) and a significant portion of this is EPDM. The EPA estimates that over one billion square feet (185,000 tons) of EPDM roofing is removed and put into landfills every year. That translates to 33,000 40-yard dumpsters or over 120,000 full-size cars.
Then there’s the petroleum problem. This rapidly decreasing resource is exponentially rising in cost. Guess what? EPDM products are made primarily from petroleum. As the price of petroleum goes, the price of EPDM goes.
In some states, tires can no longer be dumped in landfills and companies have already found the environmental benefits and economic value of recycling tires to provide carbon black and other minerals for reuse in rubber products. Automotive components, tires, plastics, building and construction materials, and industrial rubber goods – not to mention new commercial and industrial roofing systems – can all use recycled rubber from tires.
Not all EPDM, however, is suitable to recycle, but the EPDM Roofing Association (ERA) projects that 113,500 tons per year currently have a viable and beneficial end use with today’s recycling technology and grinding equipment. Even though ERA research indicates that it is logistically viable to remove and recycle EPDM from a roof to create other products, very little EPDM is being recycled. That’s about to change.
When you consider the damage to the environment from EPDM tear-offs and the spiraling cost of EPDM petroleum-based products, it’s clear that there are tremendous advantages to recycling EPDM.
Ahead of the Curve for Recycling EPDM
A few years ago, WDG began exploring green roofing options and developed System 14, an environmentally friendly silicone roofing system that eliminates petroleum-based solvents and uses recycled EPDM. A silicone topcoat is sprayed over a soy-based, spray polyurethane foam (SPF) to create a moisture-resistant, seamless, self-flashing seal. (Visit the WDG Web site at www.wdgsilicones.com for more information about System 14.)
To help ensure the success and functionality of System 14, WDG had to develop a silicone, in fluid form, that contained no solvent, but could be sprayed. When that problem was solved, the company developed a formula for producing a silicone roof coating with 20% recycled EPDM. Once perfected, WDG introduced the R2R (Roof-to-Roof) process and is now the only roof system manufacturer to use recycled EPDM to strengthen and enhance the physical properties of the silicone topcoat. Using recycled EPDM is ideal for the silicone coating of SPF in roofing applications because it was originally formulated for exposure to an outside harsh environment, including UV rays, ozone, water and ice. Fire retardants are also included in the original formulations.
Recycling EPDM: The Process
West Development Group’s EPDM recycling efforts, along with the company’s R2R process, have been so successful that WDG recently opened its new recycling facility at its headquarters in LaGrange, Ohio.
WDG begins the recycling process with sheets of EPDM obtained from roof tear-offs. Roofing contractors typically pay waste company’s to haul away the EPDM rubber to land fills. WDG will take the EPDM for recycling free of charge – depending upon distance, sometimes a nominal travel/pick-up fee is charged. It’s a win/win situation for the contractor, WDG, and the environment.
The EPDM sheets arrive at the recycling facility in bins. A granulator pulverizes the EPDM into crumb that is auger-fed into a hopper that automatically turns off when full. The granulating process generates significant heat as it pulverizes the EPDM sheets into crumb rubber. To keep the crumb from turning into a sticky mass of goop, the granulator must be cooled during this operation. To reduce electrical energy consumption, WDG uses water from a 500,000-gallon underground reservoir – routing it through the facility’s pump house – to cool the machine with eco-friendly geo-thermal energy. The water is then recycled into the reservoir. A traditional cooling process would employ refrigeration and much more energy consumption.
After the EPDM sheet is ground into crumb rubber, a rotating door spins through an airlock and a cryogenic screw pulls and dumps the crumb rubber into a horizontal bin/hopper where it is auger-mixed with -310 degree liquid nitrogen. When the mixture reaches -200 degrees, the optimum processing temperature, it is ground and shredded into a uniformly and finely ground powder. The pulverized EPDM does not lose any of its original chemical or physical properties. Once the mixture drops to a low enough temperature, the rubber crumb reaches the consistency of shattering glass and is then ready to grind into mesh. The cryogenic turbo mill system employs a self-adjusting temperature control that maintains both the temperature of the liquid nitrogen tank and the grinder.
The rubber crumb processed by WDG’s cryogenic mill is pulverized into powder that is 100 to 325 mesh-milled rubber. The EPDM then moves into a cyclone that separates the liquid nitrogen from the rubber. A second airlock drops the rubber mesh through a classifier, which measures and determines whether the mesh is fine enough to be used in WDG silicone products. If not, it is run through a second cyclone and sent back to the hopper for re-grinding. WDG grinds approximately 1,200 pounds of EPDM per hour using the process, enough for approximately 600 gallons of the company’s HSS 540 Silicone Coating.
There is absolutely no waste – zero – in this process.
From the grinding warehouse, which is insulated with WDG’s environmentally friendly soy-based spray polyurethane foam (SPF), the 200 mesh EPDM is transported to the roof coating blender for the production of WDG Solvent-Free R2R (Roof-to-Roof) Silicone Coating.
These environmentally responsible practices in the manufacturing process, and throughout WDG facilities, make System 14 a 360-degree “green” product.
Currently, this pulverized EPDM is being used exclusively for WDG products. As the volume and the process are expanded at WDG, there are plans to sell the EPDM mesh to other manufacturers that need filler, such as carbon black, when making new products from recycled rubber. Other companies are commercializing recovered carbon black from recycled tires and various types of scrap rubber as the trend to reduce the carbon foot print gains popularity and the price of petroleum continues to increase. EPDM, however, isn’t being recycled as much as tires at this point, but that may change as the word gets out about the environmental and financial benefits.
Recycling EPDM: The Benefits
When WDG began its research into making green roofing products, they found that production costs were often reduced, performance improved, and marketability skyrocketed because of the green movement in general and, specifically, because of programs such as LEED credits directed to the construction industry.
When developing our System 14 roofing system, WDG was committed to ensuring that the new products would be environmentally beneficial, economically viable, and functionally equivalent to the products being replaced.
Environmentally Beneficial – Using recycled EPDM for new products in place of virgin resources offers benefits that surpass conserving petroleum. For instance, carbon footprint reduction can be easily achieved by using systems and products that incorporate recycled EPDM as an ingredient because it saves the environment from the release of volatile, ozone depleting, or petroleum-based waste. Collection methods for EPDM are simple, and recycled EPDM construction products fit well into the LEED credits program.
Economically Viable – Millions of dollars worth of totally recyclable rubber are being dumped into landfills annually. In addition to reducing waste in landfills, there is a tremendous amount of money that can be saved on shipping, handling, managing, and disposing of waste by using EPDM and other waste to manufacture new products using recycled materials. As addressed earlier in this article, there are numerous viable uses for this material that will save money, energy and natural resources when manufacturing new products. The cost of collection and processing recycled EPDM is considerably less than the cost of the materials it is capable of replacing. For example, EPDM costs about $0.40 per pound as compared to Titanium Dioxide at $1.50 per pound or Carbon Black at $3.19 per pound. To encourage recycling of EPDM, programs such as Ohio’s tire impact fee may be considered. Ohio charges a $1 per tire fee per tire for wholesale sales. A similar program could be implemented based on distributor sales per square foot. Finally, rubber mill technology is already capable of production rates that meet market needs at a low cast and, though the production process is not labor intensive, regional grinding mills will provide new jobs.
Functionally Equivalent – EPDM, like tire rubber, contains high contents (about 25%) of black carbon, a very common and widely used functional filler for products that can use recycled rubber, such as commercial roofing and other building products, footwear products, tires, epoxies and sealants, to name a few. EPDM is UV stable and retains its original physical properties. The stability and physical characteristics of EPDM make the logistics of packaging, shipping, handling, production and distribution simple and economical. And, as noted, the quantity of EPDM available is in no short supply. The life cycle of disposed EPDM in a landfill is 10,000 years, so it certainly isn’t going to break down as an ingredient in compatible products.
Contact: Richard West, President
West Development Group
(866) 924-4585
info@wdgsilicones.com
Disqus website name not provided.