Emergency Beneath the Hospital
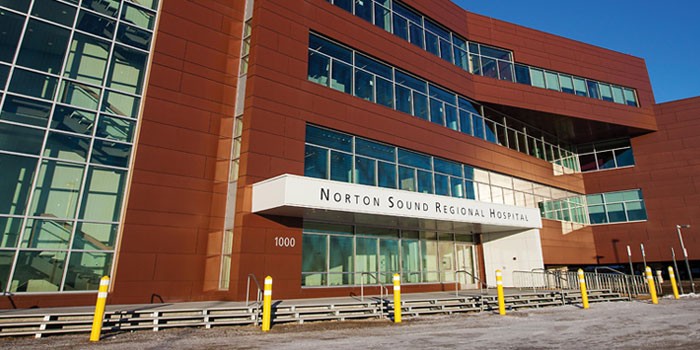
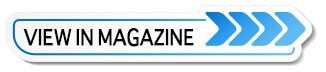
Polyseal Insulation have a reputation for quality, energy efficiency, and problem-solving, which were all useful for one slightly, unusual job. Norton Sound Regional Hospital, based in Nome, Alaska contacted the team at Polyseal Insulation (PI), with a potentially dangerous situation. The building was at risk of collapsing due to a massive void beneath it.
Business partners and PI owners Paul Broderson and Matt Wirtanen had to visually investigate very quickly. Nome is only accessible by aircraft, so this job would take a stringent amount of equipment and thorough safety planning. “Most of the city of Nome is built on permafrost, which is ground, including rock or soil, at or below freezing. When working on permafrost, different methods are used like steel piling, which is driven into the ground to provide a means of supporting a building. This enables the ground to maintain a frozen and stable base,” Matt explains.
The hospital is a three story structure supported by pilings, with an entry way, large stairwell, and foyer. “There was a 16-inch concrete slab poured right onto the ground. The slab was supported by a steel structure, so the load bearing wasn’t originally put on the ground. There was also a small layer of insulation board which had been placed between the ground and the slab. This alone was not sufficient enough to prevent melting from the heat of the building,” Matt states.
Permafrost soil contains a lot of water, much like an ice cube that has been mixed with gravel. When the ice melts, the ground drops dramatically. Handling this issue takes quick planning and ingenuity. “Something had to be done, as eventually the permafrost would have melted down to the piling line and the structure would have collapsed, given enough time,” Paul explains.
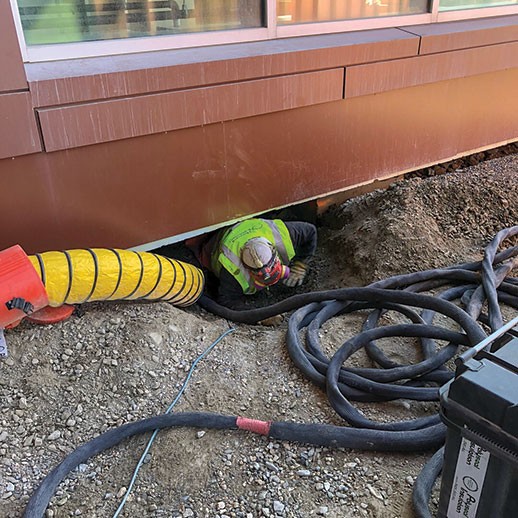
When arriving on sight, the team—consisting of a two-man crew—dug holes around the edge to look inside. They discovered what looked like a big cave under the building. The area mass was 50 by 80 feet. There were pilings that penetrated through the ground, which were indirectly holding up the concrete slab with steel framing. The team noticed how the ground around the piling had melted, causing the ground to sink down to almost 12 feet below the level of the slab, consequently leaving huge voids.
After the team assessed the problem, they outlined a confined space plan, which all crew and personnel had to follow rigorously. Making sure code requirements were adhered to would ensure the safety of the crew and all personnel and patients at the hospital. Special attention was also placed on an extraction plan and restricting the outside work perimeter so no one else but the crew would accidentally access the work zone.
The team knew straight away that they had to use spray foam as opposed to other material such as fiberglass filled cellulose. Paul emphasizes, “We used spray foam to fill the entire void for structural stability and provide insulating power against future permafrost melt from occurring. No other material would provide the same benefit. SPF has the advantage of being fast, non-invasive, and has massive insulating power. It also had the adaptability to fill all voids, gaps, and cracks we found under the structure.” The team installed SPI Eco-Rise 2.5 using a PH-2 proportioner from Polyurethane Machinery Corporation (PMC).
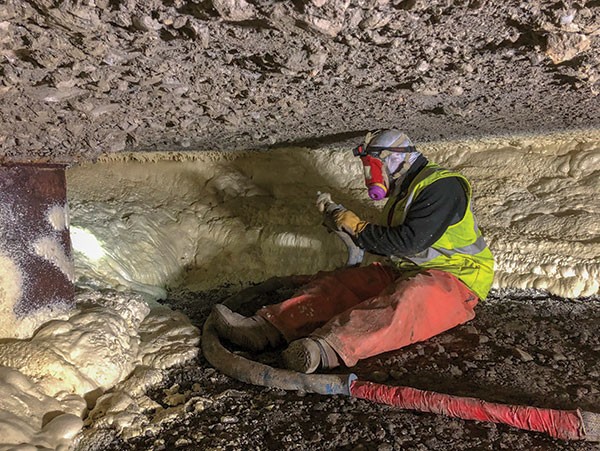
Due to the dangerous and enclosed conditions, it was vital the team was strict on safety gear. They wore hard hats, hi-viz safety vests, full-faced respirators, knee pads, protective suits, proper hand protection, steel-toe footwear, and utilized a dedicated fresh air supply. They also had “toolbox talks” everyday to ensure, plans, progression, and safety at all times.
Once the job was started, it was very difficult to see anything due to the steam generated from the foam. “We would work two hour shifts and with several small trunk ten-inch air movers that pumped air into the hole which helped to carry out a lot of the steam,” Matt recalls. »
Getting in and out of the cavern under the hospital was no small task either. The team had to belly crawl nearly 70 feet. According to Matt, “We had to really plan for this confined space, for example when you spray a large amount of foam there is always a risk of a spontaneous combustion, so that’s why we chose a void fill foam to lower that risk.”
The team also had to take into account wind direction outside. “We didn’t want any fumes or overspray to drift out and potentially interfere with the regular comings and goings of the hospital,” Paul stipulates. The two-man team always had a two-way radio and rotated from one man on the ground outside the cavern and one man spraying. They also had a hose attached to whoever was underneath the building in case there was a need for an emergency evacuation.
Due to the sizeable amount of permafrost on the ground, Nome has a large utility line in place called the utilidor, which is a large group of tunnels, running throughout the city and subsequently has become a playground for huge rats. Sounding like something out of a Stephen King novel, Matt recalls, “These large rats were scuttling around us down there, trying to escape the foam.” The team however were unshakeable as they knew they had to be able to crawl through the large spaces and spray, even when they had the unexpected guests for company.
The Polyseal team managed to spray the smaller areas by rigging a GoPro camera to a pole to make sure the foam injected into smaller areas was properly taken care of. The depth ranged from one to 12 feet of void fill, with an average of three to four inches throughout. They used 11 sets of foam in total, applying it to gravel and tundra moss substrate.
“I’m sure there are tons of spray foam contractors out there that wonder what it would be like to empty tons of foam into a pile to see how big a mound it would make and we got to find out through this job.We would lay on the ground, fill holes, empty an entire set of foam without taking our finger off the trigger,” Matt says with a laugh.
This was indeed a unique job, which required strict planning, a level head, creativity, and adaptability. Matt proudly states, “If it wasn’t for spray foam, the hospital would have needed to be torn down and rebuilt. By using this safe and un-invasive solution, we saved them millions.”
Disqus website name not provided.