Hallelujah! Hallelujah! Hallelujah!
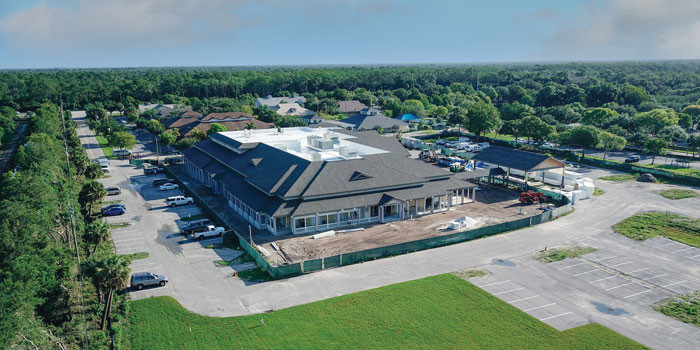
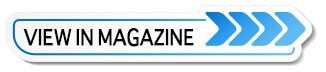
Spray Foam Magazine – Winter 2020 – Ed Richards is a spray foam expert who has been in the business for thirty years. His company, Leed Insulation, is based in sunny Fort Pierce on the southeast coast of Florida, and it’s there where he received a call from Webb Builders, a family-owned construction business based in nearby Jupiter. They wanted Ed and his crew to come and spray a new church construction to seal the building’s envelope.
Geared up in their full-face fresh air masks and fresh air pumps, the crew headed to Calvary Church with their Graco E-30 and H25. The new construction was an impressive 46,262 sq. ft., so this project required a couple of crews with staggered spray times, to fit around the builder’s schedule.
The original Calvary Church was built 23 years ago in 1997 and they needed to build a new church due to growth in their congregation. “The number of people attending has tripled over the last few years, so we were running out of space.” Stated TJ Eve, the Executive Pastor at Calvary.
The architect specified foam for its efficiency, superior air sealing, thermal performance, and better air-quality. He instructed the foam be applied to the underside of the roof deck (R38) spraying 10 inches, knee walls and gables (R20) at 5.25 inches, porches/entry ways (R13) at 3.25 inches and the exterior walls at 1.5 inches.
Originally the architect and builder had specified another spray foam brand, but Leed Insulation suggested using SES SucraSeal, open-cell foam for its advanced technology to pass the ICC ES AC377 Appendix X Fire Test without an ignition barrier. Ed explained, “In our opinion, this is a superior product and once we showed the benefits to the builder and the architect, they were very happy to change the product.” There was no specific surface prep required since it was a new construction project and there was also minimal protection needed. The substrate to which the foam was applied was a metal roof deck and concrete block construction.
The roof deck was 27,167 sq. ft. of air-conditioned space and 4.323 sq ft. of exterior porch area. The architect insisted spraying open-cell foam on the exterior walls at a measurement of 1.5 inches into 1.625-inch metal studs. This posed a challenge since open-cell spray foam is normally sprayed at a minimum of 3 inches. “We decided that a ‘000’ mix chamber was the way to go. It was a challenge as open-cell likes to be sprayed thicker,” Ed stressed.
CFI CoreFoam was then injected into 7,952 sq. ft of the exterior CBS walls and the open-cell spray foam applied to the interior surface of the exterior CBS walls with IFTI’s DC315 Thermal Barrier covering the open-cell spray foam above the drywall. The architect also required that the interior walls have fiberglass batt installed for sound attenuation.
The architect and building official had told the builders they needed a spray thermal barrier over the entire project, and Ed explained to them this was not the case. Just certain areas in the roof and exterior walls would need fire retardant paint. Ed was able to reduce the thermal barrier required by over 50 percent by educating the contractor, building official, and the architect of the code requirements for thermal barrier. Ed proudly states, “We were able to trim roughly $25,000 of the project because we were able to clarify to the building department that a large majority of the job did not need a thermal barrier. There was a total of 18 mils wet / 12 mils dry thermal barrier sprayed.”
The job was supposed to be a two to three-week project, and according to Ed, “The roof deck took about a week, but between the interior batts and everything else it took longer. Due to the contractor scheduling, the job was split into sections, and the crew was active on and off of the project from the beginning of February to mid-June. We started by spraying the underside of the roof deck; then they had us come out to do the batt work and spray the exterior walls, piece by piece, area by area. The injection foam was completed in about two days and the roof deck spray foam was mostly completed in about a week.” The challenge for the crew was coordinating their schedules with the builder’s timing, but they are professionals who like to see their clients happy, so they made it work.
The crew used 17.5 sets of SucraSeal, but some of the yield was lost due to spraying the foam on the exterior walls so thin. Between the spray foam, injection foam, and fiberglass batt work, approximately 10 different employees worked on this project.
“All the people at Webb Builders were a pleasure to work with. I believe the owners have constructed a well-insulated building and they will be very pleased when they see their energy bills when compared to other buildings of comparable size,” said Ed. Due to convincing the architect about the benefits of SucraSeal, they managed to save a lot of money on the thermal efficient building making everyone’s prayers come true.
Dan Plourde, Lead Pastor at Calvary eloquently concluded, “We believe in being good stewards of what God has blessed us with and that includes our facilities. Having an energy efficient building, especially in the Florida summers, allows us to save money and energy to put towards our community.”
Disqus website name not provided.