Case Study: Prime Flex Seals Up Leaky Tunnel That Caused Contamination
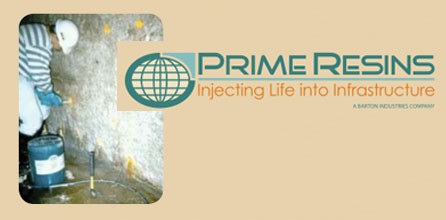
CONYERS, GA - February 27, 2012 - Problem: When the time to complete a repair project is tight, and you encounter an unexpected expansion in the scope of work, you have to be able to react fast. That’s what Don Ford of Concrete Restorations of Charleston, South Carolina found when his company was working at a manufacturing plant near Charleston. The manufacturing company produces industrial carbon products. The twelve-year old tunnel system was constructed of fourteen-inch reinforced, cast-in-place concrete.
The annual television inspection of the tunnels showed they appeared to be in good shape considering the harsh environment and their age. However, a few random cracks were found in the walls, and some floor joints appeared to be failing, allowing water to seep in and collect on the floor. There was also evidence of deterioration on the surface of the concrete floor. Phillips Industrial Services of Mount Pleasant, South Carolina was hired as the general contractor to repair a section of the tunnel that had significant water intrusion. The joint and crack repair work was subcontracted to Concrete Restorations, Inc.
The standing water in the tunnel was tested and found to have absorbed sulfur dioxide from the vented air which formed sulfuric acid. Tests of the floor and portions of the walls also indicated that acid contamination extended as deep as one inch into the concrete. Visual examination also revealed that most of the leaking water was not coming from the cracks and floor joints, but instead through the cold-joint between the floor and walls.
Solution: With this new information, it was obvious that the whole repair strategy would have to change. The owner’s project engineer met with Don Ford from Concrete Restorations, Jim Miller from Phillips Industrial, and Michael Vargo from Prime Resins. They decided that the first priority wold have to be stopping the leaks at the cold joint. Michael Vargo recommended injecting Prime Flex 910 (a hydrophobic polyurethane grout) around the outside of the cold joint so it could form a watertight curtain. He recommended drilling through the wall every eighteen inches near the cold joint, and then injecting the grout through the drilled holes. This would allow the grout to migrate through the surrounding sand and create a seal around the lower portion of the wall to the bottom of the floor slab.
Overnight, the work crews started drilling injection holes through the fourteen-inch thick concrete walls. Samples of the Prime Flex 910 were then injected into containers filled with the hot water to confirm the material would cure properly.
Benefit: Because Phillips Industrial Services and Concrete Restorations were able to react quickly and implement a sound repair on schedule, the facility owner contracted to repair the remainder of the tunnel system in three future phases.
About Prime Resins:
Established in 1982, Prime Resins manufactures polyurethane foams, epoxy injection resins, and polyurea coatings. With in-house R&D labs, formulation, packaging and technical support offered 24/7, Prime Resins has everything customers and partners need to help solve problems. Specified by engineers, injected by specialty contractors, and distributed through building suppliers, Prime Resins products are used primarily to stop leaks, stabilize soils, strengthen and protect concrete. For more information about Prime Resins, please click the link below to visit their website, or call 855 875 7612.
Disqus website name not provided.