A Breath of Fresh Air
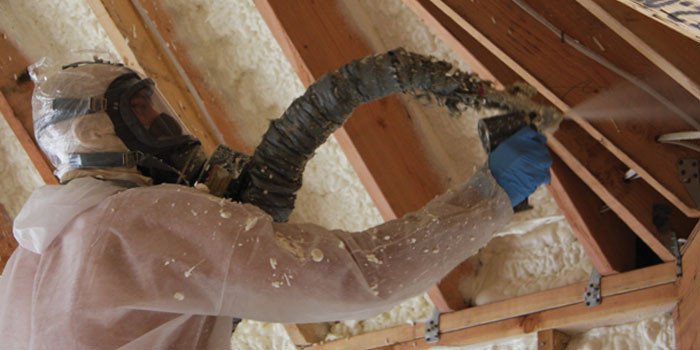
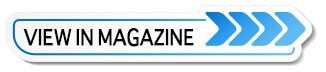
SPRING 2019 – Temperatures can rise to 200 degrees in attics and crawl spaces in the peak of summer. This created quite a challenge for folks like Michael Asbra, owner of a spray polyurethane foam (SPF) insulation company, with installing SPF in these spaces during the summer season. Even his most diligent installers struggled from the heat with the personal protective gear (PPE) required on the job.
In an effort to prevent heatstroke and exhaustion and as an overall safety precaution, Asbra often had to shut down his business, which meant potentially failing to meet customer deadlines.
Having listened to his installers concerns and witnessed their struggle, Asbra began thinking of a solution. To rescue his business in the summer months, he began toying with a “cool” idea he had to increase productivity and, at the same time, enhance employee safety. To his credit, after a few years of trial and error, he invented a device that not only breathed new life into his spray foam installation business, but cool air to his installers while they worked.
Air respirator systems, like the one Asbra developed, are now staples on job sites where spray foam insulation is used to construct energy-efficient buildings.
Insulation of Choice
SPF is an environmentally friendly product and is often credited with reducing heating and cooling costs in half. However, it is critical to avoid inhalation of, and skin and eye contact with, SPF chemicals. As with any chemicals, proper application is essential for safe working conditions.
When not protected properly during the foam installation process, installers are at risk to isocyanates on their skin and in the air that they breathe.
Federal law requires employers to ensure that their employees are both protected from exposure to hazardous materials and can breathe good, clean air. While workers are required to wear protective gear, maintaining a proper ventilation system to control and eliminate isocyanate levels throughout the installation process is essential for reducing health risks.
The most important piece of protective equipment, perhaps, is a respirator. Spray foam installers wear respirators to remove contaminants from the air where confined quarters, low oxygen levels and elevated temperatures make work difficult and dangerous. Various respiratory devices including headgear, breathing tubes and air sources, each with their own unique practicalities, are available to ensure their protection.
Powered Air-Purifying Respirator
A powered air-purifying respirator (PAPR) will protect workers against contaminated airborne microorganisms, fumes, vapors, and gases. PAPRs consist of both a purifying and supply component. The purifying respirator—typically in the form of a hood or full face-mask—transfers the contaminated air through a filtering agent, which, after removing a sufficient portion of the hazardous material, will deliver fresh, cooler air through an alternate supply respirator. This protective piece is best-suited for outdoor use.
Supplied-Air Respirator
For indoor purposes, a supplied-air respirator (SAR)—in the form of a tight-fitting half or full face-mask, or loose-fitting helmet assembly—funnels fresh air through a hose attached to a remote source, such as a compressor or low-pressure pump. When used properly, SARs can provide installers with the greatest protection. There are limitations on how long a hose can stretch without losing enough pressure to prevent an adequate flow of air from reaching the applicator. However, SARs offer an almost unlimited supply of air at the work site.
Not To Be Taken Lightly
Serena Asbra, founder and CEO of Tennessee Chill Box, the company that distributes Michael Asbra’s air respirator system, said that despite the advent of ‘green technologies’ and greater awareness about their risks, gas, vapors and excessive volumes of compressed air or CO2 remain a threat to the health of polyurethane foam installers. She said supplied-air respiratory systems that dispense non-compressed “Grade D” breathable air into personal protective equipment meet federal guidelines and offer the best comfort and protection as well.
Poor air quality is not to be taken lightly; especially when continued exposure can exacerbate preexisting conditions like asthma or lead to cancer, respiratory and heart disease in the long-term.
The good news is SPF contractors don’t have to sweat the next installation project. When respiratory systems can be counted on to protect from isocyanates and supply clean, quality air, both employer and installer can concentrate on the job—and breathe easier!
Disqus website name not provided.