Pennsylvania Net-Zero Home Designed Using Spray Foam
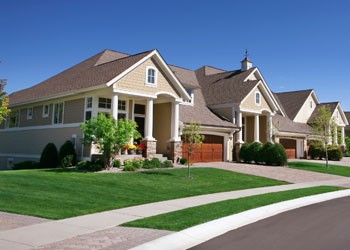
Throughout the U.S., there are building certifications given to structures that meet certain environmental guidelines. This protocol is based on metrics that tie into a structure's greenhouse gas emissions and its ability to prevent energy loss, among other criteria. In Pennsylvania, a near-zero energy lab home was recently built that will serve as an example for homebuilders looking to construct a home that is environmentally sound as possible.
S&A Homes partnered with Integrated Building and Construction Solutions to construct the facility. According to company executives, the home will serve as a prototype by which other homeowners will be able to lower their energy bills. The company plans to test various systems on the four-bedroom, 2,727-square-foot home over the next few years to determine how they would impact a home's carbon footprint.
The home's construction adhered to the toughest environmental standards and is nearly 70 percent more efficient than an average home. Its boosted efficiency results from its ground source heat pump, innovative systems and its insulation. According to Kevin Brozyna, the home's project manager, spray foam was used during construction to ensure hot and cold air do not escape from the home.
Moreover, spray foam was used in the home's band joists as well as on the foundation in the basement to prevent water from leaking in and out of the house; it was also employed to fill in penetrations in the interior and exterior of the building through which air could potentially escape.
"S&A has been dedicated to innovations over the last 20 years, and the Lab Home is simply the next step in the evolution towards achieving the ultimate in energy efficient homes," said S&A Homes vice president of sales Chris Schoonmaker. "We also understand that no matter how much a homebuyer wants to save on energy bills or help the environment, homes must be affordable, stylish and in the right location."
The home was designed with the average consumer in mind and according to Schoonmaker, during construction materials that were chosen provide large cost savings and require low initial costs. Though it's more expensive than cheap solutions like drywall, spray foam provides greater medium- and long-term cost savings by lowering utility bills and making retrofits unnecessary as it lasts far longer than traditional insulation tools.
Disqus website name not provided.