Tech Tips for Winter SPF Applications
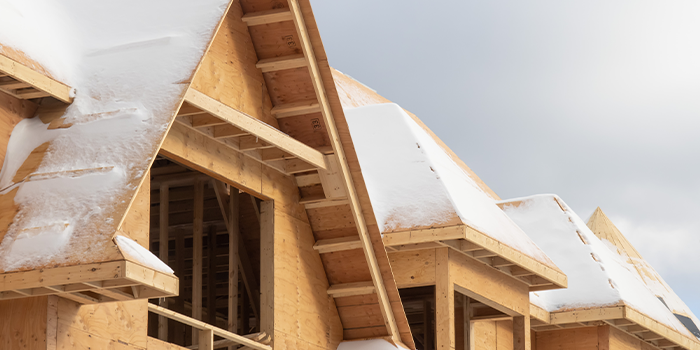
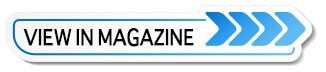
SPRAY FOAM MAGAZINE – As we transition from Fall to Winter, many people think of the leaves changing color and the fast-approaching holiday season. For those on the front lines of our industry, they think about the challenges that cold weather brings with preparing and applying spray foam insulation – keeping drums stored at required temperatures, managing substrate temperatures, adjusting processing parameters, maximizing yields, and even keeping your body warm.
This is the time of year when applying spray foam is most difficult, especially in the northern U.S. and Canada. However, with some small but important changes to your preparation, you can navigate the cold temperature season and avoid making a costly mistake. Here are the best tech tips to help promote success spraying during the cold weather season and the key theme here is “being proactive.”
- Be well versed in the Application Guide instructions for the spray foam insulation you’re installing. You’ll need to proactively store the product according to the manufacturer’s Application Guide. Typically, this requires storing the spray foam drums in the needed temperature range 24-48 hours in advance of installation to help avoid costly performance issues when applying the foam.
- Substrate temperatures must be above freezing. Freezing substrates can cause slower spray foam reaction times, which can lead to adhesion and yield issues. For this reason, it’s imperative to follow the Application Guide instructions around substrate temperatures. You’ll need to warm the substrate and spray environment with dry element heaters, which will assist in the reaction of the foam. We also recommend positioning one heater behind the sprayer where foam is curing and one ahead where foam will soon be applied to ensure that substrate is prepared for fast, continuous application.
- Seal off the spray environment with plastic to prevent direct, cold wind from impacting spray foam application. Cold winds could cause overspray or inconsistent application as well as challenges with maintaining the needed substrate temperature for the best results.
- Follow the Application Guide’s instructions for proper depths to be sprayed on the primary pass. For closed-cell spray foam, when a secondary pass is necessary, scan the surface of the foam using an infrared thermometer to ensure the primary pass temperatures are less than 110°F before applying a second pass. Open cell spray foams do not require a cool down period before applying a second pass as they release heat quicker than closed-cell foam.
- Make sure ambient temperatures are 5°F above dew point before installing SPF. Installers should use a psychrometer to measure the dew point relative to the ambient temperature. Please note, if the ambient temperature is within 5°F of the dew point, excess moisture can build on the substrate causing adhesion issues and potentially off-ratio application of the foam as it reacts with the moisture on the surface. Be sure to closely monitor this to help avoid material waste and having to rework portions of the installation.
- Prepare your drums to the Application Guide’s recommended spray temperature as according to which “B” side or Resin you are about to spray. The most common settings are over 70°F for closed-cell spray foam and 90°F for open-cell spray foam, but always refer to the Application Guide in case it differs for the spray foam product you’re installing.
- Dial in the spray temperatures and pressure with the goal of a ‘liquid-to-cream’ time of one second for your test spray. Also, make sure your spray pattern is round and has a fine mist. Odd, shaped spray patterns (with larger droplets instead of mist) could be caused by a dirty spray gun tip, the installer could be spraying at too low of a pressure, or the material could still be too cold.
Following these steps will help you better navigate the challenges of installing spray foam during the cold temperature season. Remember, “being proactive” with upfront preparation is essential to prevent wasted time and spray foam material while maximizing yields and profits.
Contact Gaco SprayFoam | SES If you have any questions about any of Gaco SprayFoam | SES’s products or services: 713-239-0252 // gaco.com | sesfoam.com
*Spray Foam Magazine does not take editorial positions on particular issues; individual contributions to the magazine express the opinions of discrete authors unless explicitly labeled or otherwise stated. The inclusion of a particular piece in the magazine does not mean that individual staff members or editors concur with the editorial positions represented therein.
For use by SprayFoamMagazine.com & Spray Foam Magazine
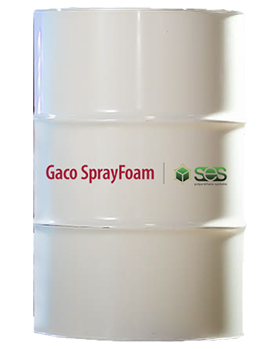
Disqus website name not provided.