Spray Polyurethane Foam Makes Connecticut Apartment Building Roofs Cooler
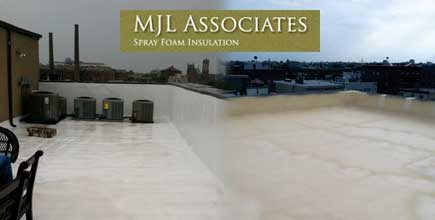
HARTFORD, CT - July 10, 2013 - Apartment building residents have high demands for comfortable living that is conducive to the amount of rent they pay. As such, building owners tend to be mindful of their properties being in the best shape possible to maintain a harmonious environment with tenants. A Connecticut apartment management company faced an interruption of that harmony when it realized the roofs of two properties were leaking. To add insult to injury, the roll-on black rubber roof systems that were failing and causing the leaks had just been installed a few months before. Routine weekly patches which not only proved costly, but also offered a merely temporary solution before the roof system started leaking again. The owner company brought in MJL Associates Spray Foam Insulation (MLJ), which offered a cost-effective, long-term solution via spray foam application.
"A spray foam roof is a three-in-one product," MLJ owner Michael Lieto said, "It waterproofs, insulates, and it gives the building structural rigidity for a much lower cost than a complete replacement of the roof system."
The project involved the installation of SPF in two separate and equally damaged building roofs that the company owned. They were worked on individually within a few weeks of one another, according to Lieto, each application only taking three days to complete.
"The three-day process for a SPF roof application involves cleaning the roof the first day and then waiting for it to dry off; applying the foam on the second; and covering it with the coating on the third," Lieto said.
Before the job started, the MLJ crew decided that they would leave the existing roll-on roofs intact and apply the foam right over them. The SPF would act as a sealant for the systems in place, which would repair the fractures and bolster the rooflines from further damage.
On the first day of each application, the crew powerwashed the substrate to clear it off from grit and dirt remnants. The A/C units were taken out during the project and would not be reinstalled until MLJ had finished the job. They applied a primer made by Lapolla on the substrate and then waited for the surface to dry so it could be ready for the SPF application the following day.
The crew outfitted themselves with fresh-air respirators and jumpsuits on the second day. Using a Graco Fusion air-purge spray gun, the crew applied 1.5 inches of Foam-LOK 3.0, a 3 lb. spray polyurethane foam made by Lapolla, on the flat surface and parapet walls. To mitigate overspray, the top of the parapets and the drain systems were masked off. The crew also used a custom-made spray tent around the spray gun while the applications progressed, which promoted further protection against overspray damage. The total spray area for the first building's roof application was 2,500 sq. ft., contrasted by a much larger application of 10,000 sq. ft. for the second building.
The third day entailed the final step of Lieto's three-day process: the coating. The crew applied two roll-on coats of white Lapolla's Roof Restoration Coating. The coating gave the rooflines a protective and aesthetically pleasing surface.
The crew had one rig equipped with a Graco Reactor E-30 proportioner parked on the side of each building during its application. Lieto explained that the hoses were run from the side of the buildings and not through the buildings, which avoided foot traffic and made the projects run smoothly.
Leito revealed that the applications not only fixed the roofs' leaking problems, it also made the roofs a lot cooler because the SPF and coating reflected off the radiant heat. He said that before the project took place, the temperature on the roofs was 130ºF to 150ºF, on average. After the coating was applied, the temperature on each roof dropped to almost 70ºF.
"It was an incredible difference," Lieto said. "You could take off your shoes or sandals and walk around there barefoot in the middle of the summer."
In addition to the temperature drop, Lieto also noted that the cool-roof application rendered the roof more comfortable for residents. Tenants from both buildings brought chairs, plastic tables, and even barbecue pits for party hosting on the rooftops.
"The finished product was great for both buildings because people could actually utilize their roof system since it was nice and cool," Lieto said.
In light of the improvements resulting from the applications, MJL's client was ecstatic. Lieto mentioned that the management company wished that SPF was brought to its attention before spending so much money on constant and inefficient maintenance on both of their apartment buildings.
"Spray foam is the best system for a client seeking out alternatives from traditional roof systems," Lieto said. "It's a durable system that doesn't give you problems for 15-20 years, if ever. It's cost-effective and it gives a building proper insulation, which in turn makes the building energy-efficient."
About MJL Associates: MJL Associates provides their clients with the latest in Spray Foam Technology. Servicing the Connecticut and New York areas since 2010,. MJL's professional work is represented in their clean craftsmanship, providing a quality product and ensuring that insulation needs are met. MJL believes in the highest levels of Customer Service, the most important value in the creation of any long term working relationship.
Disqus website name not provided.