Battle-Ready Barriers
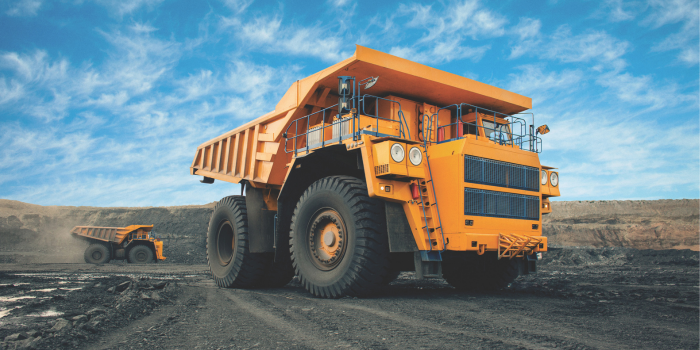
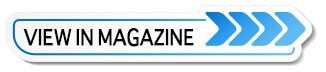
Spray Foam Magazine – Spring 2025 – On a mining site, everything feels alive with the sounds of digging and grinding, punctuated by the occasional cracks, pops, and shrieks from the massive machinery in and around the mining pit. A dragline bucket swings forward and sinks its steel jaws into the earth, tearing through layers of rock and soil like an ore-hungry predator. The impact of each scoop is enough to warp the unprotected metal over time. Nearby, a conveyor belt rattles and groans under the weight of raw material, each stone a tiny blade eating away at each surface it passes over.
ArmorThane’s Operations Director Hank Strathman and Marketing Director Troy Bacon shared a seemingly endless list of uses for the coatings, from lining truck beds to covering blast-resistant panels. It’s not just for looks, these coatings can generate real cost-savings by prolonging the life of expensive mining equipment.
“Everything the machinery gets used for accelerates the time it takes to degrade and break down,” Strathman said. “The coatings protect the equipment for much longer and can save mine operators significant money in the long run.”
Savings & Safety
Where the mine seeks to break and destroy, these unstoppable coatings fight back, acting as an impermeable second skin anywhere it’s applied. Relentless wear from high-impact forces, corrosion from moisture and chemicals, and exposure to harsh environmental conditions represent a small sample of the regular beating that mining equipment and structural components are designed to endure.
The coatings can be applied to virtually any nook and cranny on the mining site to extend the life of critical assets, reduce maintenance costs, and improve safety. And these coatings are as versatile as they are tough.
Dredging equipment, for example, faces a dual threat from constant water exposure as well as contact with abrasive materials, but ArmorThane addresses both these concerns in a single application. Likewise, it’s frequently used to coat ore shoots, huge drill bits, flotation cells, and the insides of chemical slurry tanks. Best of all, the coatings are entirely stable once it dries and will not react with or leach into other substances, be it water or chemical slurries.
Beyond their uses in protecting material-handling equipment and mining tools, polyurea and urethane coatings are also used to bring safety to the next level. There’s no shortage of workplace hazards to be found on a mining site, so anything that can reduce or eliminate incidents is a welcome solution.
As an example, the coatings are frequently used as an explosion-proof barrier coating in underground mining environments. The coating reinforces tunnel walls and other structural elements in high-risk work zones. This can be lifesaving in the event of a blast or cave-in, as it can help keep damaged walls intact long enough for workers to escape or be rescued.
While explosion risks are typically low, at a mining site it’s never zero—and for many operators, having coatings in key areas is worth it for the peace of mind alone.
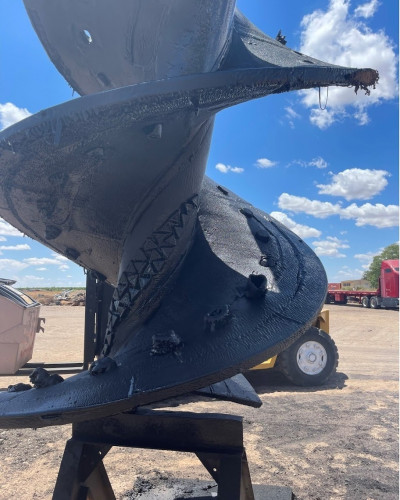
A mining drill coated with ArmorThane. The coating can extend the drill’s lifetime by slowing down wear and tear.
Prepare for Protection
Installing polyurea coatings to mining equipment and job site infrastructure requires some legwork to ensure optimal adhesion.
Preparing surfaces for these specialized coatings entails cleaning, sanding, or sandblasting as necessary to remove debris. While the surface must be clean, it is also vital that it is not too smooth—sanding or otherwise roughing up the surface helps the coating bond more effectively, which in turn can help it last longer between recoats.
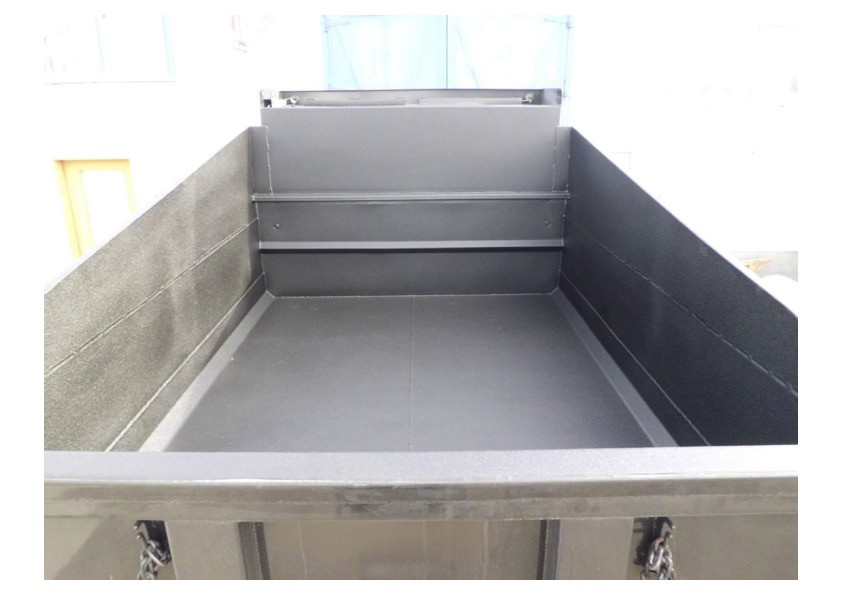
A dump truck and its bed after being coated with an ArmorThane lining
Outside of surface prep, the environmental conditions also must be just right, for example, not too cold or humid. ArmorThane’s coating technology dries rapidly, allowing freshly coated equipment back in operation with minimal downtime.
“The actual spraying process is the quickest part of the job,” Strathman explains. “It’s the prep work that takes the most time, but once that’s done, the coatings go on quickly and cure fast.”
Getting It Done
While spraying these coatings, the applicators wear the standard PPE found on any spray foam rig, including a supplied-air respirator, face mask, disposable gloves, and hooded coveralls. While working on a live mine site, they are typically also expected to wear hardhats and steel toed boots, depending on site-specific hazards.
To provide a visual clue and help with long-term coating maintenance, it’s recommended to apply a two-layer system—the first coat in a bright color, like yellow, with a neutral color, like gray, added over top. It’s a simple way for equipment operators and mine workers to know when something needs to be recoated.
“They make these fancy calipers and such to test the coating’s strength, but let’s face it, the guys working these mines are busy enough,” Strathman explains. “Doing two layers takes away the guesswork, because if you see yellow streaks where it used to be all grey, then you know it’s time to recoat.”
The dual-coating technique is yet another example of the company’s willingness to find a solution for their customer’s equipment degradation woes that saves time and effort, rather than add stress.
Everyone Wins
The many uses for coatings in an environment as intense as a mining site prove that durability is everything. Whether its shielding truck beds and drill bits against corrosion, reinforcing wall panels and blast-barriers, or fortifying ore shoots and conveyor belts, this polyurea and urethane coating technology is ready to brave the unfriendliest conditions.
By leveraging their existing equipment and expertise, spray foam applicators can pivot into a high-demand market where their skills are valued and essential. For mining site foremen and managers, investing in protective coatings means reducing downtime, extending equipment life, and championing site safety. Everywhere the battle rages, ArmorThane holds the line, turning the chaos of the mine into another day’s work.
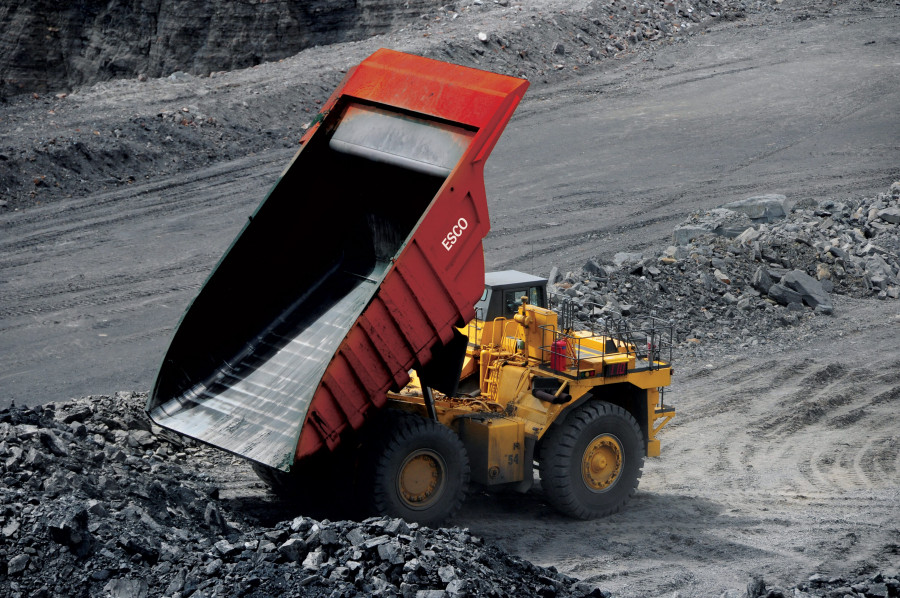
The dump truck returns to the work site, ready to haul rocks, ore, and other abrasive materials after having their beds lined with ArmorThane’s coatings.
Published by Spray Foam Magazine
SprayFoam / Spray Foam Insulation
Disqus website name not provided.