Safety, Innovation, & Sustainability
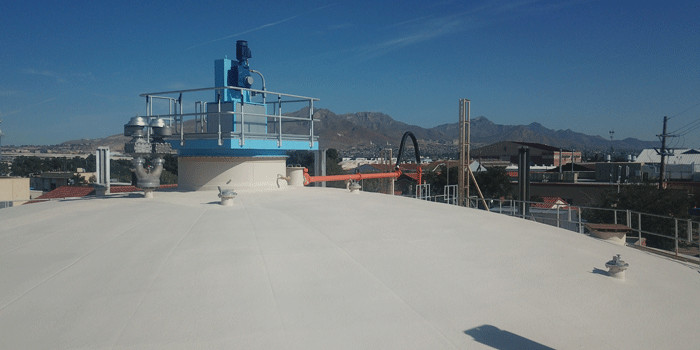
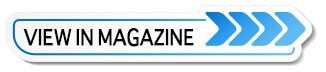
Spray Foam Magazine – Show Issue 2020 – Safety and sustainability, we all know they exist but how much time and effort does a company put into these factors?
Not only are these aspects of a business crucial to the people that work there, they are essential for business success and originality and progression in the spray foam industry. According to OSHA (Occupational Safety and Health Administration), integrating safety and health into sustainability provides an opportunity to better protect workers and achieve a truly sustainable organization.
New Era Spray Foam, a locally owned and operated business servicing the Southwest region of the U.S., specializes in the installation of spray foam insulation systems in residential, commercial, and industrial applications for both new construction and retrofitting of existing structures. They pride themselves on having highly trained applicators and the latest equipment, while promising to do it right the first time with their applicators trained to treat every project as if it were their personal project.
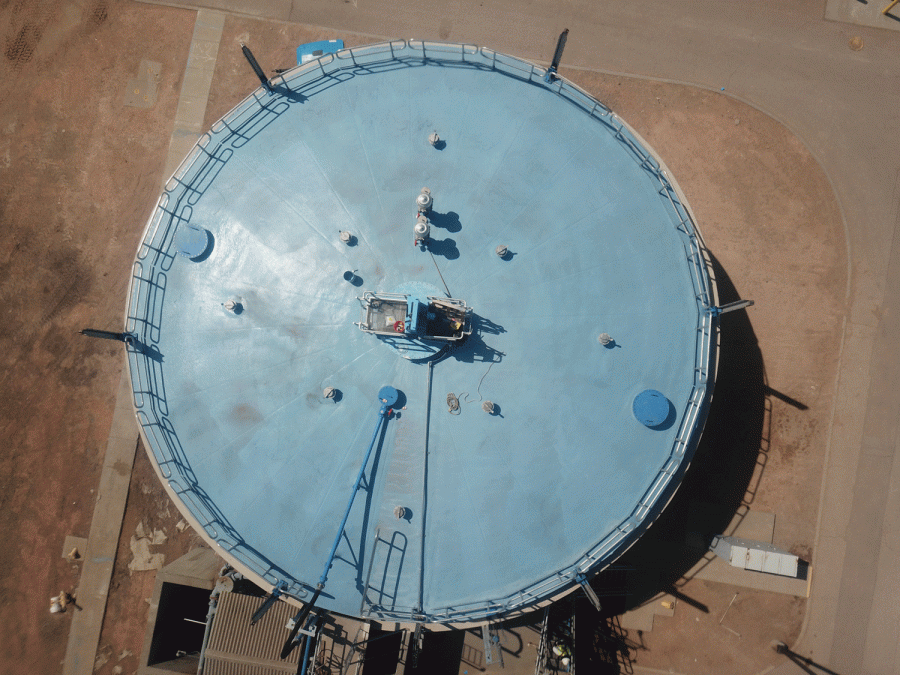
The award nominated application was completed at El Paso Water Utilities Fred Hervey & Haskel Water Treatment Plants in El Paso, Texas with the job totalling 7,800 square feet. The installers sprayed three inches of 2.8 pound roofing foam and coating system designed to insulate the lid of digester tanks at a sewer treatment plant.
The innovation materialized when problems were encountered. The precision in the installation of the tank projects were key with the lids having to be balanced in order for them to rise and fall with the volume of methane and water inside the tanks. Therefore, the foam and coating had to be precise for the proper operation of the lid track system to be successful. The installers determined that wrapping all the aluminum guard rails with tin foil was the fastest and most efficient way to protect the guard rails from overspray. Doing so made the installation and clean-up process extremely fast. »
The overspray was a constant issue throughout the application process due to the high winds in the area. Overspray curtains were required and utilized every day, so the team used a boom lift to string cable around the tank in order to properly install the curtains around the tank area. The use of the permanently installed guard rails was an additional requirement since the tanks are over 30 feet tall, and the entire tank needed to be properly masked and protected from the overspray.
Innovation – Insulating the lid was designed as a measure to improve the performance of the digester system, whose job is to recycle methane gas that is utilized to operate other parts of the plant. Once in service, and the job was completed, the plant has seen and reported an increase of 42 percent recovered methane gas. This is due to the boost in operating temperatures of the tanks and consequently has increased the productivity of the methane recovery system. The sewer treatment plant recognized the increase immediately and is currently vetting New Era Spray Foam in 2020 for several more tanks.
Environmental Sustainability – The increased efficiency of the system due to the insulation on the lid will help to reduce the use of fossil fuels for the operation of many systems in the plants. EPWU (El Paso Water Utilities) is hoping that once all the tanks are completed and operational, the use of fossil fuels may possibly be eliminated for all digester functions. Delivery was also paramount due to the scheduling of the other trades and equipment manufacturers for testing and balancing of the lid and the tracking systems.
Equipment – The equipment used on this project included the Graco GH 2 and the Graco GS 300 coating pump. The foam Sustainable Polymer Products used was 2.8 pound roofing foam with silicone top coating with the material supplied by Sustainable Polymer Products.
Best Practices – The job met all of the state and local requirements and the applicators have a written safety plan with toolbox talks monthly. All of the applicators have been trained on the job by senior applicators and all employees are CPT trained with one master installer and OSHA 30 certified, George Tollen, on the jobsite. All of the applicators had additional manufacturers training with the applicator, Evan Estes, currently working on his master installer certification.
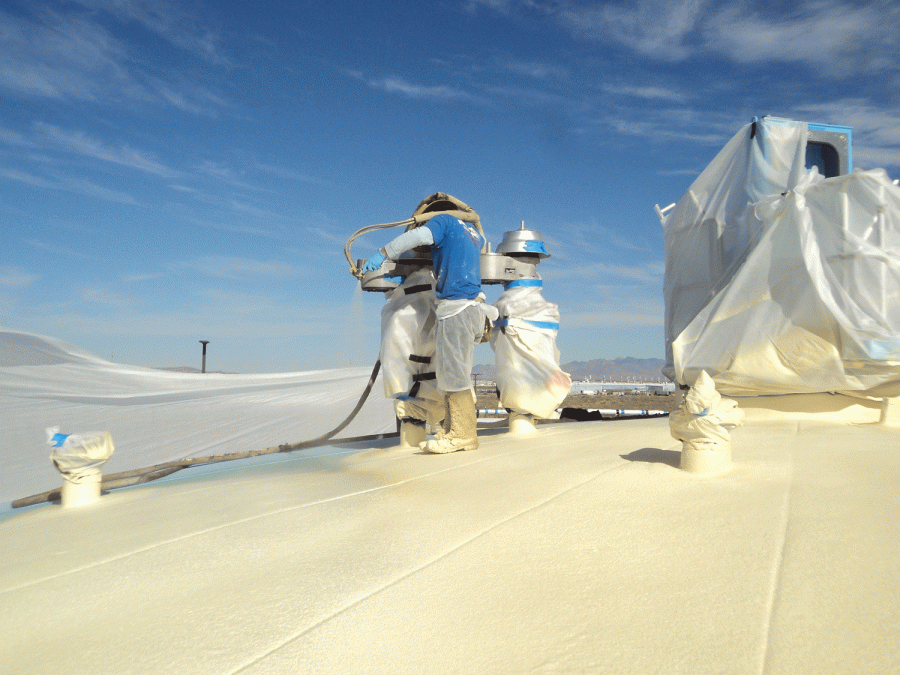
Safety – Safety is critical when you walk into industrial plants. The safety officers at the plant, whose only job is safety throughout, can make life miserable if the spray foam applicators are not ready for it. When walking into these safety meetings, have all your plans on paper as it makes life so much easier than the typical, “We don’t have a written plan” answer. The team leaned heavily on their insurance carrier for assistance making sure all their safety plans were current and by having everything in writing they were organized and professional. The team at New Era Spray Foam encourages anyone and everyone to call their personal carrier and have them review or even write their plans. This planning will save a mountain of headaches.
New Era Spray Foam has demonstrated the highest level of professionalism, innovation, safety, and sustainability attributes and Spray Foam Magazine wishes them the best of luck.
Disqus website name not provided.