Barn to be Wild
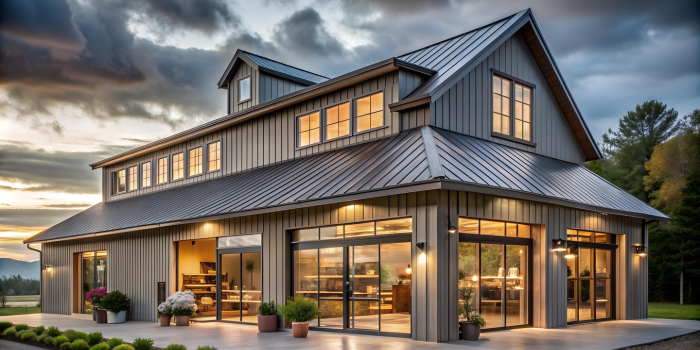
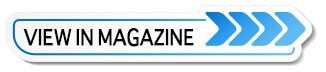
Spray Foam Magazine – Spring Issue 2025 – “Were you raised in a barn?” is usually meant as a disparaging jab, implying a lack of sophistication and class. But that phrase seems short-sighted now that modern construction methods and materials can transform barns into spacious, comfortable homes to rival any mansion or condo. A step beyond the trendy modern farmhouse interior decorating trend—barndominiums, or “barndos,” are all the rage, allowing residents to live luxuriously rural lifestyles. These structures offer rustic charm with ample space for working and playing. But as with all large, open structures, barndos can become an energy headache if not adequately insulated—and not all insulation methods are created equally. Sometimes, it takes a team of professionals to mix and match insulation systems to find the best value for a particular project.
Shelbyville, Kentucky-based Spray-Tec Inc. has extensive experience insulating these unique homes, taking care to seal the immense surface area against moisture and air gaps. In the last couple years, they’ve foamed two notable barndo projects. The first is Underwood Pole Barn in Indiana, which involved spraying the walls with three and a half inches of Gaco EZ Spray open-cell foam (now Enverge) across 9,500 sq. ft. in addition to installing blown-in insulation to the attic. A year later, they tackled the 2,700-sq.-ft. Bagdad Barndominium in Kentucky, applying five inches of NCFI’s InsulStar Light open-cell foam to its walls.
Though the two projects varied considerably in size and budget, Spray-Tec came up with economical solutions for both that would insulate the large, open-concept barndos, keeping indoor ambient temperatures comfortable and energy bills low.
A State Away: Underwood Pole Barn
In February 2023, Spray-Tec traveled an hour north to Underwood, Indiana, where they would spend five and a half days installing a dual open-cell foam and blow-in insulation system to Underwood Pole Barn.
The owner was interested in SPF for its efficiency but had a strict budget to stick to on this new construction build. This was hardly a challenge for Spray-Tec, whose lead estimator Anthony Palmer worked closely with the customer to develop a cost-effective insulation plan.
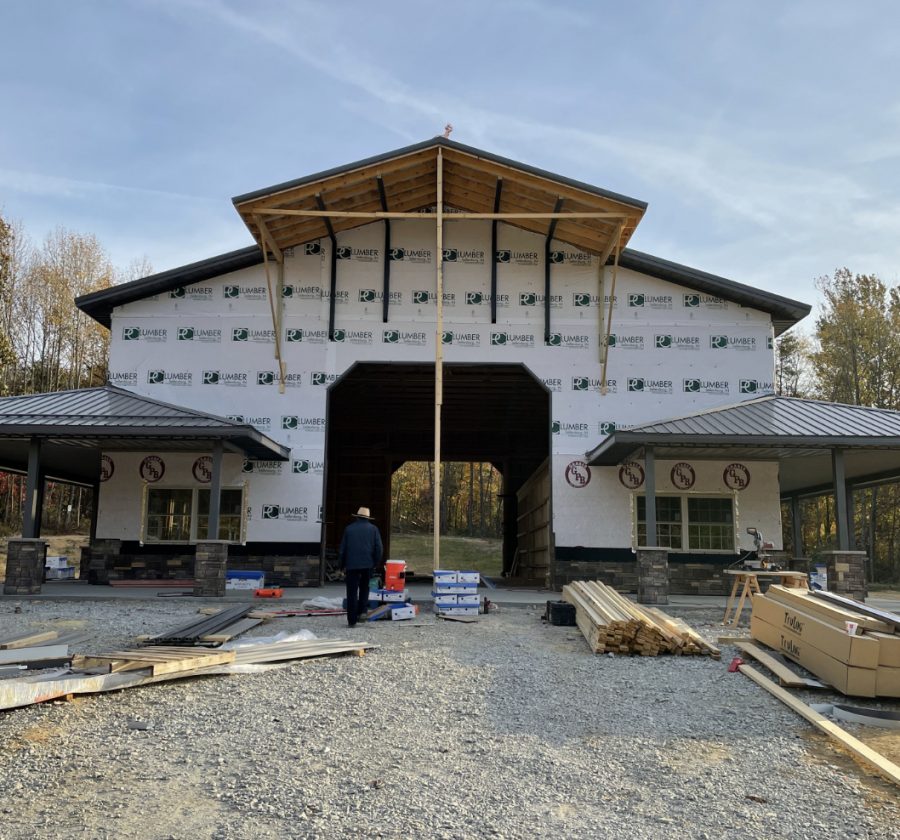
An exterior and interior shot of Underwood Pole Barn before the foam install.
They decided to install Gaco EZ Spray open-cell foam (now Enverge) in the exterior wall cavities and also blow in loose-fill fiberglass insulation in the attic. Using both insulation methods maximized the efficiency and affordability for the homeowner by targeting energy loss where it counts.
Once on-site, Production Manager Quin Heisler and Crew Leader Abel Reyes led the three-man spray team. Since the barndo was in the midst of finishing construction, other general contractors had already prepared the wall cavities with wooden board framing before Spray-Tec arrived. Since the board was newly installed and free of debris and defects, it saved the Spray-Tec team valuable prep time. Not to mention, the open-cell foam would have no trouble adhering to it for the long haul.
With nothing to clean, the team got straight to work on the rest of the prep work, which involved masking off all doors, windows, and other fixtures to shield from overspray—a standard but critical step. After sufficiently protecting the site, they hastened to protect themselves, and suited up in protective coveralls, full-face respirators, and gloves before firing up the Graco H-40 proportioner.
They sprayed three and a half inches of open-cell foam into the four exterior wall cavities and two gable-end walls.
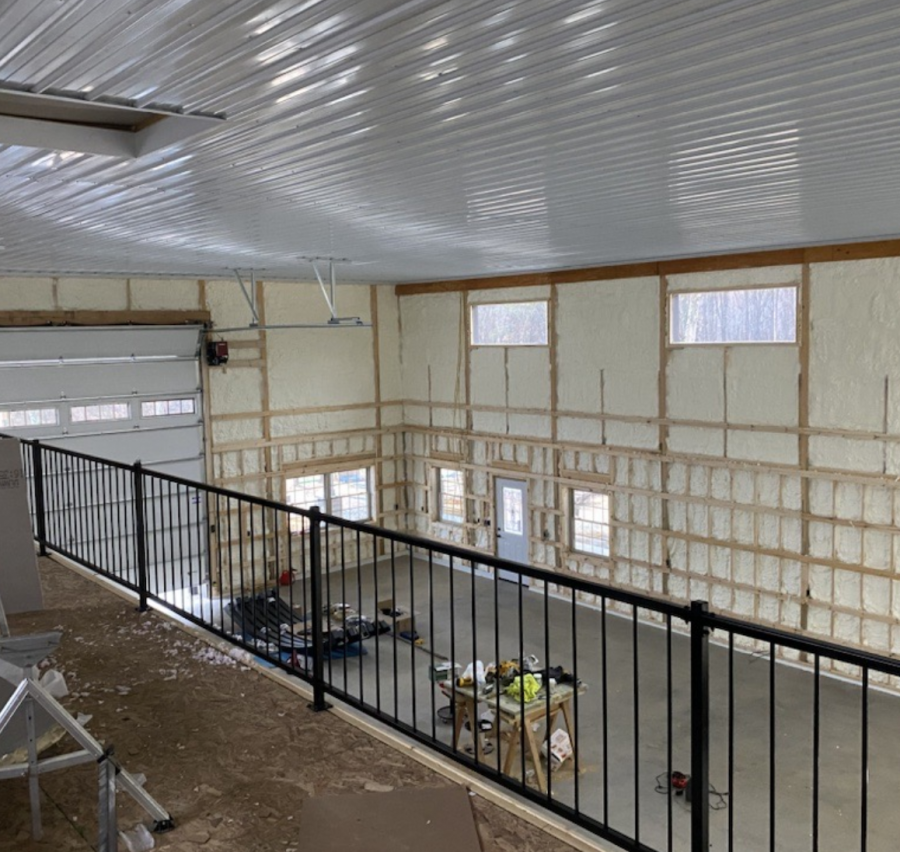
A closer look at the Gaco EZ Spray open-cell foam (now Enverge) on the exterior walls of Underwood Pole Barn, smoothed to near- perfection and soon to be covered.
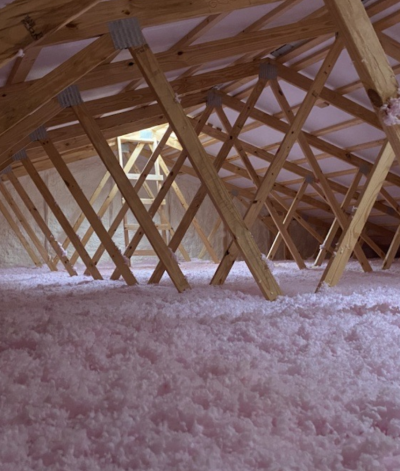
The attic of Underwood Pole Barn, filled with loose fill insulation.
After they’d finished spraying and given the foam enough time set, they meticulously scraped the studs to create a flat surface for the general contractor to install wall covering material. The final step was to clean up any errant pieces of foam that may have fallen off as a by-product of smoothing it down, leaving the site neat and clean.
A short time later, three Spray-Tec employees returned as planned to install R-38 loose-fill insulation in the attic. Compared to the foam installation, this process was simpler. Using a Krendl Fiber Machine, they aimed the hose and distributed the fluffy, pink material evenly around all corners of the attic.
The Underwood Pole Barn project was a quick process, taking less than a week from start to finish. With the attic insulated, the barndo reached a total of R-52, far exceeding insulation expectations for a structure of its size, with the added bonus of being well under-budget.
In the Neighborhood: Bagdad Barndominium
Word travels fast when companies do excellent work. Never long to rest on their laurels, Spray-Tec soon took on another barndominium project in January 2024, this time right down the road in Bagdad, Kentucky. D&B Construction was building Bagdad Barndominium, and they subcontracted Spray-Tec to handle the insulation side of things.
Unlike the previous barndo project, this one had multiple trades working on-site, making job site coordination and safety even more critical.
With safety at the top of their mind, Heisler and Crew Leader Mariano Perez began securing the indoor work area by setting up fans for ventilation, posting cautionary signage, and using cones and lights to alert other trades to the ongoing spray foam application and keep them away from the area. As usual, they used sheets of plastic to mask off the home’s windows, doors, and fixtures to prevent damage from overspray.
Once suited up in their own PPE, the team got to work foaming the walls and gables. They applied five inches of NCFI’s InsulStar Light open-cell foam to the barndo’s four exterior walls and two gable-end walls lined with a Tyvek vapor barrier, achieving a value of R-20. To ensure the barndo was properly sealed, they used a can of Soudal Soudafoam low expansion foam to fill any small voids around windows and doors, preventing air leaks in these vulnerable areas. The Soudal Soudafoam was ideal for this delicate detail work, as it allowed greater precision and neatness when filling in the narrow gaps.
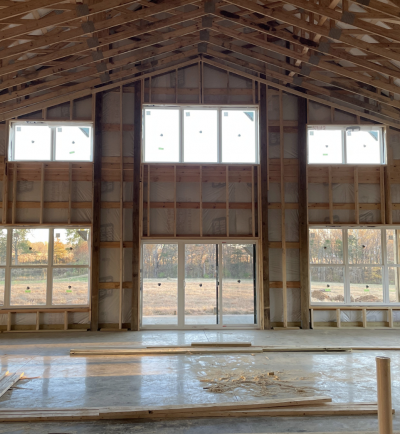
Inside the Bagdad barndo, before Spray-Tec installed NCFI’s InsulStar Light open-cell foam to the exterior wall gaps.
Once the open-cell foam cured, the team carefully scraped the foam off the wall studs, filing it down to create a smooth surface. Scraping and smoothing the foam on the studs served to flatten the open-cell foam enough that the general contractor could install siding flush to the walls, sandwiching the foam out-of-site between the barndo’s interior and exterior walls.
After cleaning up the excess foam scrapings and debris from the ground, the job was complete, and the Spray-Tec team left behind yet another well-insulated, energy-efficient barndo. Like the Underwood Pole Barn project, the Bagdad Barndominium took less than a week to complete, despite having to coordinate with and work around other tradespeople.
All in a Sprays Work
A knowledgeable insulation team does more than install foam—they’re all about understanding client needs, working within budgets, and coordinating with other trades to get the job done right. The energy-efficiency solutions used for each barndo project were well-suited to the respective structure’s design and climate, promising to keep the homeowners comfortable regardless of season or weather. Whether it’s finding cost-effective solutions or guaranteeing airtight seals in high-traffic job sites, Spray-Tec is the cream of the crop for barndominium insulation and beyond.
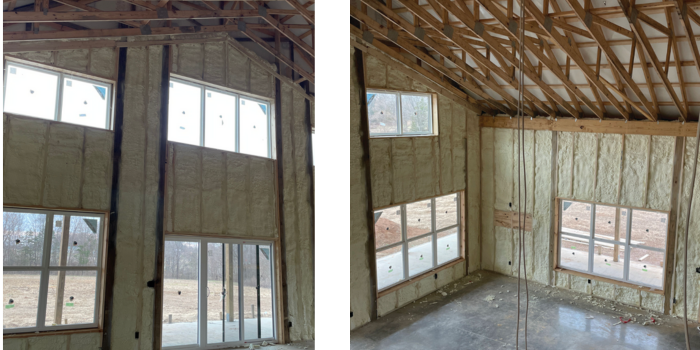
Inside the Bagdad barndo, after installing the foam. Next, the Spray-Tec team will clean up the debris left over from scraping the foam flat.
Disqus website name not provided.