All Bubble, No Trouble
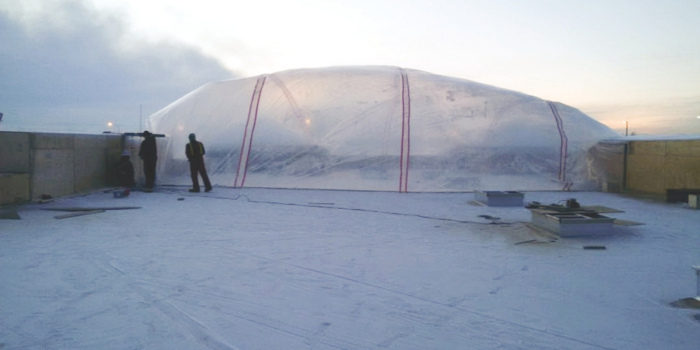
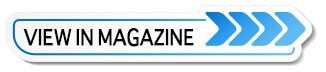
Spray Foam Magazine – Spring 2025 – At Spray Foam Magazine, we’re always on the lookout for the clever solutions that the masters of the trade have used to make tough jobs easier, or doable in the first place. When we heard about how Brad Redl of Enviro Home in Alberta, Canada, installed Polysource Industries’ Roof Armor Heat Shield closed-cell foam and Roof Armor HD Silver polyurea coating on a 13,000-sq.-ft. roof in below-freezing temperatures, we had to learn more. The secret? A custom-built, heated bubble.
The story begins about a decade ago in Grand Prairie, Alberta, Canada, where exterior foam installs are a seasonal challenge; as temperatures drop the race against time begins. Enviro Home Inc. bid on a commercial roof resealing job earlier in the season, but the client hadn’t accepted and given the go-ahead until December. Condensation and wind can create challenges that make projects nearly impossible until the weather warms back up. Many foam applicators start taking indoor jobs only around this time, saving outdoor gigs for late in the season.
Closed-cell foam has to be applied within a certain temperature range, or it won’t set correctly, resulting in wasted materials, labor, and time. Despite these conditions, Redl had a long-standing relationship with the client going back nearly 17 years. That trust afforded him the flexibility to innovate rather than postpone or walk away from the project.
“I don’t like to say no in general, so I got my guys together and said, ‘Well, how the hell are we gonna pull this off?’” said Redl. They didn’t need to look too far for their answer.
Pulling it off: Build-A-Bubble
Back at the shop, Redl and his team brainstormed their plan, bouncing ideas off each other to decide what would or wouldn’t work, and trying to work with the materials they already had on hand. After some trial and error, they were sure the bubble was the way to go.
It was constructed using fastened sheets of lightweight yet durable six-mil polyethylene plastic. The team used spray adhesive on the poly’s overlap to create the necessary size, and then wrapped each end of the sheet around two-by-fours. To both inflate the bubble and provide the necessary warmth, they deployed several 350,000 BTU heaters. It worked like a charm. After test driving the bubble prototype at the shop, Redl decided they were ready for the big time.
They soon headed out to the job site, where they were greeted by the best snow banks and freezing wind gusts that Northern Alberta has to offer. Outside temperatures were easily in the negatives—both Fahrenheit and Celsius—with no chance of rising even a couple degrees.
The team quickly got to work setting up the bubble, and with the client’s permission bolted the two-by-fours to the roof deck. They fired up the heaters, and the air inside of the inflated bubble eventually reached a comfortable room temperature ambience. The poly sheets ballooned up into the air, puffing up above the roof deck like a loaf of bread. On the outside, it was barely visible against the gloomy Alberta skies, but on the inside, seeing was believing.
Once the bubble was inflated, it quickly began melting the foot of snow covering the roof. The snow melted, leaving behind a waterlogged wooden roof deck, too soggy to install foam right away. But it was all part of the plan.
In addition to keeping the heaters running under the bubble, Enviro Home brought in industrial dehumidifiers. Within three days, the once-soaked plywood roof was completely dry and ready for the Roof Armor Heat Shield system.
A major challenge when using the bubble was its sheer size. The team couldn’t encapsulate the entire roof at once, so they had to move the dome around, splitting the work into two phases. While the first half of the project allowed them to fasten the two-by-fours to the roof on all four sides of the poly sheet, the second phase was trickier.
They couldn’t secure the bubble to one side of the roof without the newly installed foam system, which meant they’d have to secure the bubble on three sides instead of four. To maintain stability, Redl and his team switched to using six-by-six timbers instead of two-by-fours.
“Using six-by-sixes added extra weight,” said Redl, “It worked perfectly to hold the bubble down without messing up our previous work.”
Getting Prepped & Firing Up
Aside from enabling work in frigid temperatures, the bubble offers other advantages, like simplifying site prep. Foam overspray can be difficult to control, especially in windy conditions, but according to Redl, the bubble is unbeatable protection.
“You can get overspray on cars a block away in any direction if you’re not careful, but with a bubble, there’s zero chance of that happening,” he said.
The setup also improves ventilation by design. To keep fresh air circulating inside the bubble, Redl’s team cut a vent at the top, ensuring consistent airflow while maintaining internal temperatures. Additionally, crew wore full PPE while spraying, such as coveralls, disposable gloves, and a Martech Supplied Air System.
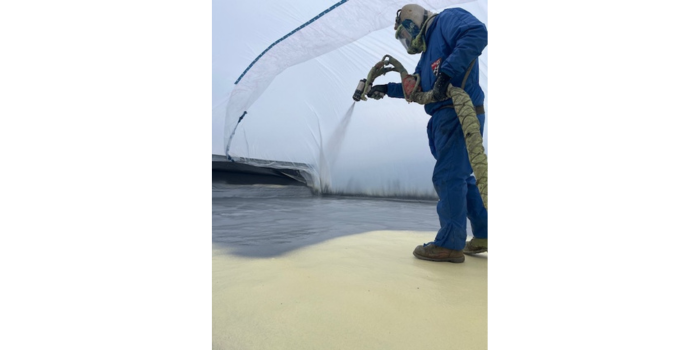
Industry veteran Chris Biermann suggested using Brad Redl’s bubble technique to apply polyurea coating to a roof in wintry weather.
To install the Polysource Roof Armor Heat Shield closed-cell foam, they used a Graco H-40. After the foam had set, they switched to a Graco H-XP3 proportioner system to apply the Roof Armor HD Silver polyurea coating, also by Polysource Industries.
It took about two weeks to complete the project from start to finish, and everyone involved was impressed they’d pulled it off, though not exactly surprised.
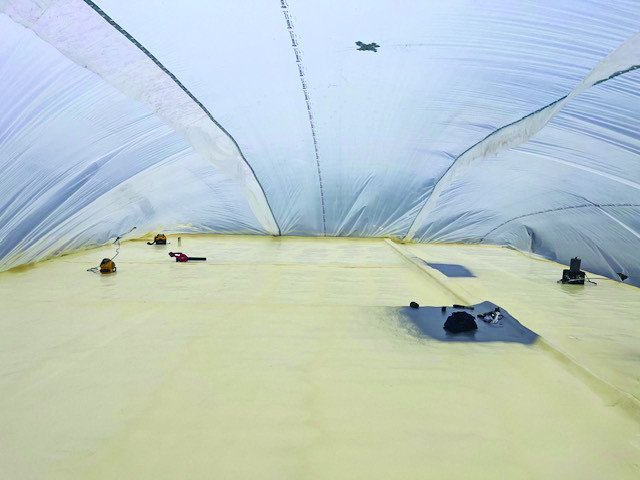
The bubble in all its glory—6 mil plastic sheeting, adhesive, a few two by fours, and heated blowers bring negative outdoor temperatures up to room temperature.
The Redl Bubble Legacy Lives On
As First Vice Chair of Canadian Urethane Foam Contractors Association (CUFCA) and a board member since 2008, Redl is not a strange face around the industry. Though it’s been a decade since Redl devised that first bubble, his ingenuity has only helped his reputation grow.
Since 2015, he and his team have completed dozens of jobs using a bubble setup, and his method has been widely shared online—even going semi-viral in some spray foam circles.
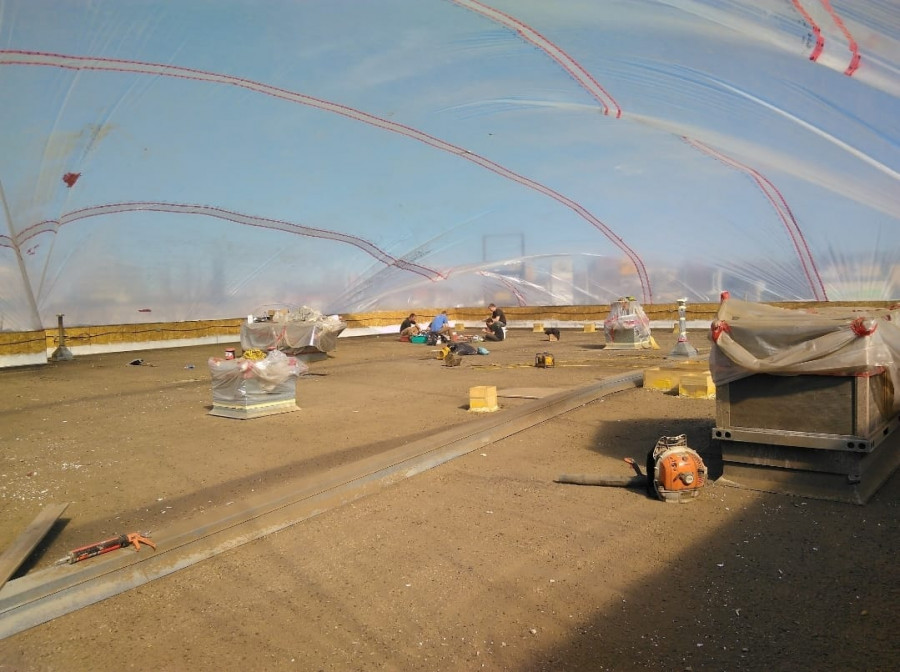
From the outside, Redl’s famous bubble is barely noticeable against the gloomy winter skies. On the inside, it’s warm enough to melt snow and cure foam and coatings.
Chris Biermann was one person who happened to see the viral bubble post years ago and it made an impression on him. During Biermann’s tenure as a technical representative at Genyk, he suggested on three different occasions that his spray foam contractor clients use Redl’s technique. With Biermann’s guidance, a contractor even managing to spray a 3,700-sq.-ft. roof in the dead of an Okanagan Valley, BC winter thanks to the bubble’s warmth.
“I’d always wondered how to keep taking jobs in poor weather,” Biermann said. “Seeing Brad’s bubble, I realized where there’s a will, there really is a way.”
Each time Biermann would visit a job where they were using the bubble technique, he’d snap a picture and give Redl a friendly tag on Facebook. One particular Facebook post by Biermann featured a massive dome-like enclosure over a flat commercial roof. Biermann’s caption read: “Another Brad Redl trademarked bubble for a 3,700-sq.-ft. winter roof job. Now for the polyurea. Outside temps are -5° Celsius. Inside the bubble is 22° C. #genyk #techlife.”
When asked about his professional relationship with Biermann, Redl admitted he’d never actually met Biermann in person, and had only interacted online. Still, he’s grateful for the shoutout and that his idea has helped others.
“We had a lot of people sharing that bubble post and saying they were going to steal the idea, so I’d joke, ‘I’m sorry, you can’t, it’s trademarked,’” Redl laughs. “Now some people like Chris tag me whenever they make their own bubble, a ‘trademarked Redl Bubble.’”
The lasting impact of Redl’s bubble technique proves that extreme weather doesn’t have to halt exterior spray foam projects. When wintry temperatures make outdoor jobs seem impossible, an innovative spirit can turn challenges into opportunities.
For those in colder climates looking to extend their work season, Redl’s approach might be just the thing. In the absence of warm, sunny days, the true experts create their own paradise. And that’s one bubble that can’t be burst.
Published by Spray Foam Magazine
SprayFoam / Spray Foam Insulation
Disqus website name not provided.