Avoiding the Freeze
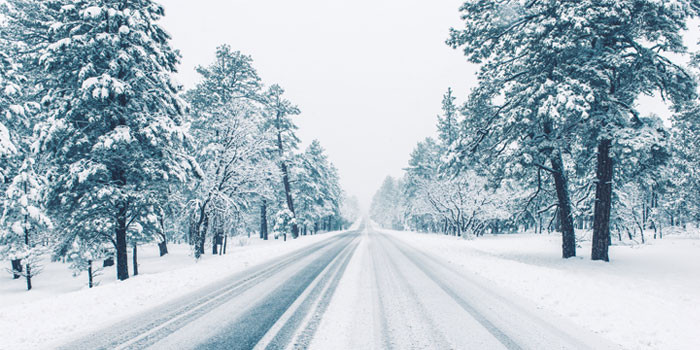
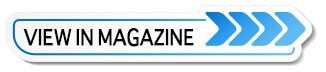
SPRAY FOAM MAGAZINE – WINTER ISSUE 2019 – All spray foam guns are basically the same and as big hunks of metal, they lose heat quickly and are generally cold in cold weather.
O-rings get brittle, lubricating oil and grease become thick like cold honey or cement, and gun grease hardens. These components are all used to lubricate and protect movable parts within the spray gun, so if they get cold and stiffen, they may fail. If you pull the trigger under these conditions and failure occurs, you may end up with a cross-over (total foam blockage in the head of the gun). This is an expensive setback when you factor in parts, labor, and time.
The simplest solution to combat that from happening is to keep your equipment warm during the cold weather. If you don’t have a heated rig, travel with the foam gun in the cab of the truck next to the heater.
You might also encounter trouble with ISO when it is cold outside. Like any liquid, when ISO gets cold, it gets thicker. This might not happen as quickly as it does with the resin, but it does get thicker and it can “freeze.” As ISO approaches freezing, the molecules actually get really close together and can attach to each other, resulting in dimers, also called crystals. Around freezing, it will not solidify like an ice cube, but will be more like a Slurpee. And these crystals can ruin the ISO material and damage your equipment. If you use this material, you could plug up and clog your entire system from the drum to the gun. This too can be an expensive setback—equipment, time and lost revenue.
In some cases, you can save the material by straining the crystals. To do this, you need a clean barrel and an extra-extra-large pair of panty hose—that’s right, panty hose—
to use as a strainer. They need to be large enough to stretch over the top of a drum. Once you have them in place, you have to transfer the liquid by hand, pouring it over the panty hose, to drain the liquid into the new drum. In this instance, you can’t use a pump because of the crystals, so it can take a while.
Once again, your solution is to be proactive and prevent an unwanted situation by keeping your chemical warm during cold weather and do not let it get close to freezing.
Now the resin is a little different. It will generally be more affected by cold weather than ISO—it will get thicker, faster as the material gets colder, like honey. Additionally, the resin for water-blown foam can freeze into a solid mass due to the water content. The good news, at least with most water-blown foam, is you can typically thaw out the material and use it, but check with the manufacturer to confirm this.
However, in good practice, it is important to maintain the resin temperature for optimum performance. Drum blankets are very effective. Band heaters can also work if they are thermostatically controlled and placed at the very bottom of the drum. Something to remember when using a band heater is if it goes wild and overheats, it can blister the drum liner and this debris can break off into the resin, showing up in the screen filters or getting caught somewhere in the spray hose. So be mindful of that.
Your solution is to keep your chemical warm during cold weather.
Hopefully by now you are noticing a common theme—protect your stuff and keep it warm during cold weather and you will be better off in the long run.
Disqus website name not provided.