Houston Bros. Spray Foam Insulation Caps Off 'Green' Home with SPF Roof
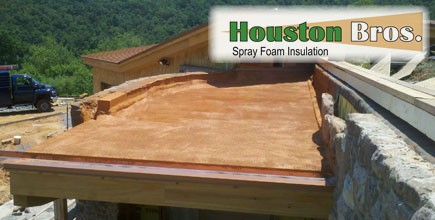
STUART, VA–July 20, 2012–With much of its roof covered in grass and able to be trimmed with a lawn mower, a new residential construction in Virginia may have raised the bar on "green" building. Capping off the unique structure was a spray foam roofing system applied by Houston Bros. Spray Foam Insulation.
It's safe to say a thoroughly Green mindset guided the home's construction, from the sustainable building materials, to the structure's power being sourced from a standalone solar array and battery backup. The home is actually built into a hill, with about half of the floor plan essentially being underground. Of the two smaller sections of the roof that weren't sodded, the one that covered the entryway was intrinsically difficult to address.
"It was more of a detail project than anything else," said Dan Houston, owner of Houston Bros. "Spray foam was good for this particular situation."
While the entryway roof is only 300 square feet, its shape and location made it difficult to address will more typical means of roofing. Especially formidable was intricate rock detail on what formed the back wall and front lip of the entryway roof. When combined with the roof section's irregular shape, an application of spray foam was deemed to be the optimal roofing solution by the homeowners.
"It was ideal for using foam, because you could spray right along the curve of the rock wall," said Houston. "It would be hard to do it with other types of roofing systems."
Not only did the substrate present complications, but the busy construction environment posed a few problems as well. First and foremost, overspray protection was critical to keeping stray bits of foam from attaching to the stonework, woodwork, and the numerous vehicles that were parked at the job site on a daily basis. Houston Bros. also had to coordinate with the other contractors as to keeping clear of the entryway's vicinity during spray days. Suffice to say, this minor roof section required major effort.
"If you were a new guy, and were training on how to spray foam, you wouldn't want to do it on this job," said Houston.
The substrate consisted of a water and ice barrier that was battened down to the roof section's plywood surface. Two inches of Lapolla Foam-Lok 2.8 lb. roofing foam was sprayed directly to the underlayment, although the depth was tapered down as it met the roof section's hidden gutter. Then, two coats of Uniflex acrylic roof coating were applied to the foam, with the top coat being broadcast with granules. Finally, the entire area was coated with Sherman Williams paint to color-match the other un-sodded roof section.
Houston Bros. completed the project in three days, much to the satisfaction of all parties involved.
About Houston Bros. Spray Foam Insulation: The Houston Bros. roofing team has over 10 years roofing experience and can provide you the repairs and coatings that you need and a warranty to back it up. for more information, please use the contact details and links provided below.
Disqus website name not provided.