Foam Roofing Project in Iraq Keeps Communications Center Cool
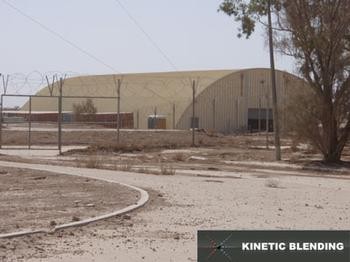
The use of spray foam roofing and insulation in Iraq and Afghanistan is increasing. We have seen reports on tents being sprayed with foam for better comfort and more efficient energy consumption. The use of foam insulation is also making significant reductions in fuel consumption, fuel that must be trucked in on dangerous roads.
We report on a project that was performed this summer at Al Asad Airbase, east of Bagdad. Al Asad Airfield, the second largest airbase in Iraq, is located in northern Iraq approximately 180 kilometers West of Baghdad and 12 kilometers Southwest of the Euphrates River.
The building to be insulated is a highly secure communications center that has heat producing equipment operating inside. It also had an inadequate interior blown-on cellulose insulation that was falling from the ceiling.
The military is putting projects such as this up for bid to local business in an attempt to bolster the economy and develop business infrastructure in Iraq. The initial successful bid came from a company in Bagdad that was not able to acquire the material or equipment for the job. When the job came back up for bid again, Sama Al Andalos, an Iraqi owned company with on-base facilities won the project. While they had no previous experience with spray foam, they did have a connection with Regional Projects Group (RPG) in Kuwait City.
Robert Chalede of RPG had acquired and designed a spray trailer for an H-20/35Pro machine that was used on a polyurea interior wall blast mitigation project a couple of years ago in Kuwait. Unfortunately the machine was not cleaned and put away properly (purged) after the earlier project and it lost its A-side isocyanate hoses to hardening.
Steve Chandler, from Kinetic Blending, was called to Kuwait to diagnose and “make-ready” the equipment prior to its shipment to Iraq. Steve tells us that he had actually been there for during the initial set-up of the proportioner and the application of polyurea back in Kuwait, an interesting connection from former project to a new one, so far away from home.
Once Chandler got the machine to function again, they outfitted it with a “D-lite” Spray Gun manufactured by Chandler’s company Kinetic Blending. The foam they applied was from a local blender in Kuwait City that also manufacturers foam core steel panels named Kuwait Polyurethane Industries.
Test spraying the machine helped us to purge out all the old polyurea in the system and verify the performance and reliability of the H-20/35 system. The trailer was then loaded on a flatbed, along with 8 sets of 2.7lb density foam and a pallet of acrylic coating. From here, an Egyptian truck driver drove the trailer to Ali Al Salam air base to connect with a northbound convoy.
Chandler returned home while the equipment made its journey to Iraq. During the time home, Chandler acquired an economical and “noticeably easier to handle,” 150 ft. high pressure heated hose system from Eric Benson of Spray Foam Equipment & Mfg. in Louisiana. He arranged for it to be shipped to Iraq for the job.
When the trailer was about to arrive on at Al Asad, Chandler returned to Kuwait to catch a military flight north. “I waited on base in a tent city for 5 days before there was available space on a C-130,” Chandler tells us. “It was hot and I would have whined, but there were too many of our troops putting up with it just fine,” he adds. Upon his arrival he found out that there would be an armed guard with all the six (6) workers at all times. “We chose to work a 12 hour shift at night as it was over 115F during the day,” claims Chandler.
Also because of the intense heat, some off-gassing of the blowing agent in the B-side drums caused heavy swelling of the drums during shipment but they all held; and with 4 or 5 bags of ice on top of the drums, they brought the temperature and the pressure down enough to open and use the material. It was fresh and had good performance characteristics during the roof application.
This was a Quonset style steel building that was sprayed with two (2) inches of foam over the top and on the ends. The A-side of our system was then purged with DOP to ready it for an easy set up on the machine’s next project. They used six (6) sets of foam, and while Chandler tells us he has sprayed that much foam in a lot less time – the project went well. “We could have used more time to touch up our coating application, but the security guards were needed for other duty. There were no on the job injuries, which is always an important part of any project.”
Thanks to Steve Chandler of Kinetic Blending for his contributions for this article.
Disqus website name not provided.