Making Waves
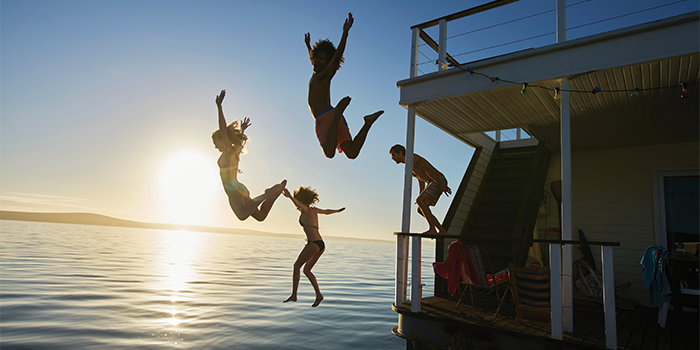
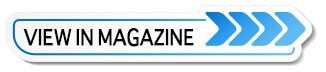
SPRAY FOAM MAGAZINE – Life aboard a houseboat evokes images of endless sun tanning, cold beverages, and floating leisurely from one beach to the next as the captain of one’s own ship. In modern houseboats, there’s endless relaxation potential—with massive, luxurious, custom-built vessels available with all the comforts of an on-land home, such as multiple rooms, stories, solar panels, and interior living quarters impeccably sealed, insulated, and sound-proofed with spray polyurethane foam.
Caymen Crappell and his crew of five from Xtreme Contractors, LLC in Delcambre, Louisiana got the opportunity to apply a combination of open and closed-cell SPF to the walls, roof, and floor of a towering four-story houseboat.
The crew at Xtreme is no stranger to taking on marine-related projects. Based in a town just off Louisiana’s Gulf Coast, they have completed many bulkhead and seawall repair jobs. Caymen’s father, Glenn Crappell, has owned Xtreme for 17 years, while Caymen manages the daily operations and oversees the crew of sprayers.
In late 2023, a mutual acquaintance of Caymen and a shipyard owner referred Xtreme to Breaux Brothers Enterprises. Breaux Brothers in New Iberia specialize in constructing utilitarian vessels built to withstand the unpredictable waters of the Gulf Coast, such as ferries and crew boats. But houseboats and yachts are designed for recreation and comfort, which meant these boats needed to be properly insulated, sealed, and protected from moisture on all sides. Breaux Brothers welcomed Xtreme aboard without hesitation given the company’s decades-long reputation of clean, high-quality work. In the past year, Xtreme has had an uptick in their steady stream of work, including spraying the houseboat at the Breaux Brothers’ New Iberia shop.
Breaux Brothers built the boat from the ground up for a private customer and contracted the Xtreme team to foam the boat for peak onboard comfort.
The houseboat in question is as big as a kraken. It’s 100 feet long and 45 feet wide, rising an impressive four stories and equipped with four bedrooms and four bathrooms. Upon completion, it will also hold solar panels on its topmost deck to provide endless electrical power throughout the boat. “The first floor houses the engine area, the second and third floors are for the living areas, and the fourth floor is for the wheelhouse, with solar panels at the back.” Crappell explains.
Crappell describes why SPF was the best choice: “They decided to use foam because of the structure’s complexity, and to insulate it and give it a great seal, plus dampen sound from people walking on the metal floors.”
Deciding to go with foam over other insulation materials was a no-brainer, though a lot of thought was put into the specific application technique. The Xtreme team utilized a hybrid approach, combining layers of both closed and open-cell foam– closed-cell to seal and protect the boat’s aluminum frame from moisture, and open-cell to provide as much acoustic insulation as possible.
Foaming the boat took approximately three weeks, beginning late December 2023 into mid-January 2024. The Xtreme team suited up in industry standard protective outerwear like coverall suits, gloves, and respirators.
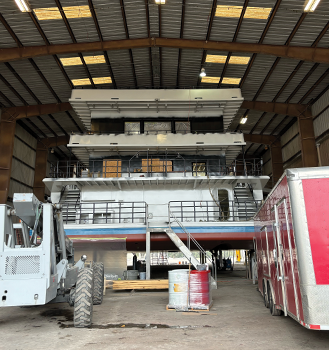
They foamed the entire houseboat interior using a Gusmer GH-2 with a Fusion ProConnect gun. They first applied five inches of high lift SES closed-cell spray foam to the aluminum frame, coating every inch of the boat’s walls, ceiling, and floor. Because the boat was newly built, the substrate was in pristine condition and did not require additional cleaning or surface preparation.
After applying the closed-cell layer, they moved onto the second phase in the hybrid technique– applying open-cell foam. The sprayers applied six inches of high lift SES open-cell on top of the existing five inches of closed-cell, bringing the foam layers to a total of about 11 inches. Because open-cell foam rapidly expands after applying, they used a-spray-and-shave technique, shaving the excess foam down flat to guarantee a smooth, even layer that could easily be covered with plywood wall material.
Crappell details why a hybrid foam application worked best for the houseboat project, rather than choosing one type over the other: “Closed-cell works best as a moisture barrier and doesn’t let any water through. Open-cell is softer, and works great for sound dampening. Each one has advantages and doubling them up is the best of both worlds.”
The foaming process remained on an even keel apart from some minor weather and temperature-related challenges. The Breaux Brothers shop where they worked was covered and enclosed on almost all sides, but the shop door was left open for ventilation and ease of access. It was winter at the time of foaming and while Louisiana doesn’t get too chilly, sometimes the aluminum would get a bit too cold and needed warming before applying the foam to ensure it adhered correctly without pulling away from the substrate. Fortunately, the cold didn’t slow down the process too much. The sprayers either warmed up the area before foaming or waited to begin until outdoor temperatures rose before getting started, ensuring smooth sailing from start to finish.
For use by SprayFoamMagazine.com & Spray Foam Magazine
Disqus website name not provided.