Liquid-Component Injection Foam Provides Advantages Over Dry-Mix Alternatives
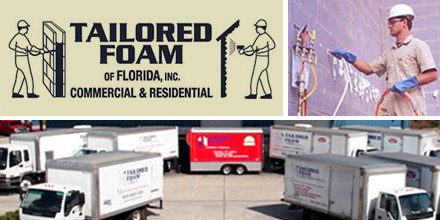
SANFORD, FL–January 16, 2014– Quality is a frequently cited attribute when companies talk about their products and services. However, merely mentioning quality only goes so far; it’s much more effective to actually prove it. Tailored Foam of Florida Inc., the largest installer of foam masonry insulation in the Southeast, shares that mentality, and works continuously to inform people about what quality means in the realm of injection foam applications.
“People tend to think foam is foam, and that’s absolutely not true when it comes to injection foam insulation,” said Scott Sander, Tailored Foam’s co-owner. “People don’t understand the differences between them, and that’s what we want to educate them about.”
For injection foam applications, Tailored Foam installs one product: Core-Fill 500, which is manufactured by Tailored Chemical Products, Inc. Core-Fill 500 is a two-component amino-plast foam, with each component being manufactured and shipped in a liquid state. That contrasts with competing injection foams, in which the resin component is manufactured and shipped as a powder. These “dry-mix” foams are commonly used for masonry insulation applications, but offer stark differences in not only production, but installation and performance as well.
“There’s so much difference between a foam that is made by a quality company like Tailored Chemical, versus a dry-mix foam where there is questionable quality control,” said Sander.
As the video below details, the resin component of Core-Fill 500 is formulated in liquid form in a controlled facility and then shipped by tanker to the location of one of Tailored Chemical’s certified installers, like Tailored Foam, where it is stored in large tanks until needed for installation. Core-Fill 500 has been tested for quality by Underwriters Laboratories, and is subject to ongoing auditing to remain UL-listed. The manufacturing process for dry-mix foams, according to Sander, isn’t as transparent. The basic process involves the resin component being manufactured as a liquid, dehydrated into a solid state, crushed into powder, and shipped in large bags.
“We know the importers of dry-mix foams,” explained Sander. “What we don’t know is who manufactures them and where they are imported from.”
Manufacturing questions aside, dry-mix foam presents additional issues when it comes to installation, as the resin powder must be rehydrated and left to dilute before being installed. The dehydration and rehydration processes present a number of variables that can be detrimental to the quality of the final product. The video also highlights these potential issues, which include processing problems, poor water quality, and inconsistent mixing.
“As you see in that video, you can see Tailored Chemical and how meticulous they are in making the foam, and all of the quality checks they have, versus something that’s in a bag and is mixed by a laborer with a paddle on-site,” said Sander.
According to dry-mix specifications, the foam must be injected into dry walls, and the walls have to be protected from rain for 24 hours.
“How is that feasible in a wet climate like Florida?” Sander asked.
The pre-installation mixing issues can and do result in foam that does not meet its purported characteristics, and often shrivels within masonry cavities, thereby negating any potential thermal and acoustic benefits.
Despite the inherent risks with mixing and installing dry-mix foam, the product is widely installed throughout the U.S., which touches on Sander’s earlier point about thinking one foam is just like another. Seeking differentiation, Tailored Foam is an inherent advocate for Core-Fill 500, but the decision to install a particular foam product ultimately rests in the specifier of a given project.
“It’s purely up the architect, or the person building the retail chain or home,” Sander explained. “We’d like to see people write a little bit tighter of a spec, and some people won’t allow products like that, but 9 out of 10 do right now, which is pretty frustrating. Architects need to read the dry mix specifications.”
It might seem like an uphill battle for Tailored Foam, as much of the challenge with regard to specifications is tied to the lower cost of dry-mix foam, but Sander invokes the notion that you get what you pay for.
“Yeah, we’re a little more expensive, but in the long run it’s definitely worth it,” he said. “Our company’s philosophy is that we offer the best products that are out there…we feel like that’s what we want to offer our customers.”
About Tailored Foam of Florida, Inc.: Tailored Foam of Florida, Inc. has been providing foam insulation services since 1986 and is the largest installer of foam masonry insulation in the Southeast. Our Total Solution foam insulation products are used in homes, schools, hospitals, movie theaters, retail shops, and various other types of masonry or pre-cast buildings, throughout Florida and Southeast Georgia. For more information, please use the contact details provided below.
Disqus website name not provided.