SPF Roofing Application Seals Canadian Roof From Pooling and Leaking Issues
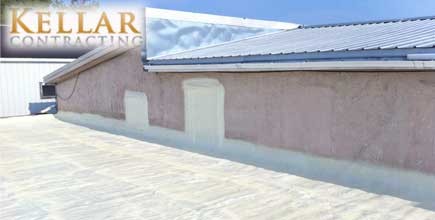
DRYDEN, ON – September 4, 2013 – When taking over a 100-year old building so that he could run his furniture appliance business, a Canadian business owner noticed a leaking problem coming from the roof. The building had a split roof system: a flat roof and a low-sloped metal roof. The flat roof exhibited significant pooling in certain areas and the metal roof had cracks where the water was infiltrating. Over the years, the owner had his roof patched with different systems, but, to his detriment, none of said systems gave his roofs a permanent fix - until he discovered spray polyurethane foam roofing.
After thoroughly researching SPF roofing systems, the owner decided that these systems could waterproof his roof once and for all. He brought in Kellar Contracting (KC) for the project, which consisted of applying SPF to the 5,500 sq. ft. split roof – 2,500 sq. ft. for the lower EPDM flat roof and the 3,000 sq. ft. for the upper metal roof.
"After inspecting the roof and the problems it had with pooling, especially on one of the low-lying corners of the bottom flat roof, we realized that spray foam insulation would resolve the problems here," said KC's owner Keith Kellar. "We needed to effectively get the water to roll off the roof, which the cracks and other problems on the roof made difficult."
The KC crew used ladders to get up to the roof and dragged the hoses from the spray rig as they went up. Since the flat roof was only 14 feet from the ground and the top metal roof was four feet from the flat roof, the crew opted for the use of ladders instead of scaffolding. For overspray protection, the spray applicator was encased inside an overspray cage that KC fabricated out of wood and mesh screening.
"The cage worked out very well for us," said Kellar. "We had absolutely no complaints of overspray and I definitely recommend its use."
Kellar explained that powerwashing the roof was not necessary because it rained heavily during the days that the crew was on site, so they went ahead and cleared off the area from any gristle and debris with brooms. Kellar said that the crew intended on priming the metal decking of the roof, but it was determined upon inspection that the substrate was galvanized and the SPF would adhere without any problems. The crew wore PPE and fresh air respirators during the job.
The crew installed 1.5 inches of Premiseal 280, a 2.8 lb. closed-cell spray polyurethane foam made by Premium Spray Products (PSP) on the split roof system. In addition to the SPF application on the split roof system, the screw sprayed a parapet wall on the street-facing side of the flat roof and a small section of wall connecting to uneven surfaces of the metal roof. Nearly three sets of foam were applied during the SPF application. The crew then applied on top of the foam roughly 40 dry mils, in two coats, of white Premicote 1400, an acrylic liner coating also made by PSP. The crew utilized a total of five 55-gallon drums of acrylic coating.
"We cross-hatched the coats so that we got better coverage," said Kellar. "By doing that, we caught every single pocket on the roof."
The KC crew had a single rig on site equipped with a Graco Reactor E-XP2 proportioner and a Graco Fusion air purge spray gun for the SPF application. A Graco X7 Airless paint sprayer was utilized for the coating installation.
Kellar noted that because application of SPF was planned ahead of time, it was precise and split roof was completely regraded so that the water would not longer pool but fall off the roof.
"I watched water linger on the roof for a long time, especially after it rained," said Kellar. "The SPF totally graded the substrate and also allowed the roof to be higher than the scuppers so the water would actually run off from the side of the roof instead of pool. There is no more standing water, and the foam sealed that entire roofline from leaks"
The SPF application also provided an R-10 value, giving the building a much cooler roof. According to Kellar, the owner had a smile from ear to ear.
"He doesn't worry about anything relating to leaking anymore, and he shouldn't have to," said Kellar. "He made the right choice in spray foam."
About Kellar Contracting: Kellar Contracting has been servicing Dryden, Ontario and its surrounding area for many years. Their excellent customer service combined with unmatched pricing has kept their customers loyal, keeping them coming back each time a new project arises. For more information on Kellar Contracting, please us the contact information and links provided below.
Disqus website name not provided.