New Firehouse Insulated With Open-Cell Foam After First Contractor Calls It Quits
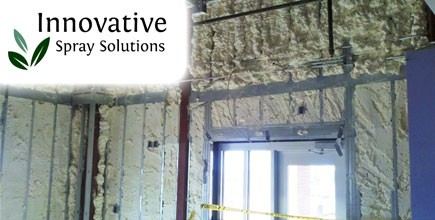
WINSTON-SALEM, NC – January 17, 2013 – Winston-Salem is nicknamed the "City of the Arts," but may be better known for its history in the tobacco industry and as the birthplace of Krispy Kreme donuts. The city is a popular tourist destination as well as a well-populated, family-oriented community. With an increase in population comes an increase in the need for more commercial and public facilities, one of which was Firehouse 19.
The new firehouse's construction had major setbacks, however. The project's initial general contractor, who the county hired to install wiring, insulation and drywall, filed for bankruptcy and left the site without completing the job. Building inspectors discovered that not only did the original general contractor leave the jobsite before running wire or installing insulation, he hid the empty wall cavities with sheetrock.
So, the development company and various sub-contractors, including Taylor Interiors LLC of Charlotte, had to start the process over again by taking the drywall down. Tarris Arnold, Taylor Interiors' owner, contacted Innovative Spray Solutions to apply the spray foam insulation.
"Not only was the insulation missing," said Innovative's co-owner Richard Farist, "all of the conduits were put in place with no wiring in them. They had to go through and run new wiring to get it up to code. They had their hands full."
Upon arrival at the jobsite, Innovative was surprised to discover that much of the interior work in the building was already in place.
"I was under the assumption that it was an open building and that we'd be working on a scissor lift around the circumference, and then I got there and saw that it was a completed building," said Farist. "It was almost like a remodel. Everything was in the way – literally."
Although Farist had put in a bid to apply two inches of closed-cell spray foam to the building, the county came back just before Christmas, requesting five inches of open-cell foam instead.
"They were very inquisitive about R-values and performance benefits," said Farist.
Before application could take place, crewmembers prepped all the windows with plastic sheeting to protect them from overspray. Since the floors were unfinished, crewmembers planned to scrape the foam off the floor after they finished spraying before tile was installed.
After their bad experience with the first general contractor, the county hired several county engineers to overlook the progression of Innovative's spray foam application process.
Innovative used a custom-built proportioner and spray foam rig, which was made for them by S.P.E.C. Technologies. Crewmembers applied five inches of ThermoSeal 500 0.5 lb. open-cell spray foam between the six-inch steel stud framing of the exterior walls, up to the roofline. The entire spray area for the project was 5,500 square feet.
Although the initial open-cell spec called for 5 inches of foam, the inspectors decided they wanted the foam to be flat and flush with the six-inch studs, so Innovative went back over their first pass to fill in the remainder of the wall cavities. Crewmembers then trimmed the foam back using a saw tool and Schmidt & Dirks CI cutter combination.
For overspray protection, crewmembers used "sacrificial" boards to create a four-by-eight-foot spray booth, which they propped against the walls as they moved from room to room. Six-foot scaffolding and ladders were also employed.
"I moved extension ladders more in a week than I have in the past year," said Farist.
For the crewmembers' safety, they used Allegro fresh air masks and hard hats while spraying. Since the windows and doors were open during application, no fans were needed for ventilation. The only other trade present during the project were the electricians, who were advised to move to the other side of the building while spraying took place.
It took two crewmembers four 14-hour days to complete the spray foam project in January of 2013. Innovative drove four hours from their location in Georgia to get to the jobsite.
There was still a lot of work to be done to complete the firehouse and the county wasted no time getting it done.
"The inspector gave the drywallers the go-ahead to immediately start hanging the drywall again before we were finished," said Farist. "We literally had to take our scaffolding away from them so we could put it back in our trailer to head home."
The county was very pleased with the new insulation and commended Innovative for their efforts under the circumstances.
"The county engineer came by and was ecstatic," said Farist. "The inspector complimented us on the appearance of the work, especially under the difficult working conditions."
About Innovative Spray Solutions, Inc.: Innovative provides customers with a reliable and eco-friendly product that withstands everyday usage for residential, commercial, and industrial settings. Innovative installs open and closed-cell spray foam insulation for homes or businesses. The company is family-owned and operated in Blue Ridge, Georgia. For more information about Innovative Spray Solutions, Inc., please use the contact details and links provided below.
Disqus website name not provided.