A Different Kind of Rocky Road
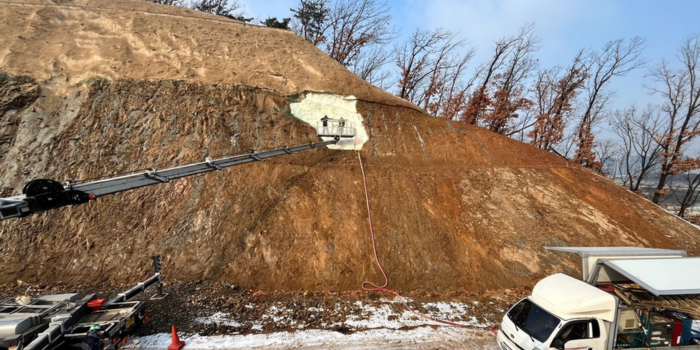
Spray Foam Magazine – Spring 2025 – While the practice of injecting spray foam underground to level out the earth is a common technique, using spray foam to repair above-ground natural rock formations is decidedly less common.
In January 2025, South Korea-based Joong-ang Insulation (JAINS) got a surprising call from the Korea Expressway Corporation (KEC). KEC was inquiring about the viability of using spray foam to repair a mountainside and prevent rock slides.
The JAINS crew loves challenges, so they accepted the job and vowed to solve the unconventional dilemma. In doing so, they took Grizzly Gold closed-cell spray foam to new heights.
Moving Mountains by Stopping Rockslides
They’d be working at the site of an under-construction highway that, when finished, would weave through the mountainous South Korean countryside.
The mountain in need of repair had crumbled away during several small-scale rockslides, leaving an unstable void of nearly 500 cubic feet (approximately 14 cubic meters) in the rock face. Being under constant threat of rockslides is not conducive to a well-traveled highway, and KEC wanted a solution that would stabilize the damaged rockface and prevent further erosion from becoming a future problem. SPF was the most flexible and economical option, as it only required a small team to install and didn’t necessitate any heavy machinery or hard labor.
The spray foam field team that day was made up of JAINS President Woong nyon Kim and lead applicator Will Min Hyoung Kim. The two set out to the site prepared to ascend over 200 feet (about 60 meters) using an aerial lift platform (cherry-picker), and a hose with a length of about 255 feet (78 meters).
While the task at hand may have looked precarious to any onlookers who happened to catch a glimpse, Shinil Kim, JAINS General Manager, reported that the two men up on the lift had a more stress-free experience than one might expect from spending a workday high up in the air.
“It was easy work,” said Shinil Kim, General Manager of JAINS, adding, “The weather was dry, too.”
Kim’s optimism is a reflection of the company’s many years of combined expertise and ability to brainstorm creative solutions. Their experiences have afforded them the reputation, confidence, and know-how to pull off such innovative spray foam applications.
JAINS has been operating since 2011 and has scaled to a core team of seven, with three different rigs each armed with a different reactor—a Gusmer H-20, Graco E-20, and the Graco H-30 used for the mountain repair gig. Where others might have preferred to stick to safe jobs, like foaming attics and crawlspaces, the JAINS crew broke out of their comfort zone and the risk paid off.
Rolling In and Setting Up
On the day of the mountain repair, the two-man team set out to the expressway construction site. Outside, it was a cool 26°F (-3°C), but the crew was not worried about the frosty temperatures because they figured that the direct sunlight shining on the mountain throughout the day would warm the site up and help the foam cure correctly. This assumption proved correct, and they also didn’t experience any humidity problems. The dry air, warm sunshine, and secluded site made for promising work conditions.
With their rig parked at the base of the mountain, the team fired up the Graco H-30, unwound the hose, and readied the spray gun. Since they were spraying such a large area, they opted to use a 5252 tip for optimal control and coverage. Before extending the cherry picker, they secured themselves with safety harnesses and made sure all their equipment was secured to the lift’s platform.
This job also necessitated the inclusion of a hard-hat in addition to the standard sprayer PPE of protective hooded coveralls, knee pads, gloves, and full-face respirator masks. Wearing hard hats was a reasonable precaution—they’d been called to the scene because of rockslides after all. Once they’d made sure they hadn’t left any PPE or equipment down on the ground, they got onto the lift’s platform and began the ascent up the mountain.
Rocking Out & Spraying On
For the two-man JAINS crew, this job was a picnic with a view. There was little for them to do in the way of prep work once they got up there. Overspray wasn’t much of a concern since they were so high up and far away from anything and didn’t need to hang any plastic masking. This simplified the job even more, since all they had to do was get in, spray the foam, and go home, with minimal time needed for prep and cleanup.
Days earlier, KEC workers had installed metal rebar and green chain link fencing material was secured at various points around the perimeter. These metal facets would lend the foam something to grip onto in addition to the craggy, exposed boulders and tightly compacted dirt.
“There were more rocks and stones than dirt, so it stuck well,” said Shinil, adding that the rebar and fencing was still helpful even if the foam had little trouble adhering to the stone on its own. Not to mention, the fencing and rebar gave the applicators a visual cue to follow with their spray guns.
To apply the closed-cell foam evenly and blend it with the mountain’s natural contours, the applicators started at the center and worked their way out toward the rocky permitter. As the foam expanded, they continued to layer the foam to fill in gaps and keep the density uniform.
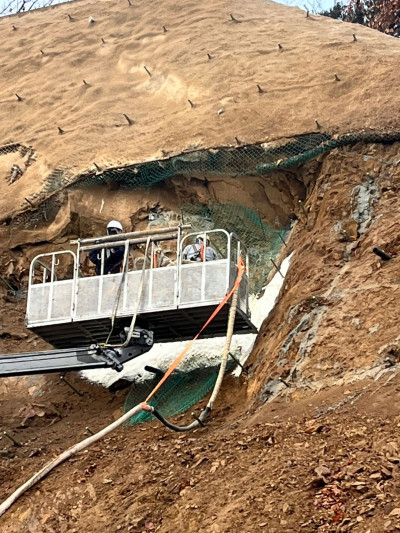
During, the applicators began filling in the void with foam, working from the center outward.
One of the key advantages to using closed-cell spray foam is its ability to form a dense, rigid structure once cured, filling in gaps and reinforcing against future erosion and unstable earth. After the spray work was finished, the light-yellow foam patch stood out against the reddish dirt of the mountainside, but this stark difference wouldn’t be noticeable once the highway construction project was complete.
Upward & Onward
The team at Joong-ang Insulation successfully filled in a nearly 500-sq.-ft. gash in the side of a natural mountain in a single day, using two sets of Grizzly Gold closed-cell foam.
Stepping back to observe their handiwork reveals a smooth, natural-looking facade where there were once jagged edges and unstable dirt clods. Except for the light color, the untrained eye would hardly know it was spray foam. The mountain repair project reinforced JAINS reputation as innovators and highlighted spray foam’s versatility as a building product beyond traditional insulation purposes.
In early March, JAINS launched a new website, where the team hopes to continue showcasing the many things spray foam can do, from insulating homes to fixing the sides of mountains.
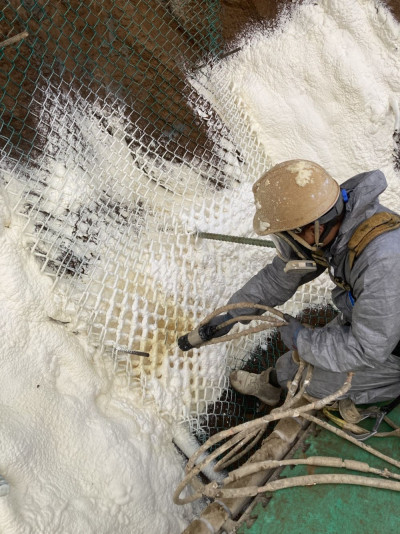
The metal rebar and green fencing material provided a visual guideline and helped the foam adhere to the rockface.
Published by Spray Foam Magazine
SprayFoam / Spray Foam Insulation
Disqus website name not provided.