Avoiding Homeowner Complaints
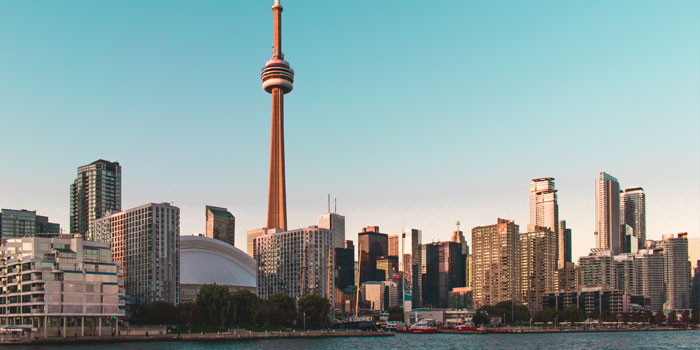
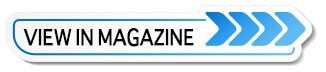
SPRING 2019 – Common mistakes made by contractors can often turn homeowners’ complaints into a business nightmare. Having a spray foam certification will help avoid these oversights and save money and potential catastrophe for all. Caliber Quality Solutions is one such recognized spray foam certification body based in Canada, currently representing manufacturers like Carlisle and Icynene. Quality Assurance Program Director Dave Andre states, “As a third-party Site Quality Assurance Provider, we take our homeowners very seriously. Avoiding complaints is the driving force behind all of our training and quality assurance activities.”
When issues do arise, it’s often necessary to touch-up and repair the installation. In some rare cases, it might be necessary to completely remove the improperly installed material and reinstall it. To prevent disastrous events from occurring, it’s best to avoid the five following pitfalls.
- EXCEEDING MAXIMUM PASS THICKNESS // Exceeding the maximum pass thickness recommendations of the manufacturer can be disastrous. The care and skill of the installer often shows up in spraying materials too thick at one time. In most cases, manufacturers set out maximum pass thicknesses of two to three inches. If an installer exceeds the thickness, the foam may shrink, give off odors or have other physical problems. Andre adds, “Manufacturers set these requirements for good reasons and poorly trained or careless installers are doing you no favors by cutting corners.”
- USING NON-CERTIFIED INSTALLERS // Using installers that are not properly trained and certified is a major liability that can put the whole project at risk for the contractor. Canadian Codes and Standards require the use of properly trained and certified installers, in accordance with the current applicable standards. Requesting the proof of certification should be one of the first things stipulated by the building official, general contractor, home owner, or design professional. Usually the contractor will be able to provide you with their unique wallet card as proof they are qualified.
The installers must have the knowledge, skills, and abilities required to install the specific product in the different applications by successfully completing the certification training. This training is offered by the certification bodies recognized by Canadian Construction Materials Centre (CCMC), such as Caliber Quality Solutions, CUFCA, UFC, or Building Professionals. - NO CONTRACT // Professional contractors and smart homeowners always work with a written contract that includes a detailed scope of the work and specifies exactly what both parties have agreed to. The CAN/ULC S718 Standard mandates that the contractor have a written contract for the work performed. Including information like:
• The name and CCMC listing number of the material being installed
• The thickness–total R-value being installed
• Health and safety recommendations (i.e. vacate and ventilate the work area, during spray foam application, etc.)
A contract is the best protection to ensure things go as planned, and it’s a valuable advantage to using a professional contractor. If there is a homeowner complaint and there is no contract in place, it is more difficult to pinpoint the mutually agreed understanding of the agreed project span and the performance expectations. Proceeding without a contract puts a business at a huge risk because there is no clear identification on the scale of the project and owner expectations. - NO DAILY WORK RECORD // In Canada, the “Applicable Standards Mandate” implies that the contractor completes a daily work record (DWR) at the beginning of each day. It logs each time a material batch is changed and each different job site location. The daily work record contains information on the job site, date, material used, name of the installer, certification number, conditions of application, environmental conditions, results of the testing completed on site, and whether the material used has been evaluated by a third party (i.e. CCMC).
The DWR protects the contractor and it provides evidence to all parties that the spray foam has been installed correctly—in accordance with the “Applicable Standards and Manufacturers” installation guidelines. The DWR is the key document that agencies like Caliber rely on as the third party to confirm the installation conditions, as we were not originally physically present. Without a DWR, the contractor cannot demonstrate that appropriate quality control was carried out during the actual installation. - LACK OF DESIGN REVIEW // Typically, spray foam is not the only insulation or air sealing material used on a building. Design review provides the opportunity to identify where there will be significant installation challenges for the contractor. The design review acts as an early warning of issues and concerns. In addition, it provides the opportunity to identify tie-in details where there maybe uncertainty or lack of clarity regarding responsibility, sequencing, and follow-up on tie-in details. For instance, does caulking or a flashing tie-in need to happen before or after the application of spray foam. Without design review input, the contractor is implicitly accepting the site conditions by the application of the product and any costs associated with subsequent removal and/or reinstallation.
Disqus website name not provided.