Designing Around SPFA Recommendations
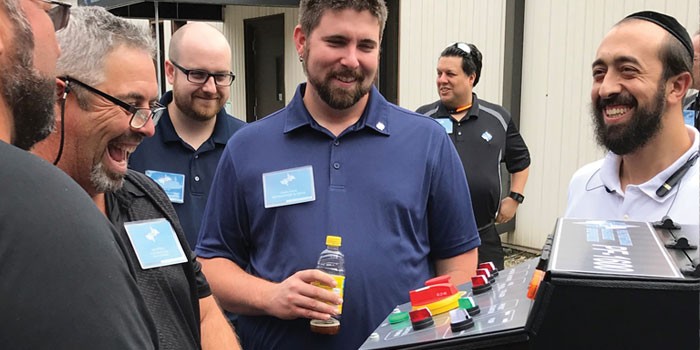
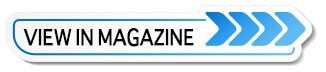
Spray-applied polyurethane foam insulation (SPF) has become the material of choice when it comes to building envelope technology and insulation efficiency. Dramatic growth has been seen in the USA residential insulation market. According to the United States Census Bureau, single-family unit starts went up 18.7 percent from 2015 to 2017, going from 715,000 to 849,000. The first two quarters of 2018 are showing an 8% increase over 2017¹. This means there is business for the adept SPF contractor. Profitability relies on efficiency in three key areas—equipment investment/operation cost, material estimating/cost, and application time including getting on and off the jobsite. It should go without saying that the first piece of the puzzle is a professional team trained in SPF application and safety.
The Spray Polyurethane Foam Alliance (SFPA) states in SFPA-137-General-SPF HP Equipment, “Size your equipment based on the type of projects you expect to undertake.”² They note an output of up to 15 lbs./7kg per minute for residential insulation, light commercial and industrial applications. These specs are reminiscent of the workhorse that started the SPF industry, the FF-1600. Although they have not been produced in many years, these machines are still in operation worldwide. The team at PMC thought: what if we designed a machine based on the needs of today’s residential spray foam industry, with a focus on meeting the SPFA recommendation while employing the absolute minimum operation requirements in our design criteria? With the efficiencies of today’s pneumatic and heating technology we could reduce the air consumption and power consumption to create a new platform that is good for both entry-level and seasoned applicators. The PF-1600 project was initiated.
The design goals of the PF-1600 started with the lowest air and power requirements possible while achieving the material flow and temperature needed for residential foam application. In sprayer’s parlance, we needed to spray at least an -01 chamber all day long. PMC engineers utilized the most current pneumatic motor design and digitally-controlled heating configurations to achieve and surpass this goal. Requiring just 15-20 scfm at 100 psi the maximum hose length is 310 feet.
The footprint was also of importance—at just 24 inches by 24 inches by 32 inches, the PF-1600 does not need much space and is built with smaller rig and truck sizes in mind. This is important domestically and even more so in many of the international markets where PMC supplies equipment. It is mobile and a true production machine, capable of replacing the ‘hot dog carts’ in the industry that require material recirculation for heating and are sold as production machines.
The PF-1600 has four heat options depending on the requirements of the environment—6Kw, 7.5Kw, 9Kw, and 10.5Kw. The high efficiency hybrid heat configuration and hose heat are controlled digitally to maintain optimum temperature control over the chemical system.
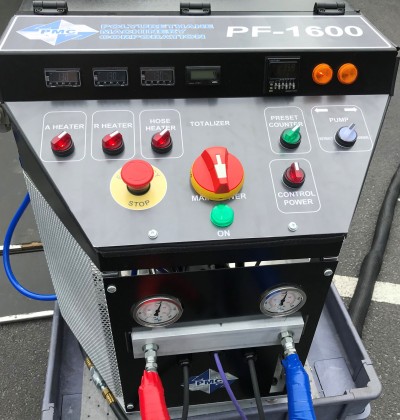
With a footprint of 24 x 24 x 32 inches, the PF-1600 occupies less space – ideal for smaller rigs and trucks.
The growth noted in the residential housing market is just one example of the increase in SPF application. PMC has the philosophy that for an industry to grow, it needs the right tools at the right time. Product development input is end-user focused, and driven by the best available information from industry associations like the SPFA. PMC distributors take part in think tanks and product refinement sessions to configure the final product. At the end of the day it is collaboration between engineers, technicians, distributors, end-users and industry associations that creates PMC products. The new PF-1600 design has met the standards set forth by the industry players, and is ready to take the field in Q1, 2019.
¹ United States Census Bureau https://www.census.gov/construction/nrc/pdf/quarterly_starts_completions.pdf
²Spray Polyurethane Foam Alliance http://www.sprayfoam.org/revised-techdoc-spfa-137-for-spf-high-pressure-equipment-now-available
*Spray Foam Magazine does not take editorial positions on particular issues; individual contributions to the magazine express the opinions of discrete authors unless explicitly labeled or otherwise stated. The inclusion of a particular piece in the magazine does not mean that individual staff members or editors concur with the editorial positions represented therein.
Contact Details
Name: Polyurethane Machinery Corporation (PMC)
Email: Email Us
Phone No: 732-415-4400
Disqus website name not provided.