Niagara Foams
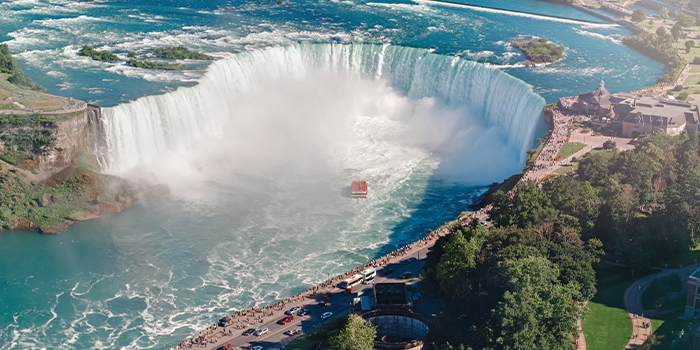
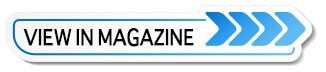
SPRAY FOAM MAGAZINE – The Niagara Parks Power Station sits about half a mile away from Horseshoe Falls on the Canadian side of the Niagara. For over a century, the former power plant harnessed the sheer force of the Falls to provide hydropower to thousands of people in the surrounding Ontario locales. Though it is no longer in use as a power station, the Niagara Parks Commission has worked hard to preserve the building’s legacy by converting it into a museum and educational attraction where visitors can experience a notable part of Ontario history. Redeveloping the historical building required the expertise of several construction firms. Hamilton, Ontario’s Ecotech Insulation Solutions was among participants enlisted by the Niagara Parks Commission to apply closed-cell spray foam to the building’s interior roof decking as a means of providing insulation and proactively preventing moisture.
The Niagara Parks Power Station operated as a hydropower facility from 1905 to 2006, formerly named the Canadian Niagara Power Generating Station. It was the first hydropower station of its kind in Canada, so when the Niagara Parks Commission acquired the building in 2009, they carefully considered the historic building’s future. For a decade, the building sat dormant, caught in limbo – it no longer served its original purpose as a power generation facility, yet it was not open to the public nor used for anything else. Its fate seemed uncertain until 2019, when the Commission revealed exciting plans to revamp the power station as a museum open for visitor tours and for hosting private events, such as weddings and meetings.
Despite being over a hundred years old and having been out of commission for a decade, the building’s interior and exterior alike were relatively well-maintained by the Niagara Parks Commission. Though the building was in acceptable condition, it still needed several renovations and upgrades before it could be deemed acceptable to open to the public. For example, the building lacked suitable insulation by modern standards.

The large building’s stone facade and steel interior might have served its former utilitarian purpose as a power generating station, but without insulation upgrades, it would not be fit to be an open-year-round tourist destination, especially during the freezing Ontario winters.
In early 2021, the Niagara Parks Commission contacted Paul Hobeck, the owner of nearby Hamilton, Ontario’s Ecotech Insulation Solutions. Hobeck had been running Ecotech’s operations for 15 years and had a sizable roster of about 30 experienced employees with many diverse projects under their belt. One of his repeat customers, Merit Contractors, referred Ecotech to the Niagara Parks Commission for spray foam insulation work at the power plant. Ecotech’s stellar reputation and Hobeck’s extensive experience proved the company was a good fit for the job. Hobeck and his team visited the power plant multiple times to assess the scope of the job and coordinate the best course of action.
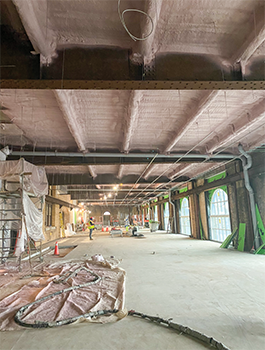
They determined that the building’s close proximity to Niagara Falls could potentially leave it vulnerable to moisture issues over time. Though moisture had not been a severe problem throughout its life as a power generating station, the Parks Commission and Ecotech decided that an application of 2lb closed-cell spray foam on the interior roof decking would be the best and most proactive course of action.
“They wanted to completely eliminate any chance of moisture developing inside the building.” Hobeck explains.
The Niagara Parks Commission tasked Ecotech with applying spray foam to roughly 16,000 square feet, primarily in the area of the building that would be used for events and social gatherings. The main part of the building that housed turbines and other legacy equipment did not require a spray foam application.
The consultation process involved reviewing the building’s blueprints, completing on-site reviews, presenting an estimate at the initial sales meetings, and working out the project details with the Niagara Parks Commission. Upon finishing the consultation, Hobeck assembled a trusted three-man crew made up of one certified applicator and two laborers to apply the closed-cell spray foam to the steel roofing decking of the Niagara Parks Power Station. The roof decking’s substrate was composed of a corrugated steel system.
Though the building’s roof decking was old, the fluted steel substrate was in good condition, having been pre-cleaned by contractors prior to Ecotech’s arrival. Because the work site was enclosed and located indoors, it did not require any special moisture testing or surface preparation aside from being cleaned to remove dirt and debris. To protect the plant’s interior, the Ecotech crew placed layers of protective plastic around certain areas, a preparation method known as masking.
The Ecotech spray foam trucks parked on the dry watercourse outside the building, as close as possible to one of the building’s entrances nearest to their work area. The Ecotech crew hauled the long hoses inside the power plant to apply the foam. They used scaffolding and a boom lift as needed to apply even layers to the tall sections. The crew applied three passes of Elastochem’s Insulthane Extreme’s 2lb closed-cell spray foam, achieving a layer of five and a quarter inches. The Insulthane Extreme has a density of 2.2 lbs., which gives it a superior thermal resistance with an R-value of R-6.03 per inch. To apply the foam, they used a Graco Reactor 2 E-30 Elite proportioner, with a 350-foot hose attached to a spray gun. While spraying, the crew wore industry-standard PPE, including respirators, gloves, and protective suits.
After the newly-applied spray foam had dried and expanded, the on-site general contractors installed a wood-paneled drop ceiling over top of the foam layer for a finished look. Hobeck describes an interesting aspect of the remodeling process: “They had dammed up the Niagara River during construction, so the part out front where we had parked our trucks actually ended up filled with water again after everything finished.”
At the time of construction, the watercourse in front of the building was completely dry and free of water, allowing vehicles to get as close as possible for convenience. Immediately prior to opening the museum, water was diverted back into the watercourse, creating a river where Ecotech’s trucks had once parked.
When all was said and done, the entire foaming process, from masking to spraying, took Ecotech approximately three weeks from start to finish. The newly-restored Niagara Parks Power Station Museum opened to the public in July 2021, serving its future functionality as a testament to a powerful past.
For use by SprayFoamMagazine,com & Spray Foam Magazine
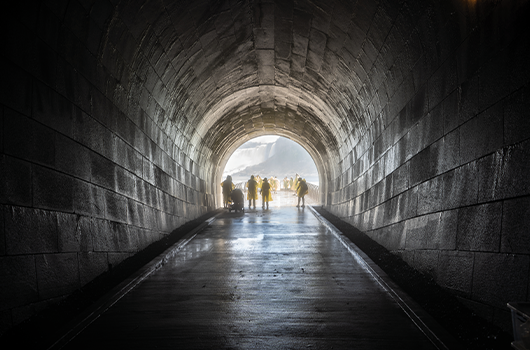
Disqus website name not provided.